Esko Digital Flexo Suite cuts costs at Interstate Packaging
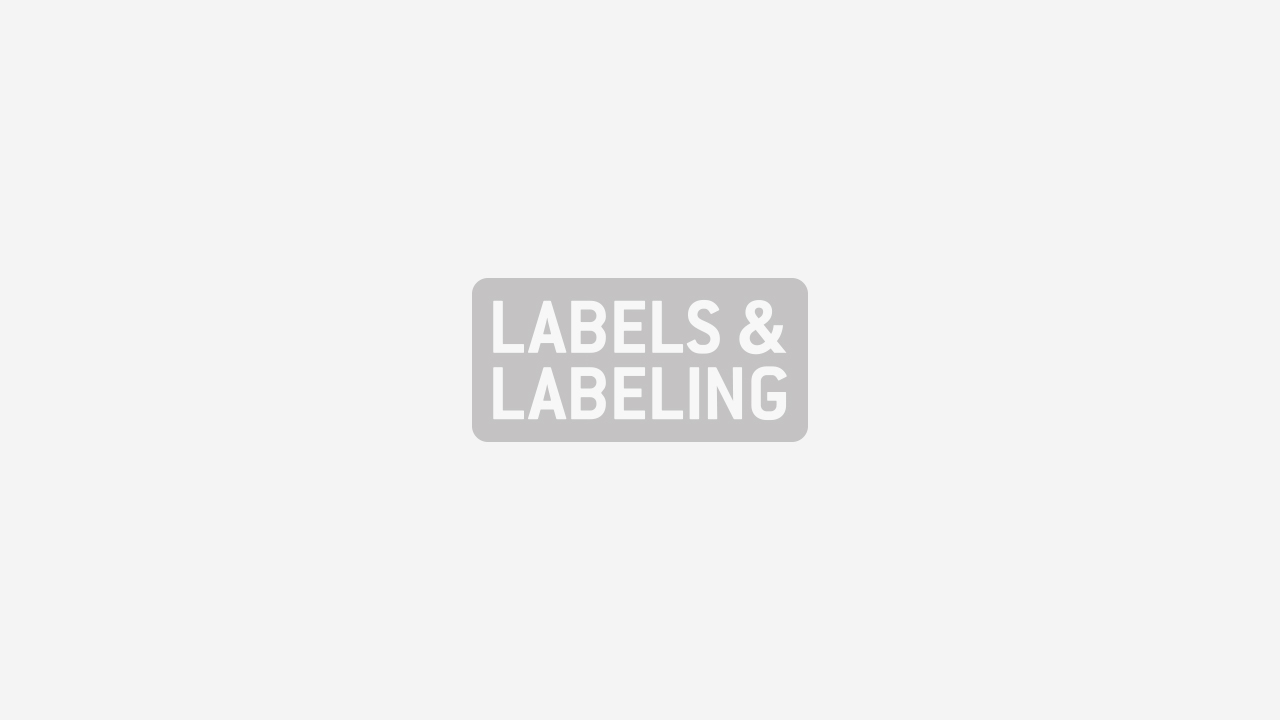
Interstate Packaging says its Tennessee-based platemaking operation has increased throughput and gained significant cost savings using Esko’s Digital Flexo Suite with a Kongsberg XL24 digital finishing table.
The system, connected to a CDI Spark 4835 imager – in operation at the company for nearly five years – is said to have reduced plate waste, eliminated human error and brought automated plate traceability to the company’s flexo plate operation.
Digital Flexo Suite automatically and simultaneously sends optimized plate files to the CDI Spark for imaging and cutting layout data the Kongsberg XL table for precision cutting. The CDI imaging file and the Kongsberg cutting file carry identical names and registration marks that are automatically marked on the flexo plate, for later identification, registration and cutting.
Of the initial push for Digital Flexo Suite’s implementation, Jeff Cassell, graphics manager, commented: ‘Our highest costs, in order, are substrates, ink, and plate material. We felt that with plate material, there were opportunities to reduce costs.’
Along with some other modifications to the platemaking process, such as barcoding plates, the use of Digital Flexo Suite with the Kongsberg table enabled Interstate Graphics to make a 30 percent saving on the amount of plate material used. The single precision cut around the plates allows them to be moved closer together, saving up to seven percent in materials.
Cassell continued: ‘The greater percentage of the savings is the result of the plate numbers etched onto the plate.
‘With multicolor jobs, one plate with incorrect labeling can be troublesome. ‘Now, driven by the Esko workflow and etched by the Kongsberg table, we can assure we are using the right plate for each run.’
Another critical element is the traceability and accountability for each plate. Cassell explained: ‘Each plate has a unique number; that number is logged into a database. The etched number of the plate is placed on the back of the plate. We can go into the database and enter the plate number and find where the plate is in process. Interstate Packaging has over 8,000 active SKUs, averaging eight colors per SKU. We are talking lots of plates. We now know where each plate should be at all times. Let’s say a plate is left out of an envelope. We can go to the database and see if the plate is active or belongs, conversely, in the recycle bin.
‘Thanks to the plate number tattooed on the back of the plates we now have traceability through our MIS system.’
Interstate also uses the Digital Flexo Suite’s Staggered Cut software option, executed with a Kongsberg cutting table, allowing the drafting of a staggered cut line for continuous print. ‘With Digital Flexo Suite, we can cut a plate in a few seconds and it fits the first time.’ The option also eliminates bounce on the press and provides a continuous print without sleeves.
Interstate Packaging produces a lot of flexible packaging, including stand-up pouches. ‘Staggered Cut allows us to reduce the clear area of the sides of the bag (plate gap) in half from 3/16” to 3/32”,’ said Cassell. ‘This is an important visual difference to our marketing clients, but now it doesn’t require a continuous “in the round” plate for backgrounds. Nor, do we incur the extra cost of an in-the-around plate. Having this option has really helped us market to that segment.’
With feedback and adjustments, Interstate hopes to use this more in the future. ‘It works great and saves plate materials and cuts plates closer than with hand cutting, but because of our own marks and bars we can’t fully utilize it yet,’ said Cassell.
Interstate Packaging is currently testing Esko’s HD Flexo high-resolution screening. ‘We are getting nice, high-quality images on our test runs,’ said Cassell. ‘Ninety percent of what has happened in prepress technology in the industry is due to Esko. They have moved these functions from an art to a science. Their 3D and plate preparation software are precise and consistent. They produce hardware that lasts. Very seldom is there downtime – there are no issues.’
Stay up to date
Subscribe to the free Label News newsletter and receive the latest content every week. We'll never share your email address.