Reproflex3 expands plate services with ThermoFlexX 80-D imager
Pre-press specialist Reproflex3 has expanded the production facilities at its Newcastle site with the installation of the UK’s second dual-head ThermoFlexX 80-D digital flexo plate imager.
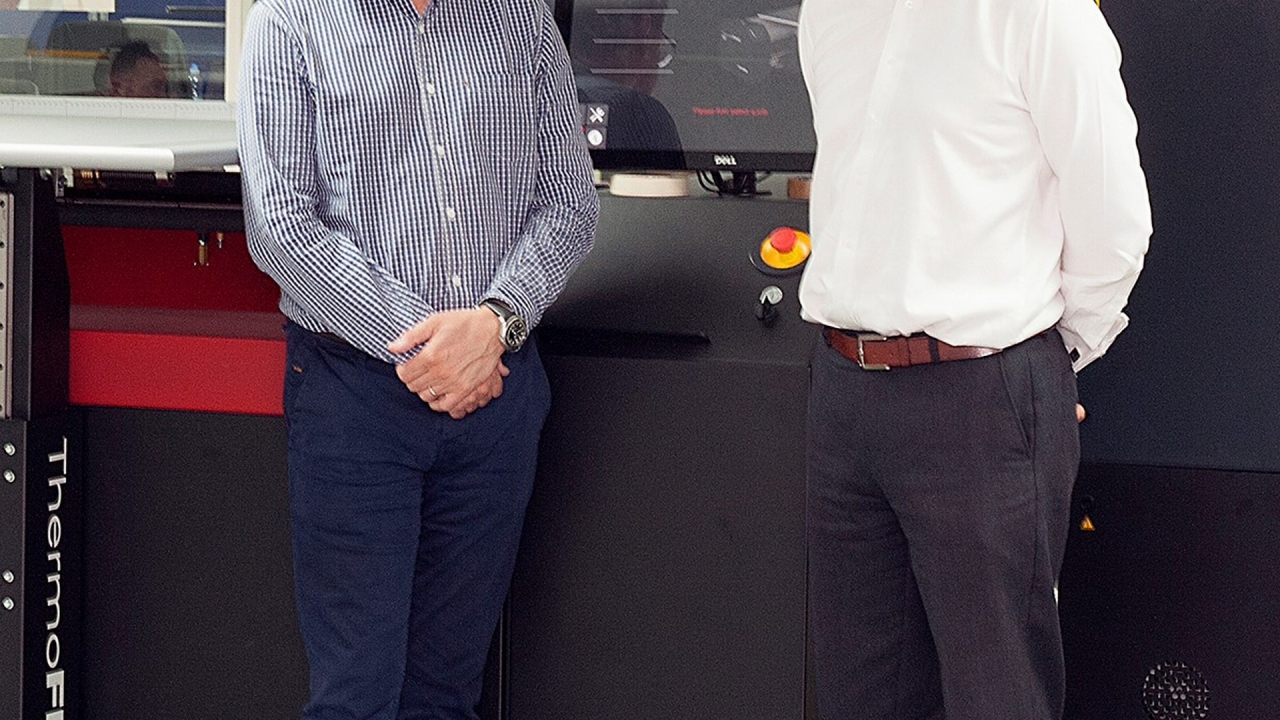
The ThermoFlexX 80-D offers Reproflex3 an imaging speed of 12 sqm an hour, with the ability to output at resolutions of up to 5080 dpi, enabling the finest detailed work to be produced. There is also the ability to mix resolutions on one plate or to use partial plates, and to handle a wide range of hybrid and surface screening technologies. A FlexTray system has aided loading of larger plates, while the ThermoFlexX vacuum slider system allows partial plates and smaller jobs to be quickly mounted and imaged.
ThermoFlexX software MultiPlate, which enables fast job set-up and remakes, is included in the system package. This has been interfaced with Reproflex3’s existing Kodak workflow, a task made simple by the completely open architecture of ThermoFlexX imagers. Reproflex3 receives files from printers throughout the UK as well as mainland Europe and once processed through the Kodak workflow jobs are sent as 1-bit TIFF files to the imager.
‘We’ve been winning an increasing amount of pre-press and plate business from printers operating wider flexo webs than we have in previous years,’ commented Reproflex3 joint managing director Andrew Hewitson. ‘It was reaching the point where we needed to invest in a larger digital flexo plate imager and one that also provided significantly faster throughput. The ThermoFlexX 80-D meets these criteria plus a great deal more.
‘Within days of its implementation we were able to deliver plates much more quickly to our customers and speed is critical in today’s market.’
The ThermoFlexX 80-D can handle flexo plates from any manufacturer, although the implementation at Reproflex3 coincides with an increase in its use of nyloflex photopolymer plates from Flint Group, which is now the parent company of ThermoFlexX following its acquisition of Xeikon.
‘We work closely with printers, convertors and brand owners, from initial discussions about design to the final printed product,’ added Hewitson. ‘At our main plant in Newcastle we service the flexible packaging, corrugated and label sectors.
‘We’re increasingly seeing a trend for flexible packaging to be printed using flexo presses, rather than gravure, and this is bringing significant new work to our door as we specialize in serving the premium end of the packaging sector.
‘We’ve been extremely impressed by the quality of output from the ThermoFlexX 80-D and so have our customers. The imager will play a vital part in our future growth. We have plans to extend the current two shifts to three, which will allow us to provide around the clock platemaking services, which is just one of the areas we are looking to invest in.’
Stay up to date
Subscribe to the free Label News newsletter and receive the latest content every week. We'll never share your email address.