Reinventing your business
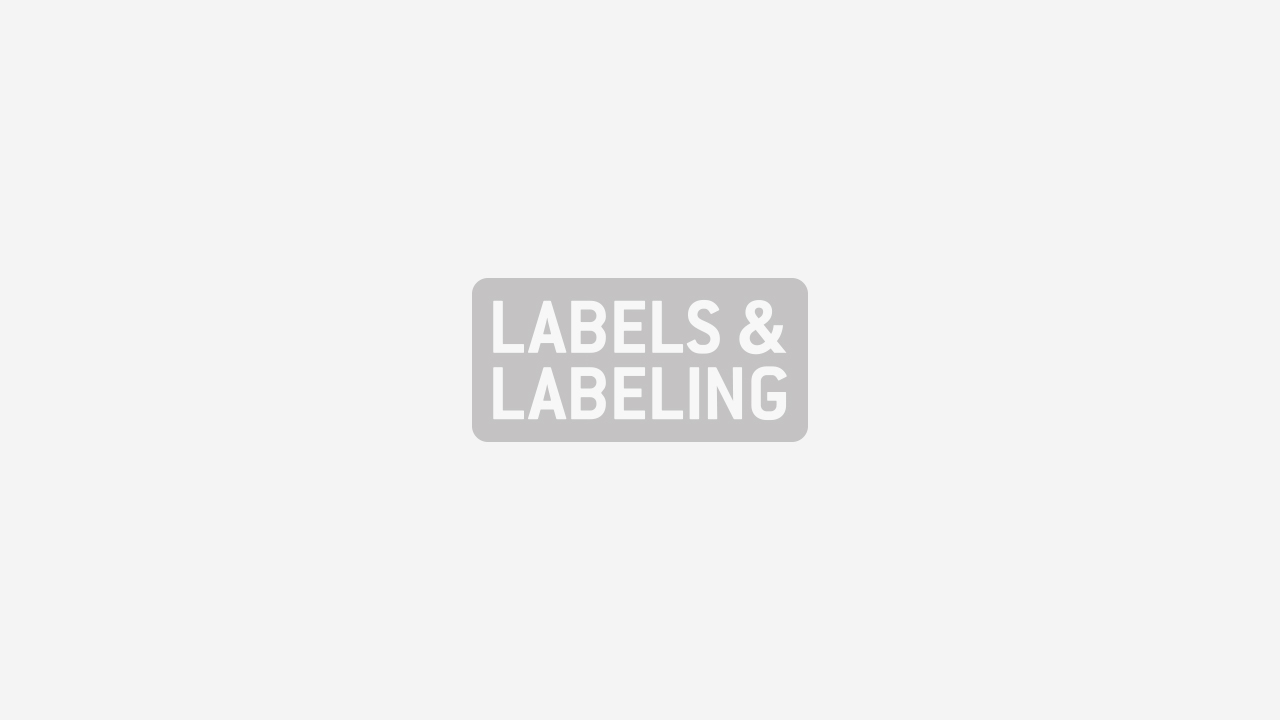
Integration of new hardware and software tools will allow converters to transform their business in line with changing end user requirements. Andy Thomas reports
New hardware and software tools allow converters to reinvent their business to meet the challenges of a new era in which service, not artisan prowess, will be king.
In this new paradigm, integration into the end user’s business will be critical:
• Understanding the marketing objectives behind a new product launch
• Advising on new decoration and consumer involvement strategies
• Reducing the cycle time from approval to print
The converter needs to push hard its value across the whole supply chain:
• Technical expertise
• Cloud-based design & approval
• 3-D preview & prototyping
• Error-proofing workflow
• Efficiency by automation
• Closed-loop color management
Researching the machinery and environment where the product will be labeled, and how the product will be stored, distributed and used will define a range of technical factors such as release value, choice of adhesive and requirements for protective varnishing. These are all areas where the converter, in partnership with their suppliers, can bring unique expertise to bear.
More converters are now undertaking management of the digital master file using software tools which allow multiple stakeholders to collaborate on the design and approval of a label, or a rapid amendment of an existing design.
This service offering can extend to virtual prototyping, where 3D renditions of proposed designs or design changes can be viewed in the context of a shelf display before any commitment is made to physical prototyping.
Once the master PDF has been approved, it drives the converter’s internal workflow via JMF (job messaging format) and JDF (job definition format) protocols.
All the information required to complete the job is contained in the PDF and its associated metadata, which shifts responsibility for the “digital job bag” firmly to the front office. The key idea is there will be no more double keying data for the job, so no chance of introducing errors.
Let’s break this down further. The PDF and its metadata contain information about ink densities and pantone references which can be communicated directly to the ink department. One example is the Cerm MIS that can now download color information from an Esko file directly to GSE’s Colorsat ink mixing system.
Because the file contains step and repeat information, the die database can be searched automatically to see if a matching cutter is in stock or has to be ordered. A next step would be intelligent matching of dies held to the actual job, offering options to the client to slightly resize the label to save the expense of ordering a new cutter.
For press planning the PDF defines the print area, and step & repeat pattern for the job, which can in turn be used to select the optimum press width. Metadata defining finishing/combination print requirements in turn specifies the way the press will be set up – for example positioning of screen, foiling and varnish stations.
Data on run length, finishing complexity and versioning can also be used to generate optimum routes through the print shop – for example digital or conventional press or in/off-line finishing. Gallus demonstrated just such a system at Labelexpo Americas.
There are many ways of automating job planning using PDF data. Jobs can be ganged together on the basis of the material being used or even by color gamut. This was demonstrated at a recent Codimag Open Day using Esko’s Equinox software to allocate appropriate combinations of a CMYLOGV ink set.
The PDF metadata will also define for the press inspection camera which areas of image and text need special monitoring. And now we can go further and define a specific (end user supplied) deltaE value for the new generation of in-line spectrophotometers.
This closes the loop between master PDF and inspection system. Designers can access accurate color data from the cloud-based PantoneLive server. Samples of Coca-Cola red, for example, are printed on a variety of substrates, measured in the l/a/b format, then made available to the designer.
At Drupa, BST demonstrated its new in-line spectrophotometric cameras – developed jointly with X-Rite - using this PantoneLive color data as a reference to measure deltaE on a running web, at the same time as making traditional measurements of density and register. No more trying to ‘chase’ a proof by adjusting color on press or going back endlessly to pre-press.
There is one final step, which has not yet been implemented, but has been called for by converters like CIPPI-award winning 5/7 Etiquettes MD, Patrick Wack. This last automation step is an open press control interface that allows downloading of a range of make ready factors, including material type (for tension control setting), print order, camera settings and run length. Currently these settings are handled internally by the press control system and have to be double keyed by the press operator.
It is only in the last year that all these technology elements have dropped into place, allowing a label converter of any size to set up a truly industrialized, quality assured process which banishes the waste and frustrations of artisan production and delivers to the end user correct color, first time, on any substrate.
This article first appeared in the Labels & Labeling Yearbook 2013
Stay up to date
Subscribe to the free Label News newsletter and receive the latest content every week. We'll never share your email address.