GEWA invests in Polar system
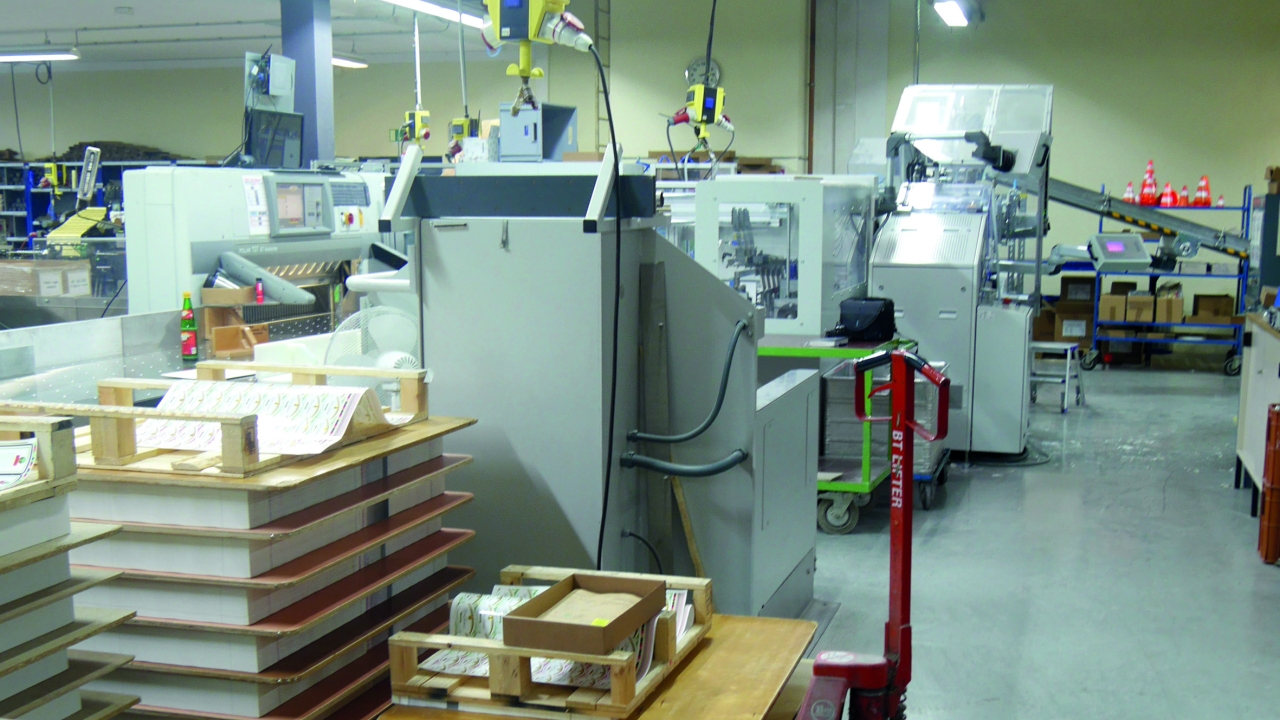
GEWA Etiketten, a leading German converter of both sheet-fed and roll labels, has invested in a Polar LabelSystem DC-11 for the in-line production of banded die-cut labels for customers in the wine, sparkling wine and spirit label markets.
GEWA is a major player in both pressure-sensitive and sheet-fed labels, and had a turnover of around 23 million EUR in 2014. The company has two plants, at Bingen am Rhein and Gau Bickelheim outside Frankfurt, located in the middle of four large wine-growing areas. High quality wine and spirits labels have been the company’s principle business since 1935, later followed by beer, food and publications.
At the Bingen site the substantial machine park for wet-glue applications consists of one-, two-, six- and seven-color machines in various formats with a total of 26 printing units, including a new 6-color Heidelberg Speedmaster with a double coating unit and in-line UV coater. Finishing options include hot-foil embossing, blind embossing and relief embossing, gold bronzing and gold lacquers.
Run lengths vary widely from 5,000 labels a year for some customers to 500,000 a day for others. High levels of efficiency mean GEWA can offer delivery within 48 hours from print approval. Key markets outside Germany include Portugal, France – where the converter has a dedicated sales team – and Algeria.
Automation calculation
A 2015 analysis of the Bingen site operations revealed clear potential for automation on one of its three lines, where a stand-alone label die-cutter was in operation. The key benefits of automation were felt to be lower operator costs, improved health and safety and an end to the risk of mixing up orders. At the same time it was important not to lose flexibility in the event of last minute order changes. The higher output of the in-line production unit would have to compensate for the lower set-up time on the standalone die-cutter.
After extensive testing, GEWA and Polar agreed on a configuration for the DC-11 Label System which would deliver the desired production flexibility. Various intermediate tables and storage areas are incorporated in the plant to allow label production to be interrupted at short notice without the sheets awaiting production having to be removed.
In operation, print sheets for processing are first lined up in the jogger, checked via a counting scale, then transported via an air bed to a Polar 137 Autotrim cutting machine. This had been installed a year before the in-line production system, and Polar’s modular technology structure allowed it to be smoothly integrated into the overall system.
Once the material – which can be up to size 3B – is precut to the desired number of strips with the high-speed cutter, the lengthwise packages are automatically fed on to the Autocut 25 cutting system. This forms the strips into individual packages and guides them to the DC-11 system die-cutter with the help of an ejector device on the front table of the Autocut 25. The punch/die-cutter works fully automatically and is suitable for all common label papers. The final step of the integrated process is the banding of the individual packages with the help of the BD single-head bander.
‘Its ultrasonic welding unit does not require preheating and is therefore always ready for use, is gentle on the material and does not cause any unpleasant odors,’ says GEWA managing director Uwe Refflinghaus.
When the system is running at full capacity, up to 960 packages an hour can be produced. Multiple square-cut and die-cutting programs can be stored, along with the variable banding geometries, which can be changed at short notice.
Job changeover is achieved within 15 minutes using the OptiChange system, which allows exact placement of the material for maximum cutting and die-cutting accuracy, says Uwe Refflinghaus. Another plus for Refflinghaus is the option of switching off die-cutting and forwarding the bundle of labels directly to the banding unit. ‘As a result, we are absolutely flexible when we have to band labels that don’t require die-cutting and our other processing lines are fully utilized.’ Just as importantly, there are significant health and safety benefits.
‘While our employees previously had to lift and move tons of material, in-line production is really relieving this burden.’
Stay up to date
Subscribe to the free Label News newsletter and receive the latest content every week. We'll never share your email address.