Automation Arena debuts at Labelexpo
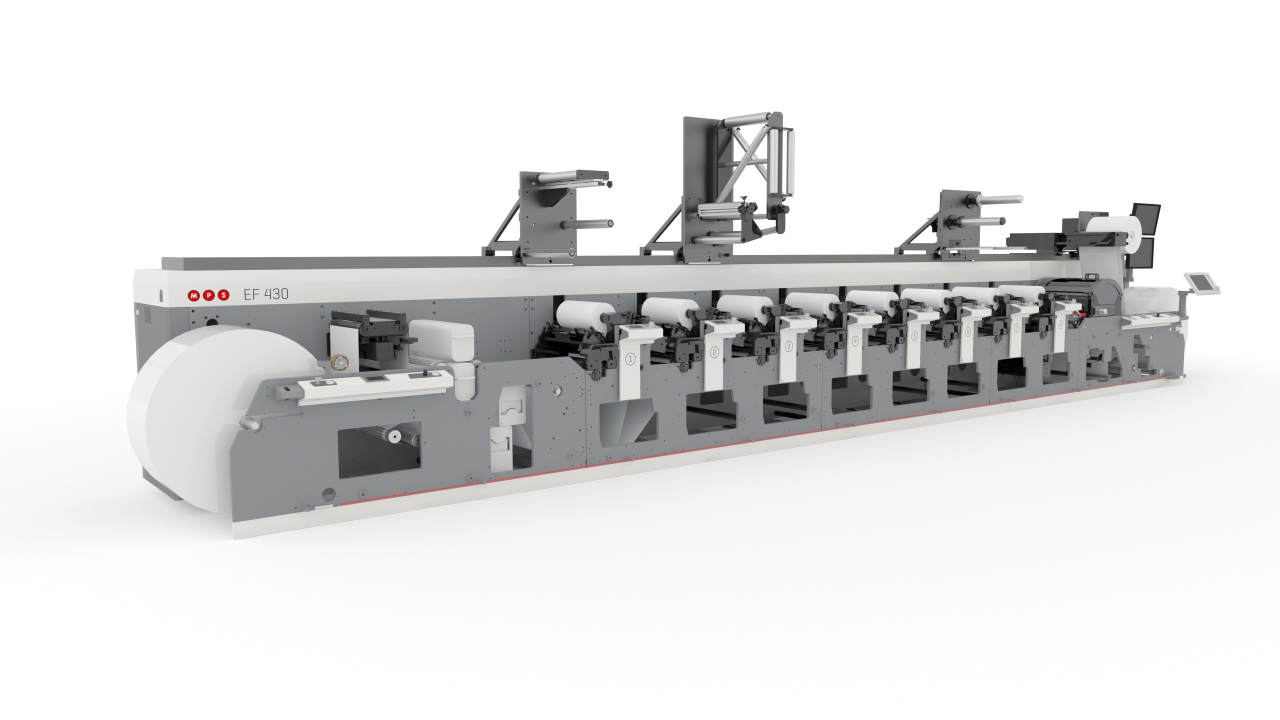
This year, Labelexpo Europe 2017 promises to provide one of the most ambitious of all the special show features organized to date, bringing together some of the main market leaders in management information systems, workflow and pre-press automation, automated digital and analogue press set-up, sophisticated web inspection, and automated finishing, waste extraction and rewinding systems – all coming together in a dedicated ‘Automation Arena’ that will provide show visitors with a state-of-the-art snapshot and preview of the increasingly automated label printing plant of the future. A future in which everything that can be automated will be automated.
Using large viewing screens in the Arena, visitors will be able to see in detail all the different job creation, artwork uploading, and MIS order processing steps taking place in a Cerm system, then on to the working stages of pre-flighting, quality checks, proofing and customer approval using Esko’s Software Platform and Automation Engine, followed by Cerm scheduling, substrate checking, tool ordering, and the sending of JDF files, ready for production on to an MPS EF 430, 8-color press ‒ with no gear cylinder connection, intelligent pressure setting and zero waste roll change, which in turn will be fitted with a Kocher + Beck UR Precision 440U non-stop splicer unwind, AVT Helios inspection and a Rotocontrol RSC 340 WFL slitter and turret rewind with a Wasberger fully automatic core loader and a Matho EM180 Cuttopipe waste removal system.
Several job files (different jobs to the MPS press) will also be sent to a Xeikon X-800 digital front end for batching, step & repeat and the preparation of job identification, die-cut, inspection and turret rewinder barcodes in preparation for running on a Xeikon 3300 with a laser die-cutting unit.
Production
Once the Xeikon press starts its production run the different press operations – printing, inspection, laser die-cutting and rewinding – will again be filmed and shown on the screens, enabling attendees to observe the different identification barcodes in operation, AVT defect detection, laser die-cutting set-up and rewinder automation.
Similarly, when the MPS press starts its production run, the different operations of printing, AVT inspection, die-cutting and defect detection will all be filmed and shown on viewing screens. The printed rolls will arrive at the automated Rotocontrol die-cutting, inspection and turret rewinding unit for job finishing, for which the operator has set-up the new job. This set-up and finishing, including fully automatic Wasberger core loading and the use of roll lifters, will also be viewed on the large screens, together with the process of edge-trim and matrix waste removal using Matho extraction and bagging – which could also be incorporated into a centralized system for complex factories using balers or press containers. Both presses will use AT740 film from Avery Dennison, with inks supplied by Flint Group and Zeller+Gmelin.
The last stages in the job automation process will come back to the Cerm operator and attendees will be then taken through warehouse stock location, job picking, allocation of the shipping carrier, printing of a delivery note and advising the customer accordingly. An invoice will be prepared and sent, with a covering e-mail, to the customer.
Finally, summary data on the day’s production and sales will all be viewed on the Arena screens.
The Automation Arena presentations aim to show what can be achieved with today’s ever-more sophisticated business management and automated production systems, bringing benefits to the converter that include reduced time to market, enhanced quality and performance, less opportunity for errors, fewer production stops, reduced waste, less materials costs, increased operational work safety, and improved margins and profitability.
Stay up to date
Subscribe to the free Label News newsletter and receive the latest content every week. We'll never share your email address.