Belgian converter revamps production
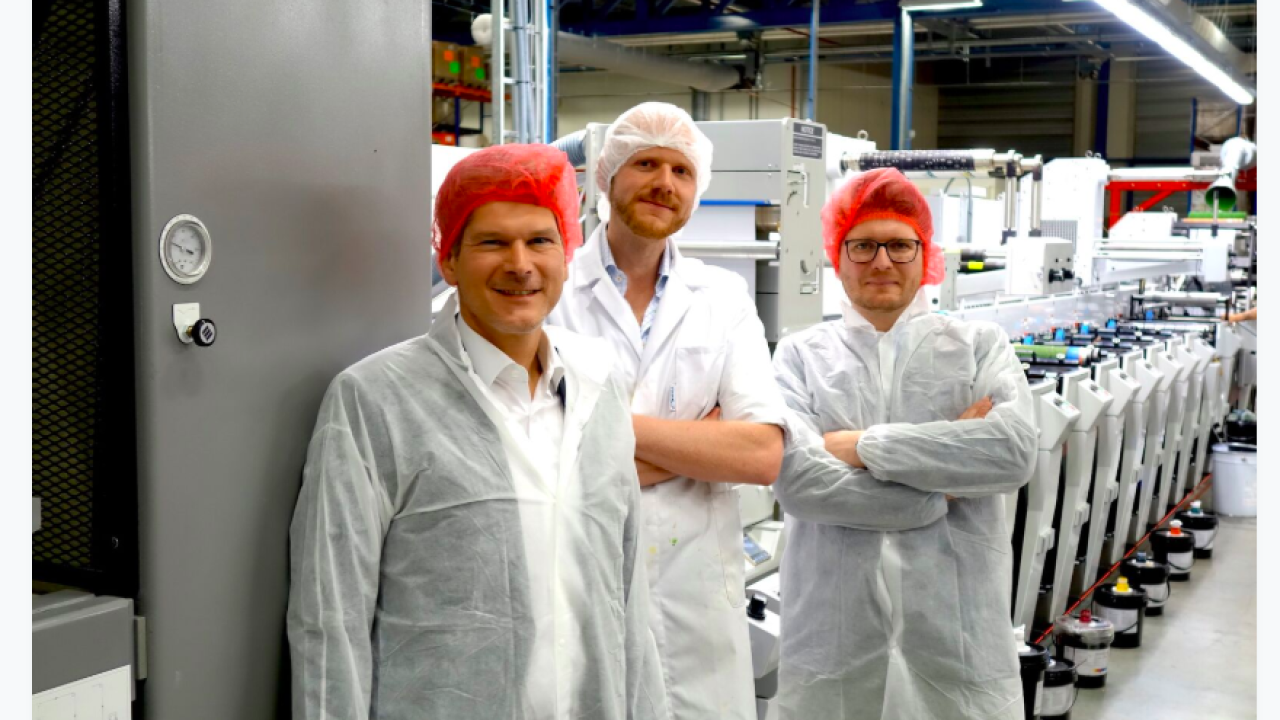
The project began back in 2016 with a major growth in label sales by Desmedt that highlighted a shortfall in production capacity on the company’s existing flexo and digital presses. According to general manager Henri Köhler: ‘We intended to buy one new 8-color UV flexo press and visited all of the major manufacturers to trial their latest machines on our own work – a mixture of self-adhesive and multi-layer labels and some screen work.’
Impressed
Not an existing Mark Andy user, Köhler was most surprised by the demonstration of the Performance Series press in the Warsaw showroom. ‘We had taken a day’s work with us and had run it off by lunchtime with our own operator, who had never used a Mark Andy before.’
Desmedt placed particular emphasis on job changeover and make ready times, and were invited to visit other Mark Andy users, KDS in Poland and LariTryck in Sweden, to see similar presses in commercial operation. ‘I was also very impressed with the Mark Andy company structure in the USA. It was obvious from their four-week lead time and the shipping of one press every two days that being a specialist in flexo technology has major benefits,’ he adds.
So impressed was Desmedt by the Mark Andy press demonstrations that the company switched its entire strategy from a single press to a complete conversion of its print capacity. The result was an order for three of the second generation P7 Performance Series servo presses, two of which are 10-color and one is 12-color. All have a 430mm (17in) web width, as well as being fitted with UV LED curing. Installation began in January 2017 with the first 10-color followed in April by an identical machine. These replaced existing 8- and 9-color flexo presses. The 12-color P7 was installed in September.
‘More colors make for greater efficiency and higher quality on existing work, and we are already seeing how cold foil and the added productivity of UV LED is generating new work in the value-added markets,’ says Köhler. Desmedt is in fact Mark Andy’s largest UV LED narrow web installation to date, and its curing capability is allowing the company to run screen white at 110m/min, even with inexperienced operators. ‘We know we can go faster, but we’re keen to grow into the possibilities that it offers us with our existing cosmetics customers,’ he adds.
Speaking for Mark Andy, European sales manager Timo Donati comments: ‘It was important for Desmedt to have a complete package of high-end performance equipment from a manufacturer that has the knowledge to realize the switch from UV to UV LED. Added to that, the company needed an organization that could support the installation with quality after sales service, and with our new European sales and service structure, Mark Andy was in the best position to supply.’
The majority of Desmedt’s output at present is for the food market, but Köhler is keen to expand into automotive and household products, and other markets where legislation is demanding multi-layer labels. ‘The two 10-color Mark Andy presses replaced three existing flexo presses and a digital line. We are using the 12-color for business development purposes,’ he explains.
Productivity
But whether on existing business or new projects, Köhler is very positive about the beneficial effects that Martin Automatic non-stop roll changing technology has on Desmedt’s business. ‘We already had an MBSF unwind/splicer on each of our former flexo presses, and they made a huge difference to productivity, especially with the high number of job changes we need to accommodate with shrinking run lengths,’ he says.
‘These machines allowed us to maximize productivity with small and part-used rolls by incorporating them into our non-stop production. While one spindle unwinds a roll, the operator can load a partial roll on the other spindle, then automatically splice into that roll without stopping the press. This has had a significant cost effect on substrate waste and effectively doubled the output on the presses.’
Also, at the conclusion of a press run, the operator can transfer out of the final roll of that job and into the first roll of the next job, without wasting any time. This increases the uptime of the press even if run lengths are short, or less than one roll.
To add to the existing Martin Automatic machines, Desmedt ordered two new MBSF auto splicers and an LRD automatic transfer rewinder to work with the new Mark Andy presses. The new machines, which were delivered straight from the Martin Automatic stand at Labelexpo Europe in Brussels, feature the latest models of MBSF unwind/splicers. The ‘F’ denotes mono film capability, and one of the new splicers is designed to operate at 300m/min on unsupported film to match the press speed. It has a servo motor to accelerate the roll when splicing, which reduces the festoon capacity. All of Desmedt’s MBSF machines feature reverse-side-tape laser assistance, which helps align the tape with the web edge and eliminates any hand/eye coordination errors. This feature is especially helpful with the narrow matrix waste edges that Desmedt runs.
The new Martin LRD rewinder is a high-spec unit fitted with in-line slitting for edge trim and center slitting. It can handle large rolls up to 800mm in diameter, and those up to 410mm can be automatically ejected to a receiver on the operator side, without the standard ramp exit. Usefully, the LRD is fitted with Martin’s ‘Mobility Kit’, which aligns the unit on locating pins sunk into the production floor, and allows Desmedt to wheel it to whichever of the Mark Andy presses has a job that benefits from automatic rewind capability.
‘We estimate that the Martin units save us five minutes per job change. Based on our double-day shift work pattern, five days per week, this equates to a saving of 400 hours per machine in a year – or better still, 1,200 more hours of production across the three new presses – that’s big money.’ says Köhler, who also points out that continuous running has ‘invisible’ benefits, as it removes many of the old operator working practices that were disruptive to production and costly to productivity.
Stay up to date
Subscribe to the free Label News newsletter and receive the latest content every week. We'll never share your email address.