Converting from digital to conventional
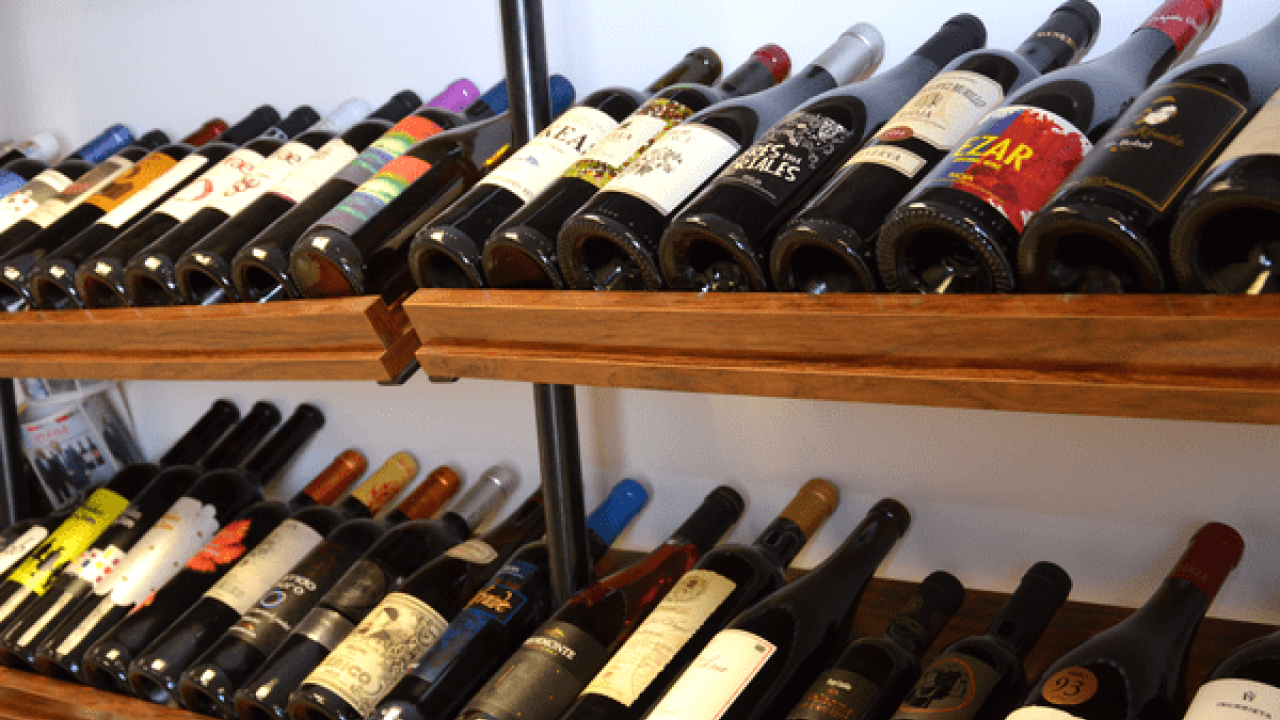
This year has seen Finat report, for the first time, digital installations surpass conventional press sales in Europe, while a number of installation stories published from around the world have emphasized the ongoing conversion of printers using conventional technology to digital printing, largely driven by short runs. However, it is also true to say that there is a growing move of high quality short run work to semi-rotary offset over digital because of the complexity of finishing combined with super-high print quality standards.
In the case of Etilisa, the decision to install a Miyakoshi MLP13C semi-rotary offset press was made as it seeks to expand its client base and offer new products to existing clients. Its main market, wine labels, demands a very high printing quality in medium length production runs, with offset technology identified as allowing it to respond to these demands.
Etilisa CEO Diego Castilla comments: ‘Wine producers in this area have sampled our products, they know us and tell us that they like our quality and our service, and they want more. Why can’t we obtain these larger orders? From our stance of “try us, share us”, which is what we can offer with digital technology, we want to go on to “order everything from us”, no matter the quantity. Our digital press is productive, it’s fast, and it gives us quality, service and quick response, all valued by our clients, but it has its limits. In this context, we must head towards a much more complete and balanced print shop.’
He adds: ‘We will expand in our market, the wine industry, seeking larger orders and moving into other wine areas such as Rueda, Ribera del Duero, Toro or Cigales. Unlike La Rioja, where wine producers produce many different wines, wine producers in these other areas often produce only one wine, and this is especially true in Rueda, so where a producer in La Rioja might order 25,000 labels, in Rueda the order might be for 300,000. With the new semi-rotary offset printer, we are now ready for Rueda.’
Castilla notes that Etilisa’s expertise in digital printing, and learning the technology and market from its foundation in 2010, has allowed it to effectively handle the transition to offering a comprehensive production toolset.
But what is the reality for others thinking about the transition? Enrique Rodriguez, Miyakoshi Europe sales manager, says: ‘In our experience, it depends above all on the attitude and background. These are fundamental. The common case is that someone familiar with conventional printing is moving into the digital realm, and if they are willing to learn, they can start producing quite quickly. But they have to understand that digital technology is not at all similar to conventional technology. Now we have the opposite situation, going from digital to conventional. We have had some experience of this, but Etilisa’s is undoubtedly the most radical case we have seen. It is starting on a different basis. But the process must be the same: willingness to learn, and attitude. I don’t think that handling an offset machine, with all it implies, is really more complicated than handling a digital machine. In the end, the question is not the machine, it’s the process. They are two different routes to manufacturing a label, and each has factors that must be taken into account. Etilisa has everything needed to implement and develop offset technology efficiently. It has a combination of knowledge and ability, and that counts for a lot. And then there is their attitude. Knowledge sums with ability. But attitude does not sum, it multiplies.’
Rodriguez adds: ‘They are complementary technologies, one does not exclude the other. They may intersect at some points, but they are completely complementary. And in label printing, more than in other sectors of graphics arts, it is obvious that the tendency is to coordinate different technologies within the same company in order to be able to respond at any time to the clients’ demands, which can be very varied.’
The Miyakoshi MLP13C installed by Etilisa features five offset printing units and a flexo print unit to enhance the quality of metallic finishes. Rodriguez goes on to note the difference between the two conventional processes.
‘Comparing the semi-rotary printing system with flexographic printing, we can change the format almost as though it was a digital printer. In fact, you don’t have to touch the machine, it is all automatic, and that helps a lot. We have been seeing this recently since we work with large organizations that are starting to adopt this technology, not only for the print quality, but also because the format changes are a lot cheaper than in flexographic printing. Semi-rotary printers have always been around, but were only useful for very exclusive labels, while our machine provides this quality for far greater production runs, printing on materials of all kinds.’
Stay up to date
Subscribe to the free Label News newsletter and receive the latest content every week. We'll never share your email address.