Geostick leads the way in automation
Dutch label and packaging converter Geostick is a cutting-edge company at the forefront of automation technology, sustainability and technical innovation that enhances its overall efficiency.
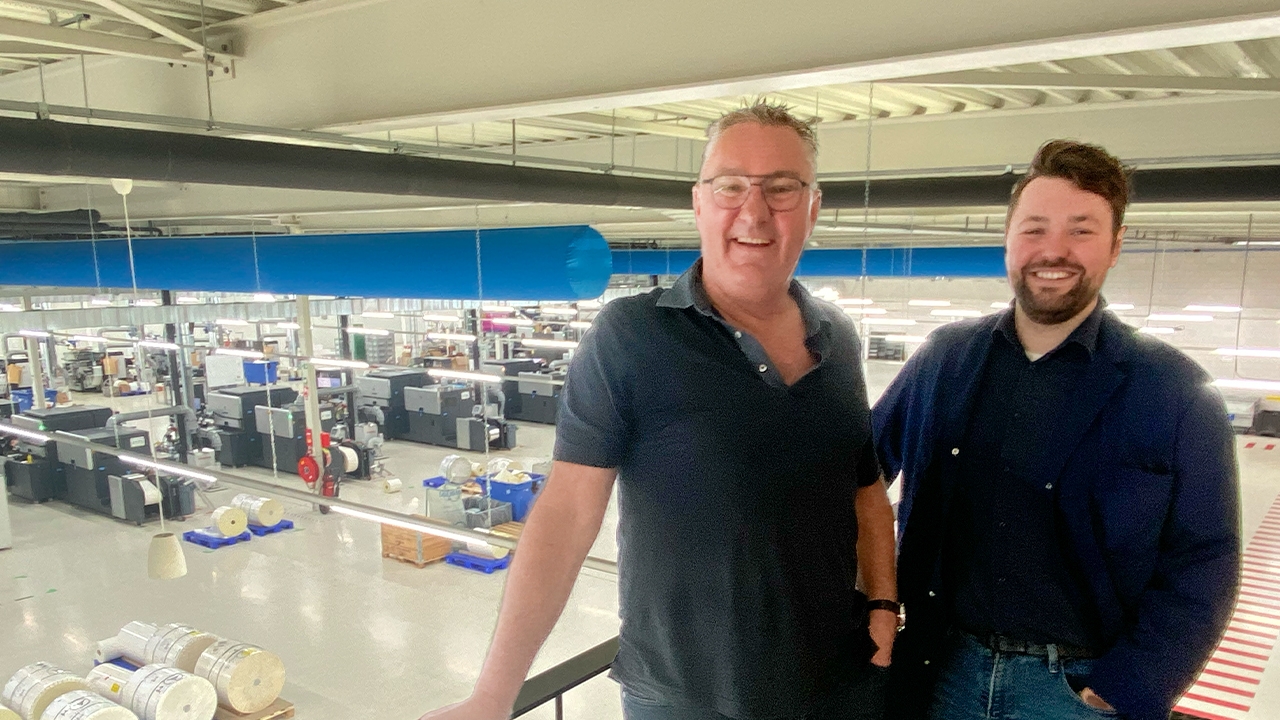
Cees and Tom Schouten in Geostick’s new digital production facility
The Netherlands’ leading label producer and supplier is pushing boundaries by streamlining its processes and carrying a strong dedication to enhancing its overall efficiency.
The kind of blue‐sky thinking at Geostick that has grabbed the attention of the world label industry.
Geostick has been on a rapid growth trajectory since 2014, though the private, family‐owned label converter can trace its roots back to 1924. The company has grown both by acquisitions – with Clever Etiketten, Labelform and Etiket BV – and more recently with the build of a new digital printing operation in Uithoorn, Netherlands, near Amsterdam, where its first production facility sits across the street. Geostick has a third operation site in Heumen, Netherlands.
Rising star
It’s not often a label converter gets a blank slate on its production floor. But it’s particularly interesting when a personality like Tom Schouten is the company’s operations manager. Schouten, with a degree in international business, joined Geostick in 2019, firstly at the behest of his father, Cees Schouten, operational director at Geostick, to assist with a few one‐off projects. Tom quickly saw the possibilities of working in the labels and packaging space and joined Geostick full‐time to help oversee the successful integration of the new digital printing facility that’s buoyed by HP Indigo, Bobst and AB Graphic technologies.
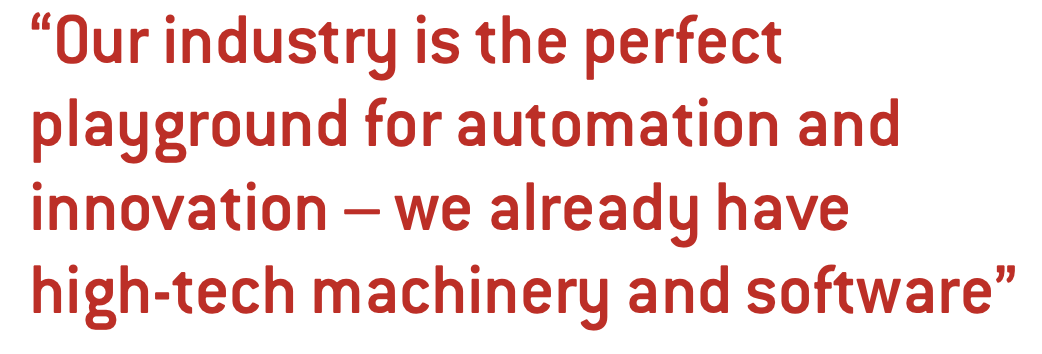
At Geostick, Tom has been given the freedom to explore new opportunities for finding process efficiencies, a passion that earned him a nomination for, and eventual win, as the 2023 Global Label Awards Rising Star. The award recognizes emerging talent in the label and packaging industry representing the next generation of leaders. Schouten was honored at Labelexpo Europe 2023.
Tom Schouten truly is a rising star in the European label industry. The 30‐year‐old only has four years in the industry, and already his impact is being felt, as the Global Label Award judging panel noted.
‘He’s managed to bring optimization to Geostick operations and supported the company’s growth by creating a workflow change management and successful integration of digital technologies,’ the Global Label Award judges said.
Tom is also actively engaged in Finat, and passionate about cultivating other young leaders in the label and packaging space, mostly by touting the industry’s boundless opportunities for technical innovation.
‘Our industry is the perfect playground for automation and innovation,’ Tom says. ‘We already have high‐tech machinery and software.’
‘In the upcoming years, I think we will see an even larger challenge to attract young talent,’ he continues. ‘Especially young talent behind our printing presses, so we need automation and digitalization of manual processes to attract them and get more out of that same operator. The supplier that realizes that will be the winner and I think they are all already heavily investing in this.’
Automation
An early project for Tom in his career at Geostick was to shape the design for the new digital printing facility. Ahead of opening the facility in 2020, Geostick purchased four HP Indigo 6K presses, the first units to be installed worldwide. Geostick paired its printing assets with finishing equipment from AB Graphic.
‘We were able to buy a lot of equipment in the middle of the pandemic, which made our suppliers very happy,’ Cees says, laughing.
In total, Geostick has 10 HP Indigo presses, including an HP 20000 for labels, shrink and flexible packaging applications, and a new HP Indigo 200K installed in October. The HP technology is complemented by a Bobst Digital Master 340 inkjet machine. The digital facility processes 100 to 200 jobs per day, and the company does about 21M USD of business each year on its digital assets. Geostick relies on AI tools from Cerm to plan the most efficient production route for the high volume of job tickets, and Hybrid Software to automate its prepress processes.
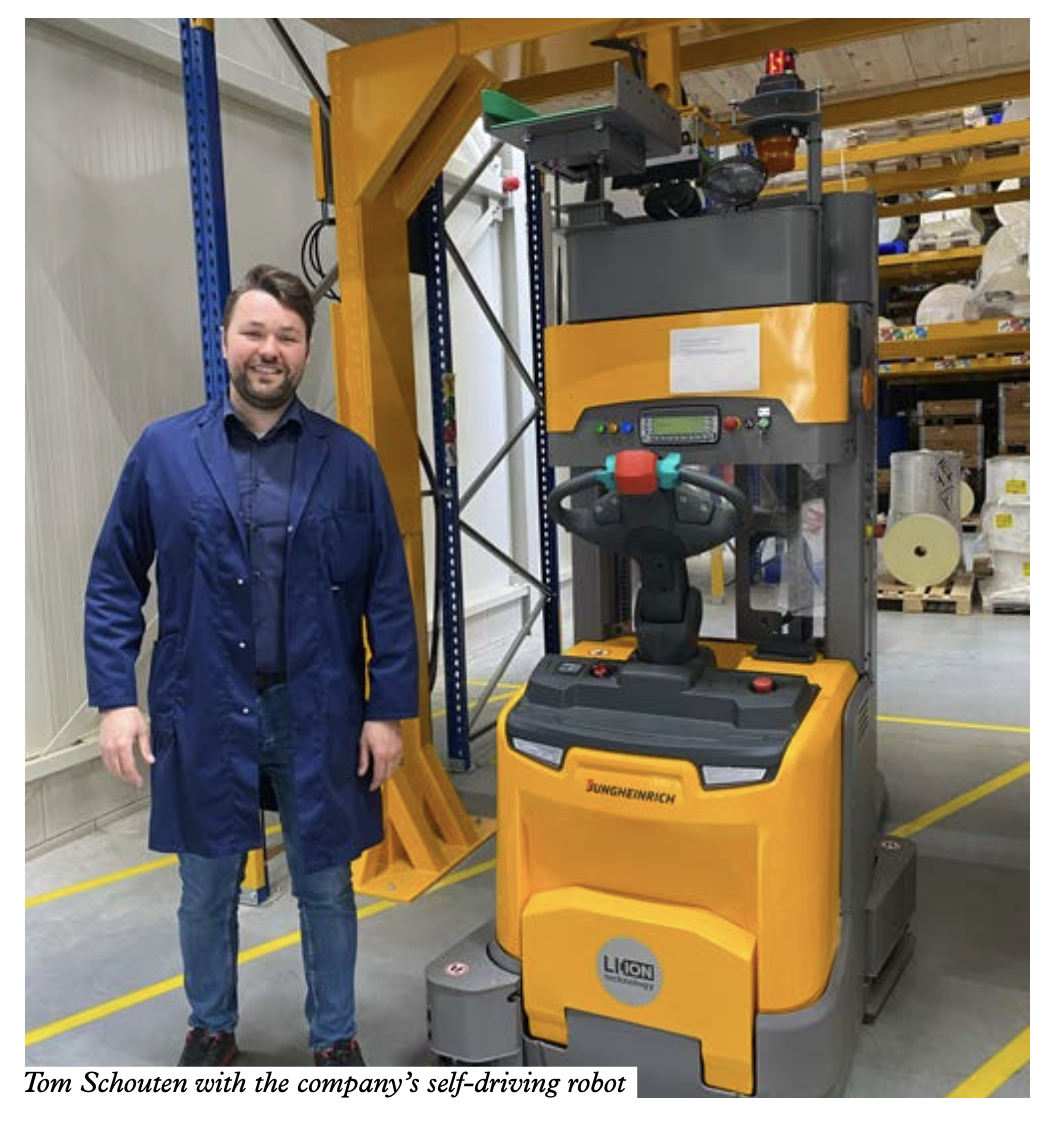
Automation is equally as important on the conventional and digital sides of the business. For flexographic production, Geostick relies on technology from Nilpeter and MPS for turning over 39M USD annually at its two conventional production facilities.
In total, the company has 14 printing lines, all running on a ‘single pass’ philosophy, meaning there is one operator per line that ‘operates everything into a box,’ Cees says. ‘There are no second passes.’
This is implemented with the help of workflow and automation technology from Cerm and Hybrid Software and automated color matching from GMG.
Robots
As the company prepared to install its new digital technology, Tom started thinking about the way the building and its assets were laid out. He was looking for ways to get jobs off the finishing equipment and to the warehouse while minimizing the time operators spent away from their production equipment. The company ended up choosing an automated guided vehicle (AGV) from Jungheinrich to move finished product around the production floor.
Tom says: ‘We were looking for something flexible and scalable, and the AGV was the perfect solution. It picks up the pallet of finished product from the machine and brings it to the warehouse. There it puts down the pallet, picks up an empty pallet, and brings it back to the machines. This way the production process continues.’
The self‐driving robot uses cameras to look for floor markings to avoid hitting people, presses and anything else that might be in the way. The robot has smart charging, meaning it charges as soon as there is a break in the workday, on the weekends, or at slow points when the production team is less likely to need it.
Next on Geostick’s robotics wish list, is a machine that can bring raw materials to the press. Tom says this is challenging given the number of raw material SKUs on a single pallet.
‘We need to make the operational structure to allow that first,’ he says.
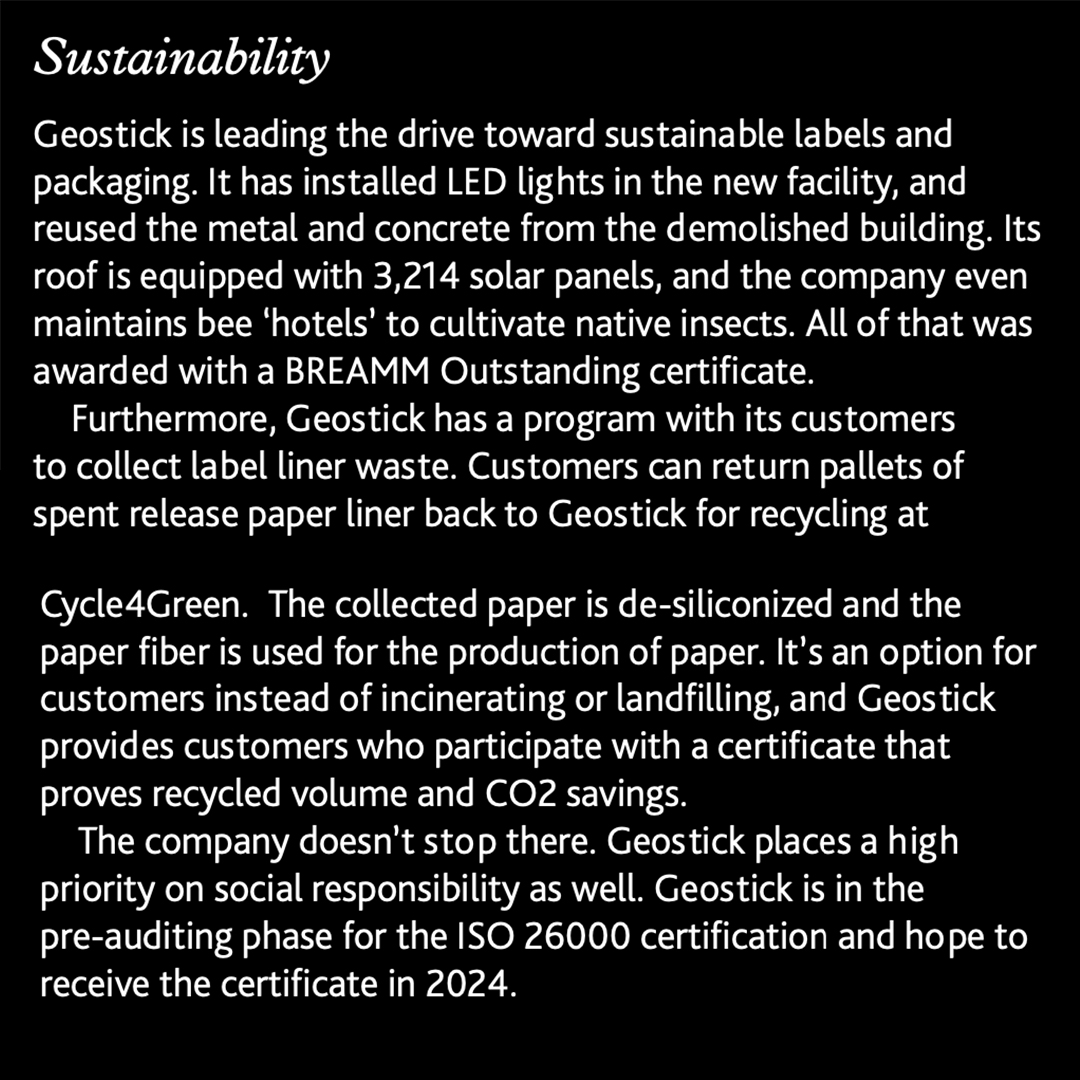
Robots are still a novelty in many label manufacturing plants, but leaders at Geostick noticed the benefits immediately. There are the tangible benefits of fewer touchpoints and fewer actions taken by the production team.
‘If an operator walks from a finishing line to the warehouse with the finished rolls, he may make a stop to go to the toilet, to talk with friends, to take a phone call. That’s all time that he’s not behind the press,’ Tom explains. ‘The amount of time the operator is walking, that’s the amount of time the press isn’t running. There’s a huge cost associated with that.’
‘We planned this facility to make it the most efficient for an operator to do their job,’ he adds.
There’s also the intangible effect the robot – affectionately called Rob Ot around Geostick – has had on employees.
‘When our employees first saw the AGV, they looked around a lot and wondered what it was doing and if it was doing it well,’ Tom says. ‘Now it’s just another colleague working with them to get the finished product off the floor as quickly as possible.’
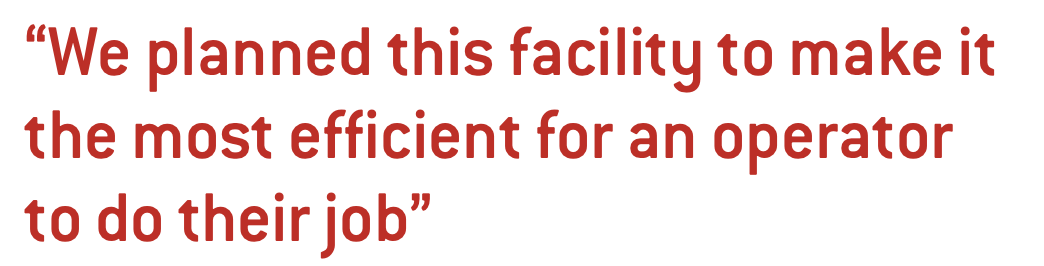
Cees adds: ‘The printing industry is still a little conventional. Although we use modern technology, the way we operate is still somewhat conventional. Implementing the robot into the production area was something our staff was very proud of. Proud to work at this kind of company.’
Future
As the company looks to celebrate its centenary next year, Geostick has ambitions for more growth, with automation leading the way.
Contrary to many schools of thought, Geostick’s approach to automation is not driven by a labor shortage.
‘For me, automation is a way to make the process more efficient and for our staff to enjoy working here, and for them to be the most productive when they are working. So anything we can automate with that in mind, we will,’ Cees says.
The company is on the path to what Cees hopes is one day, ‘a boring life.’
He says, with a smile and a laugh ‘The best situation is to have a boring life. When life is boring, then you don’t face challenges, which also means the process is fully under control.’
Stay up to date
Subscribe to the free Label News newsletter and receive the latest content every week. We'll never share your email address.