Kuresa makes move to digital technology with Durst
The leading Peruvian converter has installed its first digital press – its first investment outside of letterpress technology in more than 20 years.
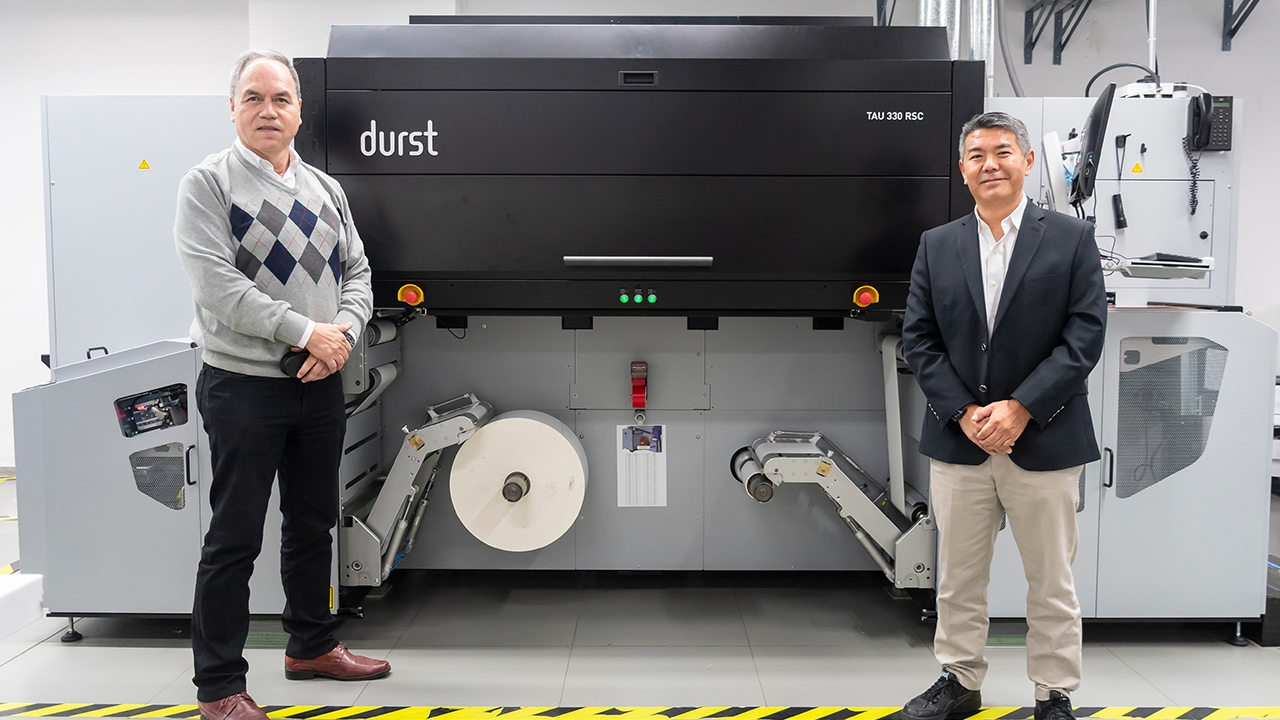
L-R: Fernando Montedoro, sales manager, and JaimeYoshiyama, CEO, with the new Durst Tau RSC inkjet press – the first in Peru
Kuresa, Peru’s leading label converter, has installed a Durst Tau 330 RSC inkjet press – not only its first piece of digital printing equipment but the first non‐letterpress machine it has added to its arsenal in more than two decades.
The Tau RSC inkjet press – the first of its kind installed by Durst in Peru – has a 330mm web width and can print seven colors (CMYK plus white, orange and violet) at 1,200 DPI. It runs at 80m/ min, with that speed reduced to 52m/min when printing white.
Kuresa CEO Jaime Yoshiyama is enthused by the possibilities brought by the company’s first foray into digital printing. ‘The investment in the Durst Tau RSC inkjet press will add a new dimension to our offering,’ he says. ‘It can print both short and long runs at high speed and with excellent quality. It will increase the options we can provide to our clients, as well as allow us to target new end‐user markets and produce new products such as shrink sleeves, among others.’
For Durst, the installation further vindicates recent efforts to increase its presence in countries outside of Latin America’s two largest markets – Brazil and Mexico – and reflects rising interest from the region’s label converters in a new generation of inkjet technology which increasingly can compete with flexography in terms of speed and productivity.
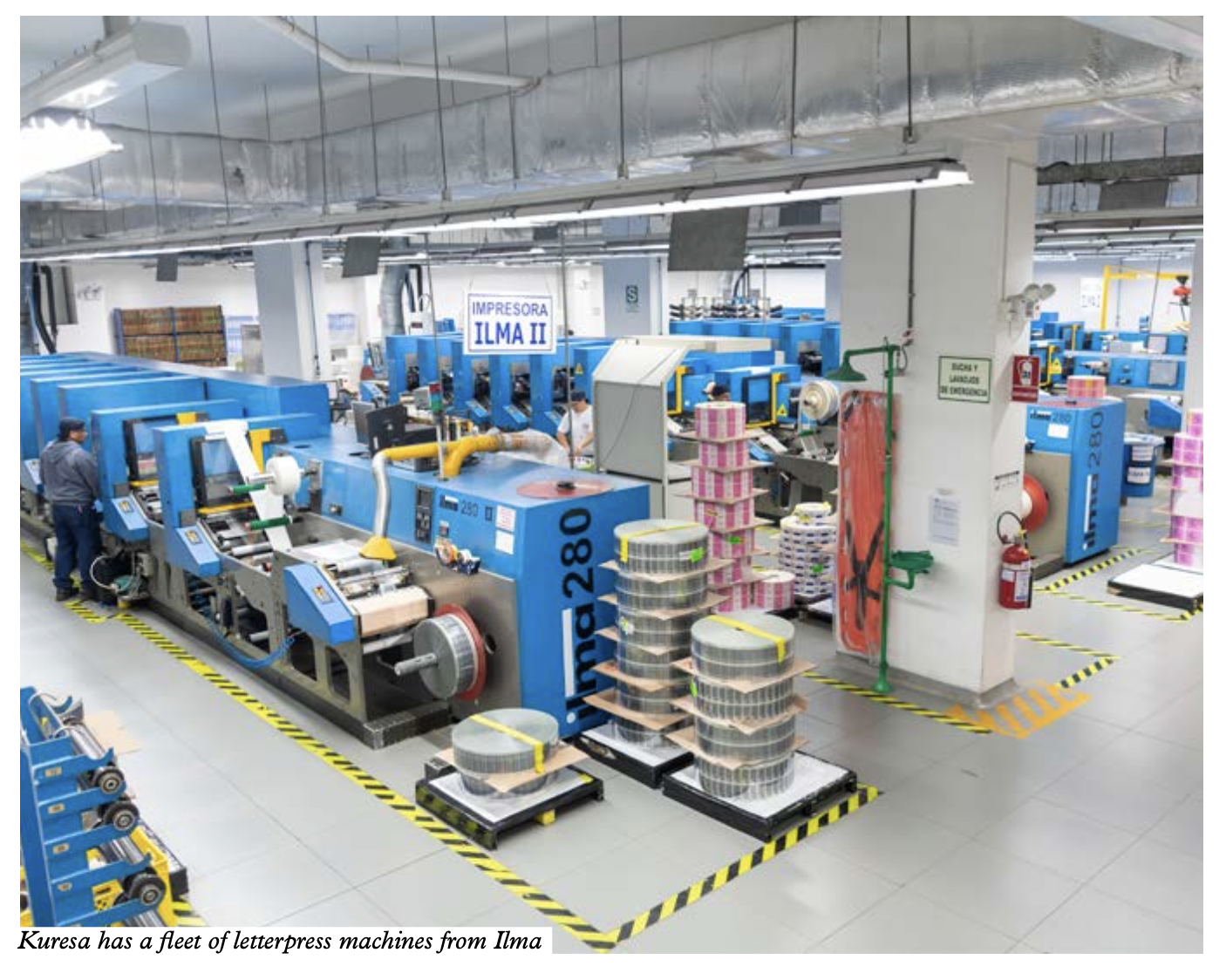
‘There’s no question that Kuresa is a hugely important reference point in the industry, and was one of the first companies we contacted when we began this process,’ says Alejandro Ortiz, who covers the Latin American region for Durst outside of Brazil and Mexico. ‘We are very proud to have them as a client and are sure that we will have a valuable relationship into the future. The Tau RSC inkjet press gives Kuresa great versatility to optimally meet all the needs of its clients in terms of job sizes, variability of information and time to market.’
History
Kuresa was founded in the Peruvian capital of Lima in 1965 as a producer of adhesive tapes, which continues to represent 64 percent of its business. Since the mid‐1980s, it has been the exclusive distributor in Peru and Colombia for Pilot, the Japanese brand of writing instruments, which accounts for a further 21 percent.
The remaining 15 percent of revenue comes from self‐adhesive labels, which the company began printing in 1998 with the installation of a flexo press from Italian manufacturer Ecoflex. Letterpress quickly became Kuresa’s core label printing technology, however, with the installations of presses from Swiss manufacturer Ilma in 2000 and 2002.
Ilma, founded by former employees of Gallus, stopped manufacturing the presses after around 50 installations though parts continue to be available on the market.
Kuresa bought further Ilma machines over the coming years. Each of the presses has flexo, silkscreen, reverse printing and hot and cold stamping capabilities, and can print variable data for promotional applications. They are equipped with inspection systems from BST, web cleaning equipment from Teknek and Kelva, corona treatment and lamination. Proofing and mounting equipment come from Heaford while finishing is handled by Rotoflex machines.
The company became synonymous with high‐quality letterpress printing, winning Finat’s Best Rotary Letterpress Printing Award for four consecutive years between 2007 and 2010, and establishing itself as one of the leading label producers in Latin America.
Kuresa invested 25 million USD in a new 23,000sqm facility inaugurated in 2011, which featured the addition of a new adhesive coating machine from German manufacturer Olbrich – the company’s largest ever single investment at 9.5 million USD. This benefitted both the adhesive tape and label printing operations, with the company now able to produce its own labelstock. Among the guests at the ribbon‐cutting ceremony were Salomón Lerner Ghitis, Prime Minister of Peru at the time, and various members of his government.
Today, Kuresa is one of the few large‐scale producers of adhesive tapes in South America. Its scope includes adhesive design and formulation, coating both waterborne and solvent‐based adhesives, converting them into finished rolls, and packing them. Production, which takes place on world‐class machinery from Switzerland, Germany and Italy, is at 65 percent of capacity.
‘There is plenty of room to grow with our existing infrastructure,’ says Yoshiyama. The company produces general‐purpose and specialty masking tapes, acetate‐based tapes, double‐sided tapes, and heavy‐duty EPVC packaging tapes, among others.
In the label division, meanwhile, running two shifts six days a week, the company produces four million square meters of self‐adhesive labels per year.
Ninety percent of production serves the local market, with the remainder exported to Colombia, Ecuador and Central America. Forty percent of the company’s production is for the cosmetics and personal care market; 34 percent goes to food and beverage; 18 percent to household goods; 6 percent is for pharmaceutical applications, with the remainder divided between the agricultural market and promotional work.
Digital move
While digital was being enthusiastically adopted by converters elsewhere in the region – around the time of Kuresa’s factory move, Latin America was HP Indigo’s fastest‐growing market – Kuresa remained loyal to its high‐quality hybrid letterpress printing, preferring to keep an eye on the technology as it evolved.
‘We were looking at investing in digital technology for a long time,’ says Kuresa’s CEO, Jaime Yoshiyama. ‘We spent some four years studying the various options on the market and getting to know the manufacturers at industry trade shows. We had felt that the productivity levels were not quite good enough for what we needed. But recently there has been a great evolution in the market in terms of the productivity of digital presses, and the quality of the printing has also improved.
‘During the pandemic, we found that some of the work we were doing was not very efficient on our machines. There were more SKUs and the runs were getting too short. This also spurred us into adopting digital.’
After evaluating many options, Kuresa opted for the Durst Tau RSC. What made the company choose the press over others available on the market? ‘Printing at high speeds, without waste, with lower set‐up time and great flexibility in materials – these have been the key factors,’ explains Yoshiyama. ‘The physical structure of the machine, too – its robustness and stability – is another advantage. It produces perfect registration.
‘The print quality is excellent and the colors it produces are very vibrant. We did a lot of internal testing of our clients’ jobs, and everything passed their quality needs. It’s a highly productive machine and very quick to set up a new job.
‘The press has given us an important amount of extra capacity. It allows us to offer existing clients new options and ideas, such as personalization and promotional campaigns. They know we can produce shorter runs for them if needed, and that their work will be turned around more quickly.
‘We have great experience in promotional labels, so the addition of digital will help that area of our business even more. It provides more options.’
Yoshiyama is clear‐eyed about the cultural change that the new press will bring to Kuresa. ‘It is a fundamental change for us,’ he admits. ‘It is not an easy transition, given our background in conventional printing. A lot of work is required in pre‐press to adjust our existing jobs from conventional to digital. But once you have got the parameters right for a particular job, the repeatability means that you can perfectly replicate the same job again just by pressing a few buttons. That speed and ease with which you can recall a job is another key advantage.
‘It has only been two months since the installation. The press is working well. But it will take a while for us to fully adapt. It is a challenge. Our sales team needs to learn how to take full advantage of having this extra option.’
Yoshiyama emphasizes that the support from Durst during the installation process has been first‐class. The press manufacturer runs a technical support office in Mexico, and Kuresa received regular visits from technicians from that office as well as Durst’s Italian headquarters during the installation. Press operators were given three weeks of training and will continue to be trained in the coming months.
Kuresa has converted one of its six Ilma presses into a finishing line for the Durst Tau RSC press. It is equipped with a flexo unit, lamination and die‐cutting. ‘We are using the converted Ilma to start with, but we might invest in something more specialized
in the future,’ says Yoshiyama. ‘We have everything we need to serve our existing clients, but of course, as we continue to grow and attract new business, there might be more capabilities that we need to add.’
Future growth
Kuresa’s investment in the Durst Tau RSC inkjet press is part of a strategy to continue its impressive growth trajectory over the past 20 years. ‘We want to continue to grow in the region, to sell more labels into more countries. We are looking at widening our portfolio to include new options to offer our clients, such as shrink sleeves and flexible packaging,’ reveals Yoshiyama. ‘While this could have been done with our Ilma presses, the Durst machine brings us the advantage of enabling shorter runs.
‘Domestically, we are prospecting customers in the agriculture sector, mainly labels for exporters of berries in clamshell packaging, and producers of Peruvian liquor Pisco.’
The converter is also setting its sights further afield. This year it began a partnership with a Florida, USA‐based distributor for various converters in the flexible packaging sector, which is now selling Kuresa’s labels to brands in the US. Kuresa is its only label printing partner.
‘We are looking at ways to ensure Kuresa’s continued growth,’ says Yoshiyama. ‘We are open to all possibilities for the future, whether that be partnerships with other companies or setting up a factory in a new market, for example.’
Kuresa’s history of international cooperation goes back to the 1980s and remains an important part of the company’s culture. By then, its Pegafan brand of adhesive tapes was one of the biggest in Peru, but a shift in government policy towards importation saw the arrival of foreign tape brands in the local market. According to Yoshiyama, this encouraged the company to rethink its strategy. It began to search for a technology supplier, modernized its production facilities and invested in the training of its workforce. This search led it to Swiss adhesive tape manufacturer Cellux, whose president Dr Daniel Blansjaar – a Dutchman who has lived in Switzerland for many years – then became chairman of Kuresa. His son Guido Blansjaar, also based in Switzerland, is Kuresa’s president.
‘When Dr Blansjaar and his engineers arrived at Kuresa in the 1980s, the performance of our machinery and the quality of our products began to improve enormously. Because of our lack of technical knowledge at the time, the existing machinery had not been used efficiently. The addition of Swiss precision to the enormous practical talent of the technicians and mechanics from Peru quickly gave Kuresa a strong competitive position.’
When Kuresa moved into label production in the late 1990s, Jaime Yoshiyama and his management team traveled extensively, visiting industry suppliers and attending trade shows. The company developed strong relationships with companies such as Netherlands‐based Kolibri Label (now part of Optimum Group) and Spanish converter Germark. ‘We have a management culture of ensuring that the company’s leaders are kept up to speed with the latest technology and advances in the industry,’ says Yoshiyama.
Kuresa’s long‐term membership in Finat is a further example of the company’s international outlook. The self‐adhesive label association’s competitions have provided a useful yardstick for Yoshiyama to compare the quality of Kuresa’s production to that of leading European converters. Its multiple victories demonstrate that it has not been found wanting – indeed, it added two more Finat Label Competition awards last year, in the combination printing and rotary letterpress printing process categories.
Meanwhile in Peru, despite recent political instability (the country had six different prime ministers last year) the local industry is growing and demand for labels ‘continues to rise’, says Yoshiyama. In 2022, as the local economy opened up following extensive lockdowns during the pandemic, Kuresa achieved growth of 25 percent across all three of its core business areas. Growth in the first half of 2023 was up 11 percent compared to the same period last year. ‘There is still huge potential for per capital label consumption to rise in Peru,’ emphasizes Yoshiyama. ‘We are more optimistic about the future growth of the local market than we were two years ago.’
Stay up to date
Subscribe to the free Label News newsletter and receive the latest content every week. We'll never share your email address.