Keeping pace with a changing market
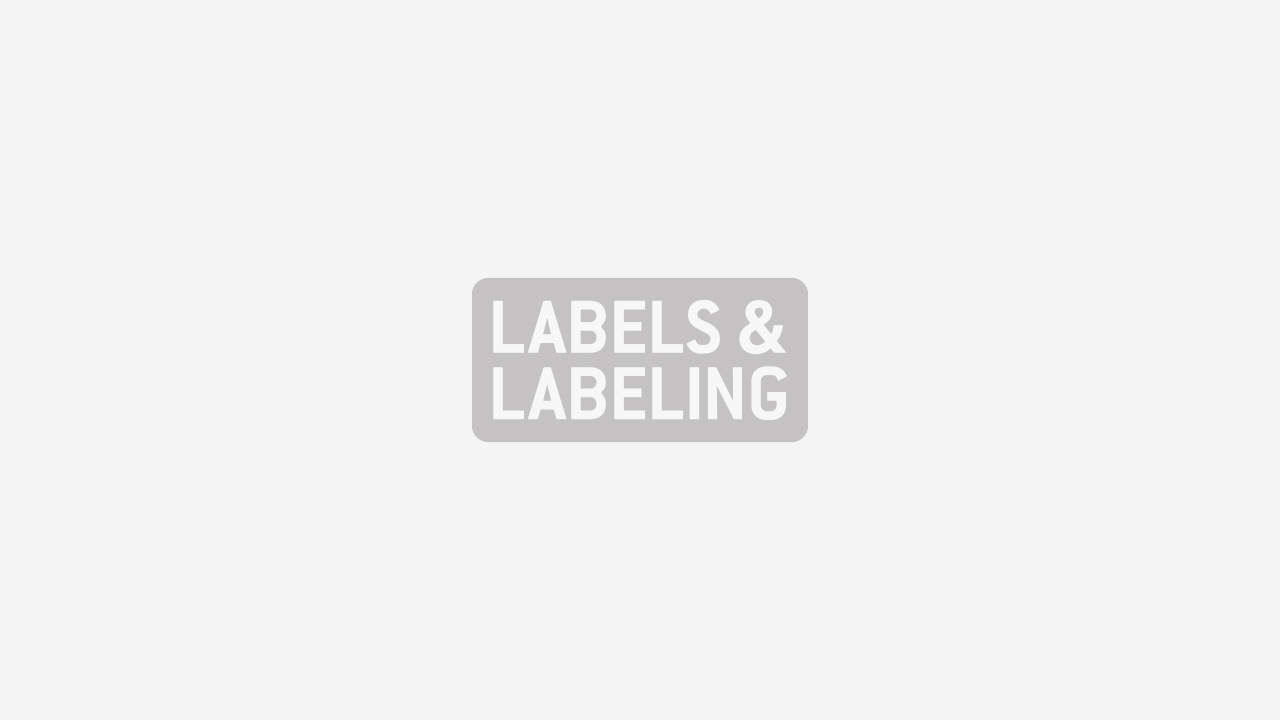
North America editor Danielle Jerschefske looks at how the mid-to-narrow web package printing industry has taken shape in recent years to produce anything the client may need to differentiate their products on the shelf
Modern market dynamics beg for rapidly changing product decoration to enhance the shelf appeal for the excessive varieties available for a single product. The package printing industry has felt this shift over the past few years with lower job runs of many SKUs – still achieving high volumes in total.
Some flexible packagers have realized that the label industry’s advanced machinery can bring production opportunities and improve profit margins, and are therefore shifting their investment dollars from wider web machinery to mid to narrow web configurations. More than half of the region’s top 25 dedicated flexible packaging converters attended Labelexpo Americas, and the 2010 show experienced a 20 percent increase in flexible packaging attendees.
This shift leaves a potentially highly profitable gap in the market for label converters. It is for this reason that Labelexpo Americas 2010 included the dedicated the area ‘Beyond Labels: New Opportunities for the Converter’. Various products were on display for markets outside of traditional labels, which can be produced using the industry’s highly advanced, dedicated narrow and mid web machinery.
These advanced machines are fully equipped to manufacture short-run packaging including flexible packaging, folding cartons, wrap-around battery bands and functional converted products, such as medical pieces and cell phone components that can diversify a label business.
Labels & Labeling’s recent North America Label Converter survey, conducted in January 2011, revealed that over 40 percent of respondents are already producing flexible packaging, while nearly 20 percent are converting folding cartons and 57 percent are producing some sort of ticket or tag.
Paco Label, a Texas-based converter, installed a Nilpeter FA-3 last summer (pictured below), expanding its capabilities to include cold foil as well as rotary screen. This gearless press can handle a wide range of packaging materials with its servo-driven in-feed, and servo motors on all print units. It is equipped with a mid-feed pacer, and the latest P2P automatic register control system.
The installation will allow the converter to take on more complex work and break into the market for highly decorated food and beverage packaging. Paco Label is pleased that the press is able to achieve the quality needed to compete against both gravure and offset, yet with the narrower web, can produce work more economically that’s difficult for its competitors to match.
Dwyer Group in California made a significant investment to move into process color offset shrink sleeve label production by installing an 8-color 38 inch RDP Marathon IVCO press at its Pennsylvania location, and an HP Indigo WS6000 digital press in California, within 12 months. The company is using the digital press to create prototypes to drive sales for the higher volume offset press. This dual platform meets Dwyer’s business model of just-in-time delivery. Initially, prototyping allows the converter to show the quality of the label it can produce, but significantly, the system increases Dwyer customers’ overall speed-to-market, compressing the time-line down to two to three weeks from concept to consumer.
Hammer Packaging, based in New York, was the first North American customer to invest in Heidelberg's new CX 102 Speedmaster. The CX 102-8+L is equipped with a CutStar roll sheeter and Prinect Axis Control color measurement and control system. Hammer Packaging selected the press primarily for its speed and efficiency in printing different film stocks. According to the company, the addition of CutStar will make the printing of film even more cost-effective, because of the way it controls the sheet as it is fed into the press.
The converter is a high-volume producer of premium seed packets, and supplies leading brands like Gatorade, Coca-Cola and Pepsi.
A number of the market’s largest, multi-site converters – Multi-Color, WS Packaging and York Label – have invested in EFI Radius MIS/ERP software systems that can manage the production of a multitude of product lines effectively. The EFI Radius solution is designed to enable an end-to-end, intelligent and optimized management and production workflow for label, flexible packaging, converting and folding carton businesses.
Its recent roll-up into the EFI portfolio places the supplier closer to the label converter’s ear, and the most recent acquisition of Prism highlights how the business is looking to develop more solutions for medium to small package printing operations.
The 2009 recession brought total cost evaluation to the forefront of CPG and brand owners’ decision making processes, which gave digital printers a shoe in. Numerous small and medium-sized label converters have found advantages in the packaging market by selling on total delivered cost, reduced inventories, and improved response time.
Improvements made to market leading machines have allowed their users to produce labels and packaging profitably in volumes that most converters consider medium run lengths – and packagers consider short run. Interestingly, while the sweet spot for the HP Indigo WS6000 is considered to be 15-17,000 feet (4,500 – 5,000m), jobs are being regularly clicked at 40- 50,000 feet.
Vibrant Graphics in Wisconsin manufactures in-mold labels with a thin 0.5mil laminate on an HP Indigo WS4500 digital press, which has given it the ability to hit the mid to small size markets with IML service. The converter’s core competency is the coating. Yet, innovation is two-fold, since the business was able to capture this new in-between sector, giving the market something that it had never had access to before. Prior to Vibrant offering IML, the decoration type was exclusive to long run work and could only be found in the wider format (52in) arena.
The converting process offers the greatest potential for differentiation, and sometimes the most innovation, when it comes to expanding business beyond a typical label.
Delta Industrial’s Spectrum digital finishing machine can be customized to convert a variety of materials. It can offer cut and place web capabilities, and is considered to be ‘plug-and-play’. Vibrant Graphics uses Delta equipment, because of its versatility and flexibility, which allows the business to be flexible when reacting to customer needs. The Spectrum is a semi-rotary system that allows tension and speeds to be changed quickly, and includes a die station for whatever configuration is required.
RotoMetrics opened a new Converting Technology Center at its headquarters in Missouri to demonstrate its advanced die cutting and modular processing equipment. It hosts the new 660 mm (26 inch) Rotary Processing Module, designed to convert a wide range of materials from flexible packaging, to folding cartons and pressure-sensitive labels. The module can perform creasing, die cutting and embossing with solid or flexible dies in widths up to 864 mm (34 inch), and still provide the accuracy needed to compete in the market for re-sealable flexible packaging.
With design life-cycle decreasing rapidly, and increased demand for individualized product marketing, it appears that the best way to service the dynamic needs of brand owners selling products to the ‘socially plugged-in’ consumer population is to establish a multi-level platform that allows the flexibility to produce anything the client may need to differentiate their product on the shelf, effectively and profitably.
Most of the modern ‘conventional’ presses are supported by advanced digital servo drives, internal software, and advanced design to help converters address CPC’s efficiency needs while boosting margins. High Definition digital printing plates have improved the print quality capability of flexo, challenging the likes of offset and especially gravure, while digital printing is beginning to find its place.
The question is not, ‘which process is better’? You need to understand the differences in each process, and their capacity and performance restrictions. Only then, can you determine when and how each one is used.
It is imperative that, as this trend continues to evolve, converters hold the line on pricing, and sell on the opportunities they have with brand owners. In some cases, converters have been able to sell short-run work at 20 percent more per unit but the total cost remains seven percent less. The shape of labels, packaging, printing and converting has adapted to the way the world has evolved as a consumer. There is no doubt it will continue to do so – converters beware!
Stay up to date
Subscribe to the free Label News newsletter and receive the latest content every week. We'll never share your email address.