Heidelberg boosts IML efficiency with rotary die-cutter
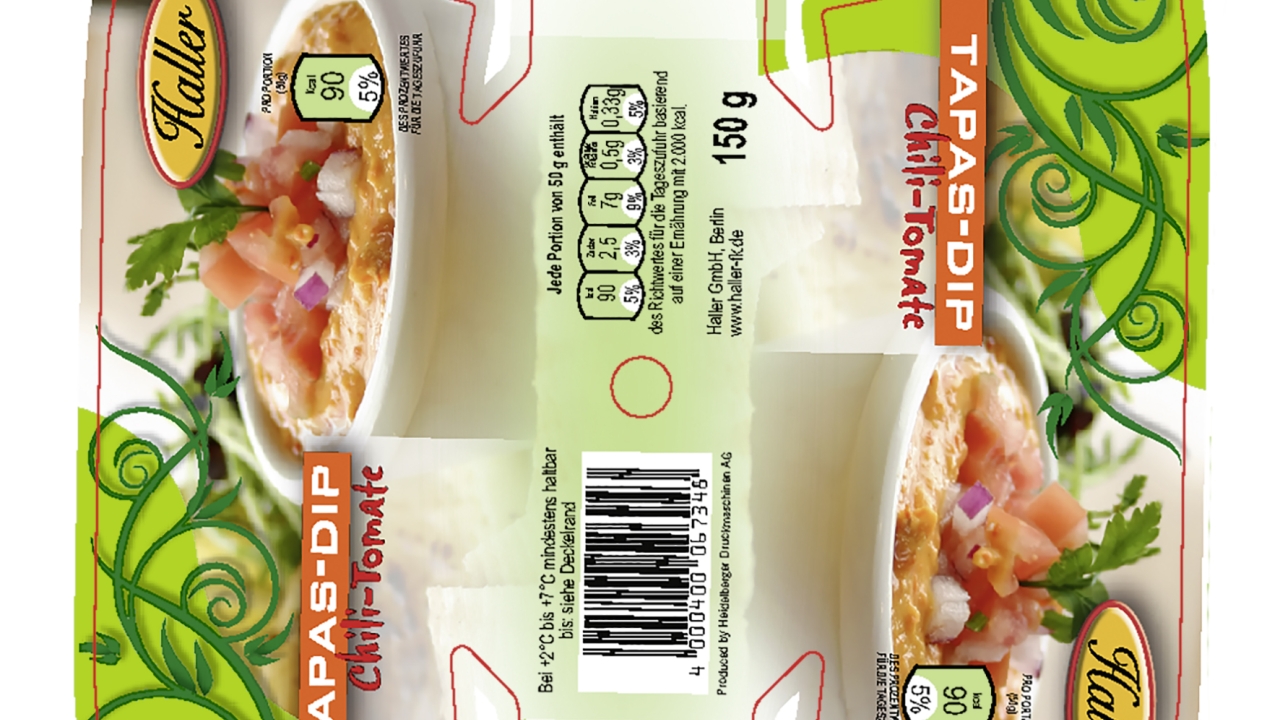
The unit was launched at Heidelberg’s Label Day event focused on sheet-fed offset production for in-mold labels. The company showed for the first time the printing of in-mold labels with food-safe UV LED inks on a Speedster XL106 press equipped with Heidelberg’s Dry Star LED lamp system. Labels were then finished on the new XL106 DD rotary die-cutter.
Why are injection holes important? Where an in-mold label covers the bottom of a container – an increasing trend as end users place more information away from the main branding area – a hole needs to be cut to allow the plastic to be injected into the mold. Holes are also necessary for the thermoforming and blow molding processes.
Up to now this has required a separate off-line operation. Now, by placing the hole punching unit, with integrated waste extraction, in-line with the outline cutting unit, both operations can be carried out in a single pass, greatly increasing productivity.
The specially designed magnetic cylinder on the hole punch unit has a grid of air holes which both suck and blow air – sucking to hold the snippet in place while it is punched, then blowing to eject the waste into a suction hood inside the cylinder. Two separate chambers integrated into the cylinder move the air from blowing to sucking as the cylinder rotates – a fast, accurate and fully mechanical process.
The magnetic die-cutting plate covers all the air holes on the cylinder except the hole to be punched.
The punched waste is taken away to an external storage unit with two removable hoppers.
Production speed of the machine is between 6-10,000 s/ph. and the punching module will handle materials ranging in thickness from 0.05mm to 0.3mm. Minimum injection hole size is 5mm.
As well as IML applications, Philipp Doley, product manager of sheet-fed at Heidelberg Druckmaschinen, sees other possible applications in POS and Sample of die-cut and hole-punched in-mold label packaging: ’The market is changing so if you have the possibility to cut and blend holes you can also speak about different kinds of holes, not only small injections but also the possibility to cut a window and extract the window in the label, or to create hang tags with paper or plastic, or even egg boxes. So maybe this creates a new kind of product.’
Heidelberg has run successful tests with hole diameters up to 15mm on a range of papers. ‘We can leave it to our customers to think about the different possibilities this opens for their business,’ says Doley.
Rotary history
Heidelberg started development work on its rotary die-cutting technology around ten years ago, launching the original Speedmaster XL 106-DD in 2009.
‘This enabled IML label converters to cut any label size on a rotary system. Compared to a flatbed die rotary is faster, uses cheaper tooling and eliminates work-in-progress,’ says Philipp Doley.
‘If you are only able to flatbed die-cut 2,500 sheets an hour and your press is running at 12,000 sheets an hour, work in progress takes up a lot of space. And on a flatbed die-cutter the cutting process for the sheet has to stop completely and speed up 100 percent afterwards, so you always have a hard stop and a hard run. On rotary, the sheet is always moving.’
Based on a Speedster XL-106 coating unit, the XL106-DD IML rotary die-cutter will handle paper and synthetic materials from 50-80 microns at production speeds between 6-10,000 sheet/hour – around twice the speed of the fastest flatbed die-cutter.
The flexible die tooling costs are between 300-1,000 EUR per cutting plate, with a tool lifetime up to one million impressions. Heidelberg estimates that the cost of rotary tooling is half that of flatbed on runs of 500,000 sheets.
A newly developed pin mounting system ensures tight cutting plate registration and pressure setting can be fine-adjusted by one micron increments.
The magnetic cutting and punching dies were developed by Kocher+Beck, in a project headed up by Reinhold Hiller, product manager, In-line Offset Cutting System.
‘The Speedmaster XL 106-DD rotary die-cutter for in-mold labels is certainly the best machine on the market, a revolution in terms of IML label production,’ says Hiller. ’The Heidelberg concept proves that rotary die-cutting is not only much faster than flatbed die-cutting, but at the same time more precise and more efficient.’
As the tool manufacturer, Kocher+Beck was involved from the beginning of the project. ‘The focus was on topics such as feasibility, user-friendliness, speed in setting up/changing the tool and the customer’s demand to punch and remove the snippets very close to 100 percent,’ continues Hiller. ‘A register system guarantees a repeatable, precise application of the tool when changing jobs, and an additional scale facilitates the set-up process.’
A range of options were tested to simplify the punching process and plate handling and to focus the airflow. ‘The good cooperation between machine manufacturer and punching tool manufacturer was the breeding ground for this revolution in the IML labeling,’ states Hiller.
As Hiller notes, the rotary die-cutting unit is optimized for fast job changeover. The die-cutting plate can be changed in just three minutes, and a complete job change including feeder pile change and setting takes no longer than 15 minutes for a repeat job and 30 minutes for a new job.
Since the launch of the XL-106 DD there have been 41 installations around the world, including five fully in-line on Speedmaster XL 105 and 106 presses.
‘A fully in-line configuration only really makes sense if the press is dedicated to IML labels on an industrial scale, with average runs of 50,000 sheets,’ says Doley.
Up to now five of the IML rotary die-cutting units with hole punch option have been sold, so it looks like Heidelberg has anticipated a growing market need.
Stay up to date
Subscribe to the free Label News newsletter and receive the latest content every week. We'll never share your email address.