Press technology trends
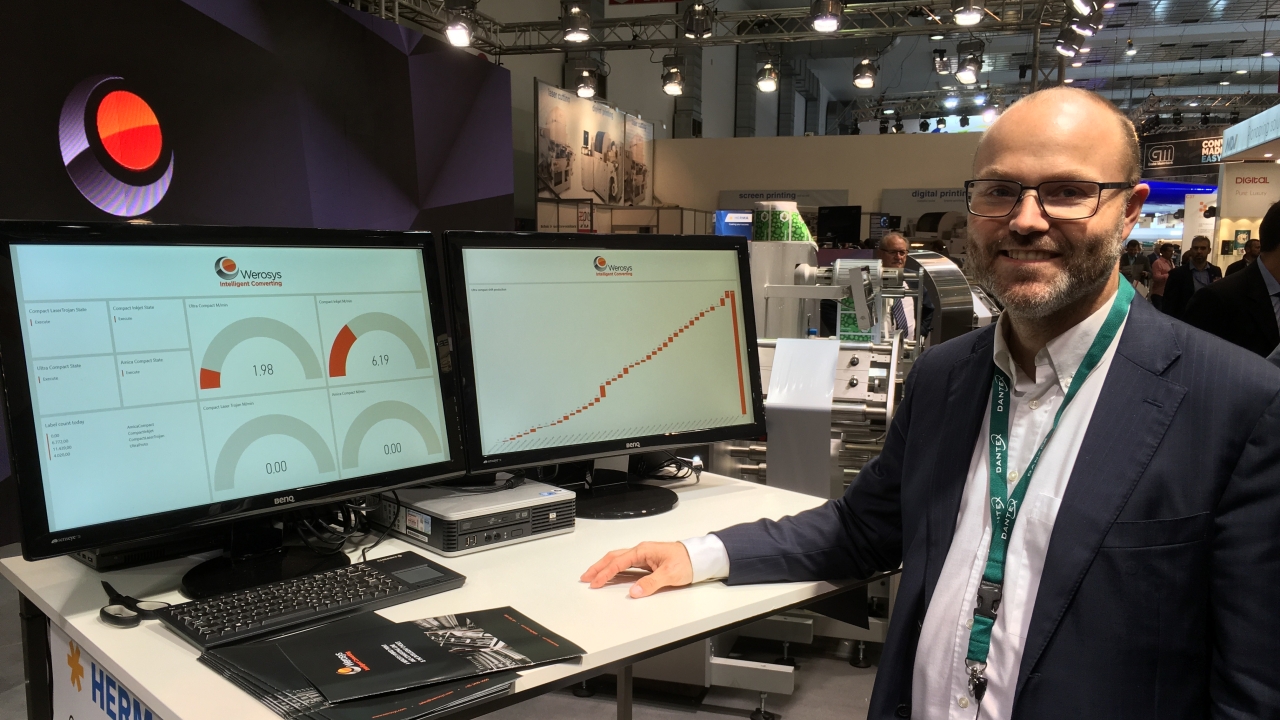
The flexographic press has defied predictions of a slow death at the hands of digital, reinventing itself in a range of new automation and hybrid digital configurations.
Flexo press automation will in the future be offered at a number of different levels. For highly industrialized workflows involving multiple job changes per shift, advanced automation packages now include closed loop print pressure and auto register adjustment: Bobst led the field and is now joined by Edale with its new AiiR (Automatic Inking, Impression and Registration) system, Omet’s Intelligent Cruise control, and MPS, all demonstrating these systems in action for the first time at Labelexpo Europe 2017.
Both Gallus (LabelMaster) and Nilpeter (FA-4*) have launched press platforms with a range of automation options. This extends in Nilpeter’s case to fully wireless press operation via a tablet, including recipe building and job recall.
A key advance for Gallus press users is a new Screeny design operating up to 120m/min, eliminating the speed penalty of using Screen. Another key trend is the introduction of fast, semi-rotary die-cutting systems operating at full flexo press speeds – further reducing make-ready times and tooling costs on short run jobs. At Labelexpo Europe, Mark Andy, Edale and MPS all showed semi-rotary systems in action. The Mark Andy implementation allows converters to change between semi-rotary and full rotary mode from the press control console as the converter moves between short and long run jobs.
We also saw more flexo companies at Labelexpo demonstrating fixed palette print systems with spot color simulation, which will have great benefits in further reducing downtime between jobs. At this point we should also mention developments in automated platemaking – up to now the Achilles heel of the flexo industry no matter how efficient the presses are. This will be the subject of an in-depth feature in a 2018 edition of L&L.
The final link in the conventional press automation chain is integration into standard Management Information Systems (MIS). The problem at present is that press consoles use proprietary operating systems, making this the last area of the plant where double keying is still required. The first manufacturer to demonstrate an open press interface is MPS, which launched its ‘Talk To Me’ bi-directional protocol at Labelexpo.
Data to be exchanged from the MIS to the press includes the customer name, press run, color sequence, tooling, material type and thickness, printing plate code and planning. Data from the press to MIS consists of the operator, printing speed, meters/yards printed, waste produced, set-up and printing time.
Press operators can also access these capabilities remotely using a ‘Talk To Me’ app, available for any Android or iOS smartphone or tablet. Indeed, at the show, visitors were invited to follow the data trail themselves by downloading the app.
MPS is working closely with Cerm and LabelTraxx and Apex International has launched a ‘Talk To Me’ compatible RFID-equipped anilox roll designed to optimize process control. Although all press manufacturers now offer remote diagnostics, this form of connectivity is now being taken further. Omet, for example, has announced an initiative called the Transparent Factory Cloud, which takes in remote machine check-up, data analysis and strategic production planning. This will be aided by ‘Smart glasses’ which will have multiple functions – sending an image of the print in real time to final customer, ensuring printing registration accuracy and connecting directly with Omet engineers for on-the-spot fault finding.
A similar program – minus the smart glasses – has been announced by Gallus.
Hybrid systems
Another key trend sees conventional presses morphing into digital presses – adding bespoke combinations of flexographic print and converting modules to an inkjet print engine. Mark Andy has gone the furthest down this road with the launch of its Digital Plus program, which now includes the Digital Series hybrid flexo UV inkjet press and various configurations of digital add-ons for its Performance series flexo press line. These include Digital Plus Screen, a digital UV inkjet module laying down an opaque white and available both as a rail-mounted option or as a retrofit.
Gallus’ parent company Heidelberg is making a strong push into digital, and the latest narrow web development is an in-line inkjet varnish module, the Digital Embellishment Unit (DEU), available for the Gallus ECS 340 and Gallus Labelmaster UV flexo machine platforms as well as the LabelFire hybrid press.
The DEU applies matt, gloss and tactile spot coating effects in various thicknesses. A joint project, it is built on Steinemann’s dmax technology with Schmid Rhyner developing the UV inkjet effect varnish. The unit supports coating volumes up to 100gsm with a resolution of 600 x 600 DPI.
Nilpeter’s Panorama hybrid press now features tight integration between the FA-4* converting units and digital engine, with no festoon required, and the machine has moved into higher value markets with the addition of Nilpeter’s FP4 flatbed embossing/ foiling unit.
Omet and Durst have meanwhile announced an alliance which sees the new high resolution (1200 x 1200 DPI at 78m/min) Durst Tau 330 RSC fully integrated with Omet’s XFlex X6 flexo press modules.
Lombardi has also joined the hybrid rush with its Digistar hybrid inkjet press, which uses the Domino inkjet integration unit (as does MPS’ Symjet), while Focus continues its collaboration with International Inkjet (IIJ).
A number of digital press system suppliers now offer add-on units for conventional presses.
FFEI and Xaar have worked together on PrintBar Uncovered technology. FFEI developed the PrintBar integration module and management software and offers consultancy to companies looking to integrate the mono print/coating system into presses and rewinders.
Printbar Uncovered is based on Xaar’s new 1003 GS12U printhead, which runs in both grayscale and binary HL (High Laydown) modes. HL is a software technique which allows high build UV varnishes to be applied – up to an 80 μm layer thickness at 25m/min line speed. A double head is available which increases resolution to 720 DPI.
FFEI’s Andy Cook says the company’s own software – which resonates the head combined with LED pinning – has already achieved builds of over 130 microns. ‘We are very close to a height of 250 microns, which is Braiile height, in a single pass,’ says Cook. ‘This will open up completely new opportunities for converters with conventional presses.’
Colordyne Technologies has its 4-color 3600 Series UV–Retrofit, operating at speeds up to 246ft/min across either an 8.5 inch or 12.75 inch (324mm) print width at a print resolution of 600 DPI. This is based on the experience the company gained developing its aqueous Memjet-based press integration unit.
Industrial Inkjet (IIJ) has a new range of compact color print modules for conventional presses based on the Konica Minolta KM1800i printhead with speeds up to 200m/min. ColourPrint HiQ has a native resolution of 600 DPI – claimed with asymmetric screening technology to achieve 1000 DPI ‘apparent’ resolution – with 3.5pl droplet size.
Inkjet Solutions, meanwhile, runs a digital integration service with engineering partner KPG Europe based around CMYK or monochrome UV inkjet modules operating in standard format at 75m/min at 600 DPI, or at higher speeds on request. Domino continues to find new applications for its K600i digital print module, with the latest being digital cold foiling.
Digital presses
The biggest digital technology story this year, and likely to have a major impact on the industry in 2018, is the entry of Bobst and Uteco into the narrow web digital market.
The Mouvent press is a joint venture with Radex, a small Swiss company with a new technology, the scaleable ‘Cluster’ based on the FujiFilm Samba 1200 x 1200 DPI printhead, The Cluster units can work with UV and water-based inks and on any substrate, including labels, flexible packaging and cartons – a textile printer is already under development.
The Mouvent presses are rated at 100m/min, though this will be application dependent. They will be available in both 170mm and 340mm widths.
Uteco’s Gaia digital label press uniquely uses Electron Beam curing technology. It was developed with ebeam Technologies and INX Digital. Up to now electron beam curing has only been seen on dedicated packaging presses, but has been miniaturized by ebeam Technologies to fit inside a compact 4.4 x 1.5m frame – a major technical achievement. The key benefit of EB is it is safe for indirect food contact applications, as there are no photoinitiators.
This is a 4-color system using specialist INX Digital inks. It has a resolution up to 720x360 DPI and speeds up to 25m/min. Gaia is driven by the JetINX printhead drive and ink recirculation system.
A new technology waiting on the horizon is SPGPrints’s Pike 700 UV inkjet hybrid press, which combines 1200 DPI digital imaging with extensive pre-treatment and added value finishing processes, in a single pass, at up 70m/min.
The 700mm-wide roll-to-roll press, now in beta, is based on technology developed by SPGPrints for the textiles market, and features up to 10 inkjet positions in a central cylinder configuration, with CMYK plus white standard. Optional integration of rotary screen printing units is also offered.
Another big story this year has been Xeikon’s adoption of UV inkjet technology, both through its own Panther system seen in the PX2000/3000 press series, but also with the stunning announcement of the acquisition of EFI’s Jetrion press technology.
Xeikon views UV inkjet as a complementary technology to its electro-photographic press range, which it continues to develop with the upcoming launch of the wider web CX500 dry toner press. This machine will have a web width of 520mm, printing at speeds up to 30m/min at 1200 DPI.
Xeikon is also committed to inkjet through the development of its Fusion in-line digital embellishment units. The first commercial unit is an opaque white ‘digital screen’ module, seen at Labelexpo Europe in-line on a CX3 dry toner press.
Another notable trend in UV inkjet is low migration ink systems designed for indirect food contact and pharma label applications.
Durst was the first into this space with a nitrogen inerted unit and new low migration inks for the Tau 330 press, and has now been joined by Screen with an enhanced version of its established TruePress Jet 350UV. The Jet350UV LM machine takes advantage of a faster speed of 60m/min, a sixth color and optional chill drum (all found on the new Jet350UV+ model), and is sold with a new generation of low migration inks developed by Screen.
Another development which points to a wider range of applications for UV inkjet is Domino’s early and successful experiments printing shrink sleeves on its N610i digital press, using the company’s latest UV90 6-color UV-curable ink set and a hybrid press configuration – a flexo station after the digital print module prints the white back layer. The project involves MPS with its Symjet hybrid press and AB Graphics.
Shrink sleeve capability has long been considered a disadvantage for inkjet when compared to liquid toner, as Domino’s Philip Easton acknowledges: ‘Industry research suggests that many of the liquid toner applications are just used for prototype production and early product life requirements. This is mostly driven by high unit cost and slow running speeds. We think the Domino N610i high-speed inkjet solution, running 70m/min combined with a lower cost flexo printed white for the backing, will offer a different proposition and will be a disruptive technology.’
HP Indigo meanwhile continues to build an ecosystem around its core liquid toner technology. Two recent additions point the way the company is moving through 2018. Firstly, the GEM UV inkjet-based embellishment unit, designed to sit in-line with a WS6800 digital press, shows HP Indigo moving towards the integration of key technologies in a ‘traditional’ narrow web in-line workflow.
The second key trend is HP indigo’s continued move into the digital packaging space with the full commercialization of its PackReady instant lamination system. This works in tandem with the 20000 press to deliver a complete short run, VIP-capable flexible packaging system, now including a special coating for retort pouches. At a contract packer, this duo could then feed directly onto a pouch making line (HP did in fact demonstrate this at an earlier open house).
The strategic move into packaging is confirmed by the sales figures: At Labelexpo HP Indigo announced its 50th 30000 digital carton press sale and 100th 20000 flexible packaging press installation.
One final thought: as flexo presses become more efficient on shorter runs – and start to add digital capabilities – digital press suppliers will need to rethink what digital is good at, and focus on these added value applications, whether in low migration, packaging or true variable imaging pressure-sensitive label applications. On the other hand, as digital, and UV inkjet in particular, continues to increase speeds, web widths and resolutions, the battle for the short to medium run arena will continue to heat up. Tough but interesting choices for the label converter in 2018.
Stay up to date
Subscribe to the free Label News newsletter and receive the latest content every week. We'll never share your email address.