L&L turns 40: Foil stamping in label printing
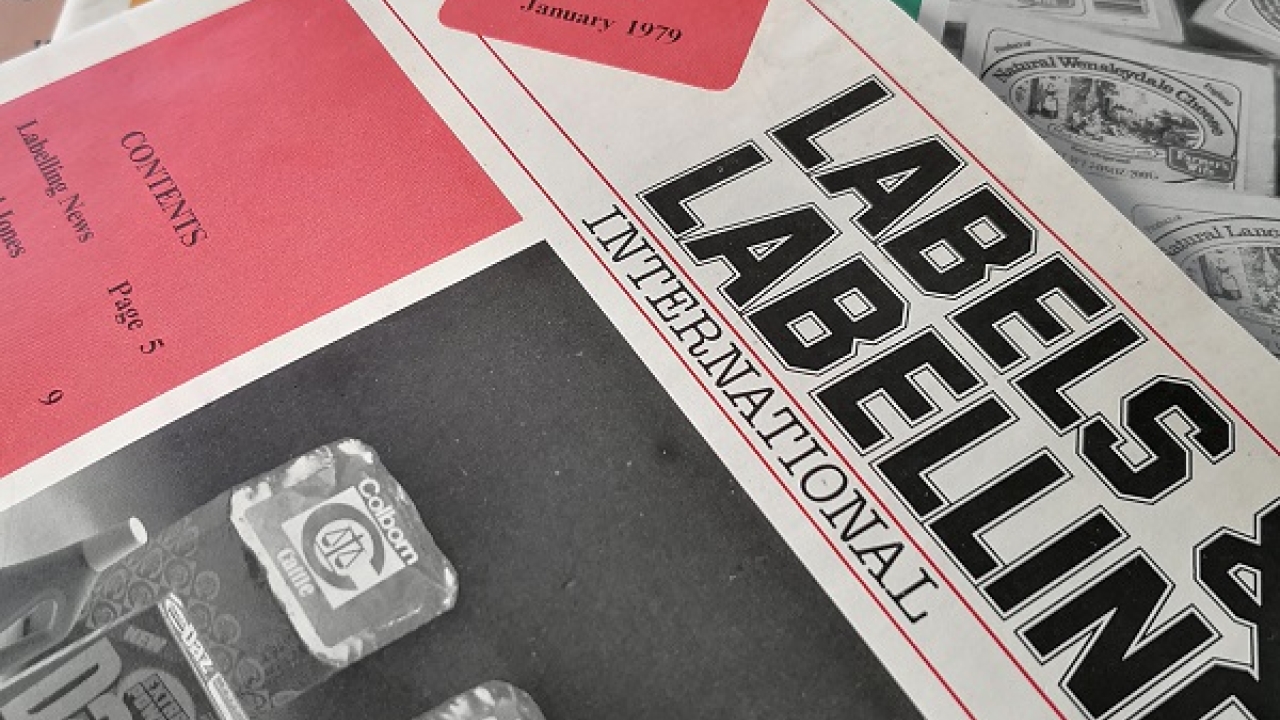
More than ever before foil stamping is being employed today not only as a finishing process but also as a printing method in its own right. In the context of label production, where legibility and point of sale impact are essential prerequisites of whatever printing method is employed, foil stamping has become a well established technique because of the many advantages which the process has to offer, which may be summarised as follows:
- Foil stamping is a dry process.
- No colour mixing/matching.
- No solvent problems.
- Relatively simple equipment.
- Modest space requirement.
- High running speeds.
- Extremely versatile.
- Bright, durable metallic effects.
- High opacity colours.
- Simultaneous embossing if required.
The fact that the process is dry enables labels to be handled and/or applied immediately after printing and avoids the necessity for equipment to be cleaned after use, or between colour changes. Additionally, there is none of the other problems associated with wet printing and solvent usage. The process is very simple to operate and the factors determining the printing quality are easy to adjust and control. Of equal importance are the visual considerations, the range of metallic finishes available can be matched for brightness and durability by no other marking method and the opacity of coloured pigment foils exceeds that of conventional printing inks. It is possible, thus, to apply white on black in a single ‘pass’ to excellent effect.
The Process
The equipment and materials involved comprise a heated press, an appropriate stamping foil and a suitable block or die. The latter will normally be of a harder metal than that employed for conventional printing, although for short run work, zinc plates can be used entirely satisfactorily providing high pressure is avoided. The block is mounted on the heater plate of the press and the stamping foil, a plastic film coated with heat sensitive transferable layers of metal or pigment, is fed beneath the block by means of an automatic mechanism, as is the label stock. The heated block presses the foil into contact with the substrate material, to which it transfers in the shape of the block design. The quality of the finished work depends upon a number of inter-related factors. The machine must be set at the correct temperature, pressure and impression time; the stamping foil selected must be a suitable type for the substrate concerned and the design being applied, and the type of make-ready employed must be compatible with the nature of the work being undertaken – hard for definition work and relatively soft where solid areas are involved.
The importance of the heat/pressure/dwell relationship will be apparent from the nature of the process – the rule-of-thumb is to employ the lowest temperature, pressure and dwell at which complete transfer of the design is achieved, together with adequate adhesion. An excess of any of these factors usually results in loss of detail or dulling, whilst a deficit will produce an incomplete image or loss of adhesion.
Foil Composition
Most types of stamping foil consist of three or four distinct layers or coatings. The carrier is the expendable portion which serves as a base to receive the transferable coatings which are applied layer by layer as manufacture proceeds. The most commonly used carrier materials are glassine paper, viscose film and polyester film.
The latter is more commonly encountered today and is preferred for its high tear strength, good dimensional stability and chemical inertness. Furthermore, the strength of polyester is such that it can be produced in very thin gauges (1/2 thou. is most frequently encountered), enabling fine detail to be reproduced through it without loss of image quality. In the manufacture of a metallised simulated gold stamping foil, the carrier is normally first coated with a release layer. This ensures that the subsequently applied layers will readily transfer when required under the influence of heat and pressure. The release layer is followed by a lacquer, coloured in accordance with the shade of foil being produced. Thus, in the case of a simulated gold, this will be transparent yellow. The next coating is of aluminium which is applied to the film by passing it across an aluminium vaporising source under vacuum. Finally, a heat sensitive adhesive is applied to the back of the aluminium. This will, of course, vary in its composition according to the substrate upon which the foil is intended to be used.
Coloured pigment foils are built up in a very similar fashion having a layer of pigment in the place of lacquer and aluminium. The range of colours, finishes and effects in which stamping foil is manufactured today is considerable. Matt and bright gold in a variety of shades, together with silver and metallic colours, offer much scope for the designer seeking visual impact, whilst pigments also available with a matt or gloss finish – cover an even wider spectrum. Most manufacturers offer a colour matching service to supplement their standard ranges.
Foil Selection
The most common substrates employed in the use of label production are plain, printed or varnished paper, acetate and vinyl. All of these materials are well within the scope of most manufacturers’ ranges, and each requires consideration on its own merits. For example, normally, a different type of foil will be required for a vinyl surface than for plain paper.
Where printed and varnished stock is concerned it is normally advisable to employ a low temperature foil since this will go a long way to avoiding pin-holing due to outgassing or bubbling of the coated surface. The type of design to be applied must also be taken into account since it is very seldom that any one foil is capable both of high definition and solid area work. Care must also be taken in the selection of compatible foils where foil on foil over stamping is involved – it is one advantage of the process that given a two-headed machine a plain white label, for example, can be stamped with a solid coloured or metallic foil and immediately after by whatever other design may be required in a contrasting colour to produce a two tone effect.
Machinery
Foil stamping machines designed specifically for label work have been on the market for many years and have attained a high degree of precision and overall performance. A typical piece of equipment consists of two reciprocating printing heads, both capable of being heated and thus applying stamping foil. Alternatively, where single colour work is involved a cutting forme can be mounted on the second head. Automatic roll feed and take-off facilities for the stamping foil and the label stock are a standard feature of machines of this type. Heat control is normally achieved by means of thermo-couples mounted in the heater blocks of each head thereby ensuring that the block temperatures vary by no more than 2 or 3 degrees C. throughout the run.
Design Considerations
The most effective use of metallised foils calls both for an understanding of the principles of the hot stamping process and the realisation of the essential differences in visual effect between printed and foil blocked images – a design conceived in black and white will often produce a totally opposite effect when reproduced in gold or silver. It is of equal importance for the designer to appreciate the effect of the background colour and the texture of the substrate. The colour will not only determine the degree of contrast but will also add its own tone to that of the gold or silver impression. The surface texture of the substrate will be reproduced in the surface of the stamping due to the extreme thinness of the vacuum deposited metallic layer. Thus, only subdued effects are obtainable on antique and similarly finished stock whilst a cast-coated base produces maximum brilliance from any given foil.
The treatment and design of the stamping block also merits careful consideration. Generally, the most effective foil stampings are based either upon line work, or upon embossed or textured solids. The use of the former can be extremely effective and, in contrast to normal printing practice, visual effect is almost invariably enhanced by impressing the image into the substrate surface.
Apart from the obvious practical and economic advantages that the foil stamping process has to offer in label production, reference should also be made to the unique properties of bright gold and silver effects to confer something of their own intrinsic quality to any article to which they are applied. It is probably for this reason above all others that metallic finishes are so widely employed today in point of sale and packaging applications, and there can be no doubt as to the importance of this particular feature in label production also.
All too often the presentation of a product is marred by its labelling, and particularly the type of label that appears to have been added as an afterthought, when a little more care in design and execution could have resulted in improving rather than detracting from the overall effect.
*This feature was first published in Labels & Labeling issue 1, 1979
**This transcription is a direct replication of the article as published, and before the magazine adopted an American English style guide with a name change to match
Follow Labels & Labeling on Twitter, LinkedIn and Instagram, then share your memories of the magazine using #LnLturns40
Find out how to join in with Labels & Labeling’s 40th anniversary celebrations here
Stay up to date
Subscribe to the free Label News newsletter and receive the latest content every week. We'll never share your email address.