Namibian flexible packaging in the spotlight
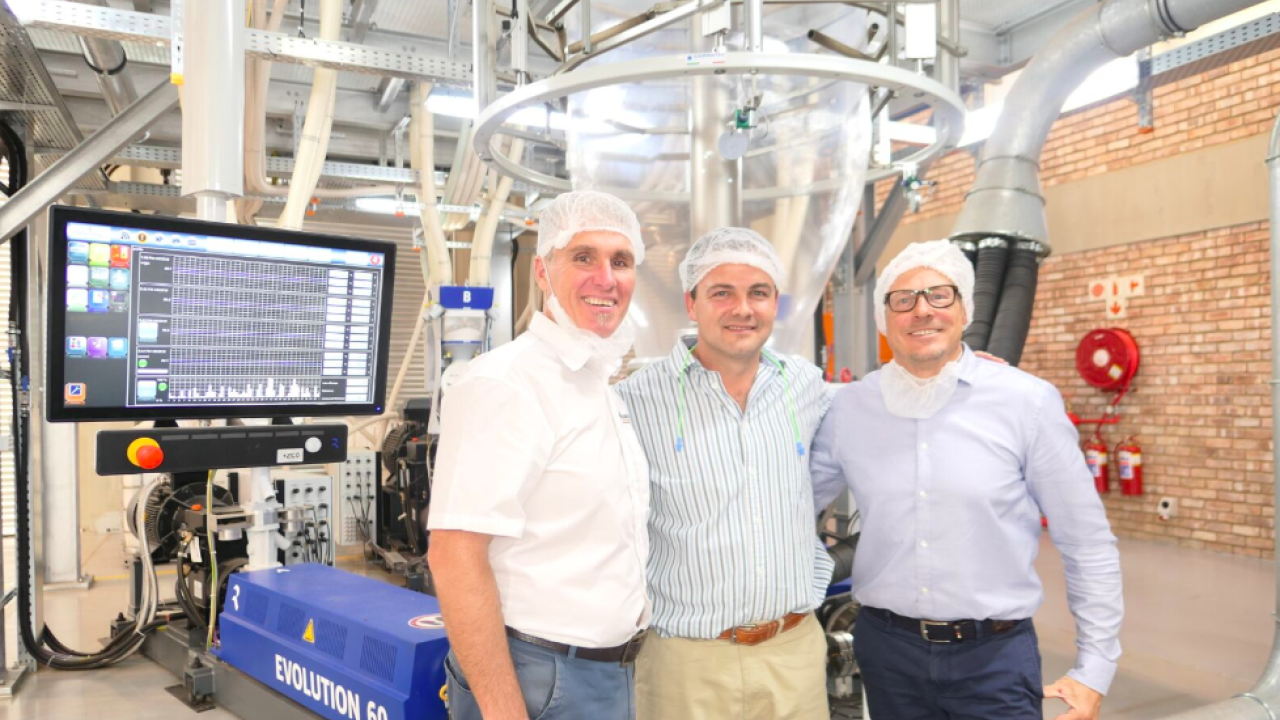
The journey began around a New Year’s Eve barbeque fire in 2010, when Wernich Meyer mentioned to his friend Johan Struwig that his South African company required a packaging film distributor in Namibia. Struwig, looking for a meaningful change from his financial services management job, decided to take up the challenge.
His first opening came when Namibia Breweries Limited (NBL) placed an order for stretch hood film, with the proviso that local manufacture would be undertaken once business reached adequate volumes.
Fuelled by this ultimate goal and using NBL as a reference, Namibia Plastics went from strength to strength – employing more people, diversifying into printed shrink films and establishing a depot at Walvis Bay harbour to service the fishing and salt packing industries.
The range continued diversifying into tubing, sheeting, pallet wrap, a variety of printed bags, and film for food-grade form-fill-seal applications. These key products, making up more than 80 percent of the company’s turnover, have helped to grow a significant customer base across the beverage, salt, fish, poultry, milling and cement sectors.
Targeting sustainable local production
Seven years after inception, the business reached sufficient volumes to obtain finance to build a factory and to make the move into manufacturing.
The year-long construction process for the 2,660sqm state-of-the-art manufacturing plant started in March 2017.
Although Windhoek isn’t currently experiencing power supply problems, the plant has been designed solar-ready to maximize the city’s sunny conditions, in keeping with the company’s environmental sustainability mission. This also includes a less water-intensive operation that means process water is recirculated throughout the factory to keep machines cool. In addition, equipment is selected with specific environmental and energy saving benefits in mind.
Namibia Plastics is driven by the slogan, ‘We’re all about less plastic’, which promotes reducing, reusing and recycling principles.
Stretch hood substrates are extruded on a Reifenhäuser Evolution three-layer blown film line, allowing the film to be downgauged, without compromising quality. With an output rate of 250 tons/ month, it was commissioned in October 2018 by Southern African distributor Sabre Equipment.This technology has already helped customers to reduce the amount of plastic required to pack products by some 20-40 percent compared to monolayer films.
According to Reifenhäuser, while it’s difficult to simultaneously offer downgauged film with the necessary clarity, strength and flexibility in a monolayer construction, a coextruded three-layer film provides the optimal holding form and stretchability.
Namibia Plastics plans to become a leader in the recycling and reuse of plastics, with significant developments being brought to life in the latter half of 2019.
‘By supporting and implementing new recycling campaigns, designing and producing recyclable plastics – viewed as valuable and kept in the economy and reused in packaging – we can help address environmental waste and unemployment issues,’ Struwig maintains. ‘We will, for instance, create a closed-loop system by ensuring that shrinkwrap returned by customers and end users to our recycling plant is sorted, washed and converted back into shrinkwrap.’
World-class printing wrapped up
In October 2018, just six months after the plant’s official opening, Namibia Plastics celebrated its first significant steps towards realising the goal of curbing 50 percent of plastics packaging imports by producing printed shrinkwrap for NBL’s Windhoek Lager six-pack beers on a Comexi F2 MB flexo press.
‘Comexi shares our vision of making the flexible packaging printing and converting industry more environmentally sustainable,’ says Johan. ‘We chose this CI press because it uses 58 percent less power, 72 percent less gas and 80 percent less compressed air than the previous version.’
According to Miquel Gironès, Comexi’s area manager for Africa, this model shares the patented Flexo Efficiency concepts of ergonomics and accessibility with the performance and robustness of the rest of Comexi’s F2 flexo press range.
Back-up service is provided by Comexi agency Cape Town-based Advanced Packaging Technology.
Stay up to date
Subscribe to the free Label News newsletter and receive the latest content every week. We'll never share your email address.