Nilpeter upgrades US headquarters
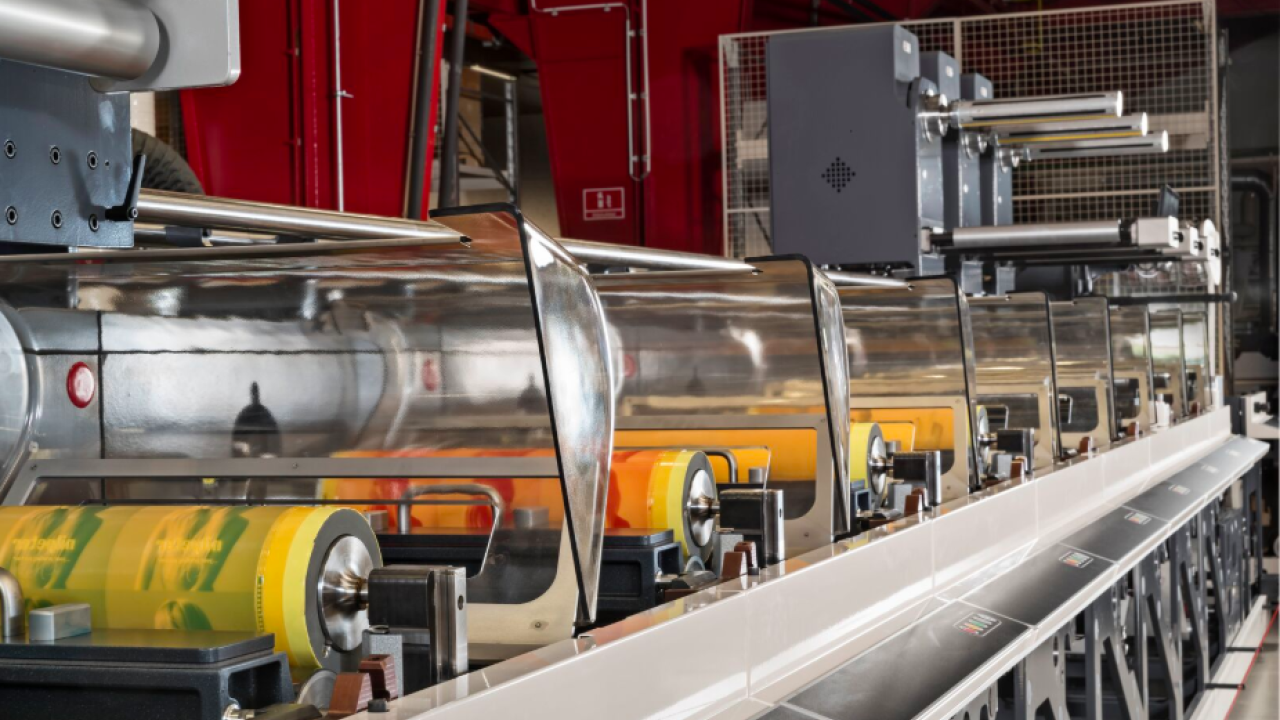
In 2015, the company began renovating its Cincinnati, Ohio-based US factory and front offices. Also included in the remodel was a shiny new showroom to host customers for press demonstrations or open houses.
Walking into Nilpeter USA is like taking a step into the future. A robot-operated forklift moves along a rack at 30mph to pull parts and retrieve components that are then moved to an automated CNC machine that creates the frame for the new FA line press. Building a module used to take 20 hours; it now takes six, and when finished, each part is identical. Tools in the machine shop are tagged and alert the operator when they’re dulled or need to be replaced.
Nilpeter has created a standardized approach to machine building and smart manufacturing.
The new FA
Nilpeter manufactures flexo presses on both sides of the Atlantic, which means more support and flexibility to meet customers’ demands, says Paul Teachout, vice president of sales and marketing at Nilpeter USA.
The Ohio facility will be the manufacturing site for North and South America for Nilpeter’s new FA flexo line press. Since launching the new press at Labelexpo Europe 2017, Nilpeter has sold 40 new FA line presses – 20 in Europe and 20 in North America (see boxout).
The new FA line is equipped with what Nilpeter is calling ‘clean hand technology’, meaning the press minimizes hands-on press interaction, and ensures clean hands during operation. All job data is saved on the press so jobs are easily recalled, and the press will auto register for an automated set-up. The new press has replaced manual knobs and controls with touch buttons, which Nilpeter believes will resonate with younger press operators.
‘If you grew up doing this,’ Teachout says, pausing and miming video game play between two hands, ‘that’s the generation we’re targeting.’
The company’s investment into a fully automated manufacturing facility mirrors how it’s trying to market the new press: fully automated efficiency. ‘We’re practicing what we preach,’ says Larry DeGirolmo, president of Nilpeter USA. ‘This wasn’t cheap, but it was worth it. Not only did we change what we’re doing with our equipment, but we had to change our cultural standpoint.’
As industry trends change and label manufacturers are faced with an aging workforce, Teachout says it’s imperative that OEMs recognize and address that problem.
‘We needed to address the workforce challenge that’s affecting all manufacturing. We can’t just preach it. We have to live it,’ Teachout emphasizes. ‘It was important for us to address that because that’s a real challenge our converters are facing.
‘We have restructured our operation to meet the needs of industry 4.0 with big data and consistent manufacturing between global manufacturing sites. We are now much more efficient with less. Now we have the ability and experience to share this culture with our customers. To offer the most sophisticated 4.0 offering to them so they can do more with less and engage with a modern workforce.’
Stay up to date
Subscribe to the free Label News newsletter and receive the latest content every week. We'll never share your email address.