Omet unveils mid-web offset press
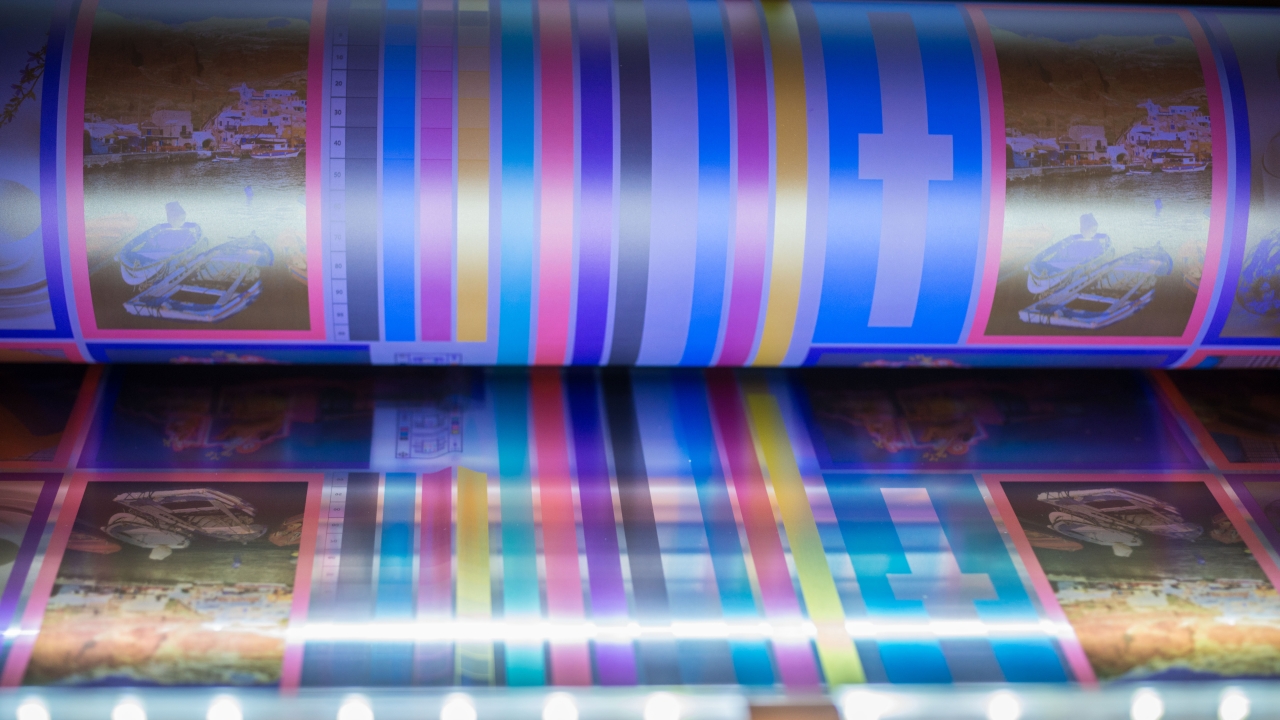
Omet has launched the Varyflex V4 Offset press, a sleeve-based combination machine integrating electron beam drying and targeted at the flexible packaging and film label markets.
The V4 Offset press is available in 670mm (26in) and 850mm (33in) widths and operates at speeds up to 400m/min (1,312ft/min) with a variable print repeat between 16-32in. It will print materials as thin as 12 microns.
‘This new press is able to satisfy not only the need for high printing quality but also for high density color applications thanks to the combination of high quality offset technology and newly designed flexo stations,’ says Marco Calcagni, commercial director at Omet. ‘The Varyflex V4 Offset is highly competitive in this ever-changing market where job runs are shorter and shorter and the alternative printing solutions, like rotogravure and CI flexo machines, add higher production costs to low flexibility and limited configurations.’
Calcagni sees offset quality, along with lower plate costs and far shorter plate-making times, as key advantages over CI flexo and gravure. Omet estimates the crossover point with CI flexo and gravure at around 100,000 sqm, and claims the V4 is also highly competitive against digital on very short runs.
In terms of print quality, with a minimum dot close to 0 percent and uniform transfer onto the material, Calcagni says offset at least matches gravure while being a more flexible process. It is superior at high resolutions both to flexo and digital. ‘It is the best solution for CMYK and vignette printing, with better results in light/dark areas and fine lines.’
Rapid job changes
Rapid job changes across different repeat sizes are enabled by Omet’s Easy Sleeve format change system with automatic pressure adjustment. The blanket and impression rolls automatically compensate for plate gap bounce, helping guarantee print quality and register stability. There are a total of 10 direct-drive motors in each printing unit, allowing fully automatic set-up of the press.
The demonstration press at Omet’s Lecco plant uses Rossini’s lightweight plate mounting sleeves constructed from a fiberglass core coupled with aluminum outer with polyurethane/honeycomb intermediate layers to give high levels of dimensional stability. A protective steel ring integrates the register notch.
The sleeves incorporate RFID tags for automatic identification of the print repeat, helping avoid the wrong job being put on the press. It also allows a check on blanket wear. A special trolley, the Revolver cart, allows sleeves to be rapidly removed and replaced. Each Revolver cart carries up to eight sleeves and services three printing units.
The ink ducts consist of 27 laser-carved remotely controlled independent sectors, and the ink train is constructed from 20 idling rollers and three oscillating temperature controlled ink rollers with an automated washing system. There are four form rollers on the plate with constant right, left and center ink-and-water or water-only dampening.
The direct driven flexo units are also sleeve-based, both for plate and anilox, and will run up to 400m/min.
The Varyflex V4 Offset incorporates automatic adjustment of cross- and machine-direction print register using a multi-camera scanning system. In offset mode, automatic register control balances incorrect plate mounting or compensates for substrate stretch.
The press allows considerable flexibility, printing either Wet-on-Dry (mounting UV lamps between printing stations) or Wet-on-Wet with either UV drying or electron beam curing at the end of the press.
Electron Beam is a simple system to control, with only three variables: energy (penetration), power (throughput) and dose (effect on substrate). ‘The advantages in the print industry are consistent high performance, energy efficiency with no heat generation, better adhesion regardless of color and no photo-initiators – so nothing to migrate and no odor,’ says Elsa Callini, business development manager at unit manufacturer ebeam. ‘The result is completely food-safe packaging.’
EB curing with low-migration inks is VOC-free, giving it a health and safety advantage over solvent-based systems, says Callini.
Stay up to date
Subscribe to the free Label News newsletter and receive the latest content every week. We'll never share your email address.