Pushing finishing forward
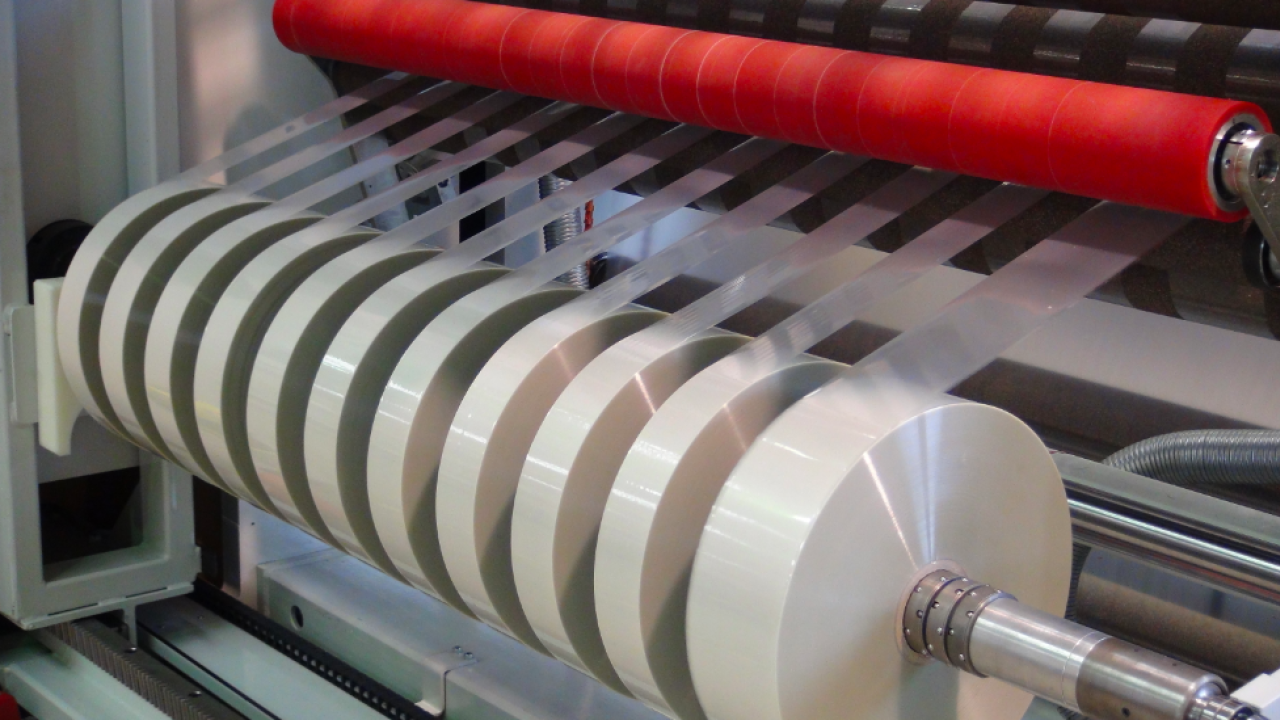
For Gabriele D’Onofrio, general manager at Labeltech, this means requests for more complex and advanced machines such as modular converting systems to finish rolls from digital label printing machines. Luca Goldoni, sales manager at Cartes, says: ‘Digital presses have certainly simplified, speed up and made the printing of labels more versatile, but they probably also have “flattened” the “artistic” result of the embellished label.’
At Lemorau, reacting to this evolution in the industry has centered largely on creating fast, efficient and affordable digital finishing systems. These entry-level (EBRM+) and modular (MEBR+) systems can provide options for customers either adding digital finishing or preparing for their future needs.
France-based Smag Graphique is working to extend its collaboration with the main digital and inkjet press manufacturers to propose finishing customization capabilities as standalone or integrated in-line hybrid systems. Smag has also focused on optimizing the development of its new generation finishing equipment to match high-speed requirements and increase workflow connectivity. Labeltech sees customers asking for bigger machines, able to handle bigger and wider rolls. Rotoflex’s wider VLI-800, for example, has been designed to support the HP Indigo 20000 and growth in short runs of digitally printed labels and packaging.
Barrie Homewood, sales and marketing director at Atlas Converting Equipment, continues: ‘We have many customers who utilize wide web roll-to-roll applications (800mm-plus) who are experiencing label materials becoming thinner in gauge and narrower in width. This brings its own challenge to the slitting process. It also means that efficiency is vital.’
Labeltech’s Gabriele D’Onofrio adds: ‘We are increasing the size and the solidity of our slitter rewinders, as well as developing new modules that are more versatile in converting.’
A smaller footprint Rotoflex DSI provides such versatility in converting by offering digital finishing and die-cutting, integrated with semi-rotary module. UV flexo print-cure, cold foil and lamination can be integrated too.
Cartes’ Luca Goldoni says: ‘Going back to 2012, the year in which the first GT360 series machine was launched, and making a comparison with what is requested and produced today, we are talking about different eras. Initially the configurations of the machines produced were limited to three or four units, nowadays the trend is to produce much more versatile and complex machines, with a potential of embellishing able to amaze the market. The challenge is based on automation, working in-line with other machines (digital and non-digital), and the possibility of making our GT360 and Gemini machines highly automated.’Goebel IMS group marketing manager Kerstin Stumpf-Trautmann notes how the company’s customers are increasingly looking for optimized and highly efficient technologies. A new fully automatic MPW slitter rewinder with coreless winding is designed to facilitate more efficient production for those manufacturing and converting paper rolls with short running lengths. Coreless winding is realized through a modified winding process with specially designed rewind shafts.
Further, the deepening strategic partnership between Goebel IMS and Laem Systems has expanded the machine portfolio for primary, secondary and converting industries as well as slitting and winding. This has created a complete portfolio of technology suitable for various applications along the value chain. The two companies are now jointly executing projects.
Software David Grenwis, marketing manager at Delta ModTech, further notes that label finishers are ‘always looking for ways to decrease downtime.’
To facilitate this, Delta ModTech has made advancements to its Intelli-mod control system to make the controls simple for the operator and automate steps where possible. On-screen instructions walk users through the set-up of the Spectrum finisher and machine settings can be stored as individual product recipes to be recalled.
Atlas’ Barrie Homewood sees machines sharing information from upstream and downstream processes becoming standard in the future, which will increase the efficiencies of the complete manufacturing process for customers.
Lemorau’s slitting rewinding and finishing machines come Industry 4.0 ready while Refine Finishing CTO Bjarke Nielsen notes how he has been talking about and representing Industry 4.0/ IoT through finishing equipment for a number of years. This will continue to be integral to the new-look Refine Finishing product portfolio, centered on its Compact series, to drive productivity and automation. Data will also be used to enable machine maintenance and remote support.
With Siemens’ Industrial Edge FFS technology, analysis of machine data helps to identify process errors automatically. Via frequency analysis and the comparison of frequencies with a reference list containing the mechanical data of all the machine components, the element causing the failure can be automatically identified.
KTI product engineer Chris Plude envisions a future where the operator interface includes complete set-up and operating instructions for the machine. ‘This puts everything the operator needs to know about the machine at his/her fingertips. It could also include a link to the factory production system for downloading and uploading job information. Technology provides us with some powerful tools to work with and the OEM needs to constantly explore new ways to leverage those tools.’
An example from elsewhere in the value chain is Siemens’ near-AI LECo self-learning compensation technology, which is able to overcome the limits of mechanics and conventional control technology using digitalization and intelligent software to improve print accuracy. Grenwis identifies artificial intelligence in machine controls as already making Delta ModTech’s machines smarter. ‘The prevalence of Industry 4.0 will give finishers real time information on the status of their equipment and on the production and quality of their products. The ability to monitor all phases of your manufacturing allows you to stay ahead of issues that could slow production. For example, monitoring raw materials such as inks and substrates helps prevent shortages and waste. Real-time feedback on your machine’s health allows you to plan for preventative maintenance and shorten downtime. Data logging of both pass/fail and critical tolerance dimensions, critical quality inspection data can be sent to the end user before the product reaches their shipping department, providing confidence in the product and decreasing delivery time.’
Hardware
On-machine, the increased access to and use of data has made modern systems highly automated. KTI’ Chris Plude explains: ‘There are a number of tasks traditionally performed by the operator on a turret rewinder and the good news is that the technology exists to automate many of those tasks. The bad news is that automation is expensive.’
Plude gives as an example KTI’s new automatic core loading system, which has been developed to handle a broader range of core sizes at or below the price of feeder bowl systems, providing an improved ROI on the expense. Other tasks ripe for deeper automation include slitter positioning, finished roll closure, and finished roll removal and conveying.
The Labeltech Lavaredo automatic slitter positing unit is the result of such an appetite for automation. Recent upgrades have been made to speed up production and expand the unit’s capabilities, such as compatibility with razor slitters, lateral adjustment monitoring and semi-automatic opposite slitter placement.
Stephane Rateau, general manager at Smag Graphique, says: ‘Thanks to servo motors and automation, the machines are now able to register the jobs and provide automatic pre-setting features.’
Smag’s portfolio includes the new table-top Vega 2 rewinder allowing the web to move forward and backwards in a continuous or step-by-step mode for control applications. The machine can be fitted with web guide, camera, and inkjet or laser printing option. Its modular finishing lines, Digital Galaxie and E-Cut Generation III, can integrate similar options to enhance the finishing process – from flatbed screen printing at 25m/min, and flatbed hot stamping and embossing at 45m/min, to web treatment, UV flexo module, spot varnish, cold foil, laminating, inspection, laser cutting and sheeting, as well as die-cutting at 70m/min in semi-rotary mode.
Rateau says: ‘The best performance nowadays is achieved with semi-rotary die-cutting that provides an excellent cutting quality level coupled to low cost tooling at a standard speed of 60-70m/ min. Magnetic plates are now easily and quickly delivered at very affordable prices.’
Grafotronic’s Q-Load is an automatic side-loading system for the quick change of magnetic die-cutting cylinders, while Rotoflex claims die changeovers are achieved in 30 seconds or less on its Rotoflex DF3 off-line converting option. DF3 uses semi rotary and rotary quick-change die-cutting technology in addition to flexo stations, which it says accelerates the finishing process.
R&D
For Atlas’ Barrie Homewood, the technical demands of the label industry mean ‘a continuous R&D program to find the most efficient and market leading ways of processing the wide range of materials used in different label applications.
‘These include PSA, shrink, wraparound, thermal and in-mold. These all require different handling through the slitting and rewinding process.’
Cartes’ Luca Goldoni confirms the changes in end uses and market trends represent a continuous challenge, but sees this as an ‘incentive to innovate’.
‘Every market, every customer, every production environment, every sector, requires specific solutions to allow each label producer to express themselves at their best.’
For Labeltech’s Gabriele D’Onofrio, this will result in future machines becoming more modular and standardized.
‘Modularity will be extended to all our models to obtain smart solutions with few devices and give the customer the chance to adapt their machine to market changes years after purchasing.’
Lemorau’s Susana Teixeira identifies future machines as being more compact, faster and efficient, a view Atlas’ Barrie Homewood concurs with. He concludes: ‘In the future, machines will be compact, fast, automated and solution-based.
‘Floor space is expensive, so naturally our customers want compact machines. We have to keep ahead of the upstream process, so speed is essential. A solution-based approach means that we are not just supplying a slitting machine, but a fully integrated solution which may incorporate additional equipment to provide a turnkey solution.’
Stay up to date
Subscribe to the free Label News newsletter and receive the latest content every week. We'll never share your email address.