Faller Packaging implements EyeC inspection for pharmaceutical quality control
German converter deploys Proofiler 1200 DT systems to eliminate defects in production processes.
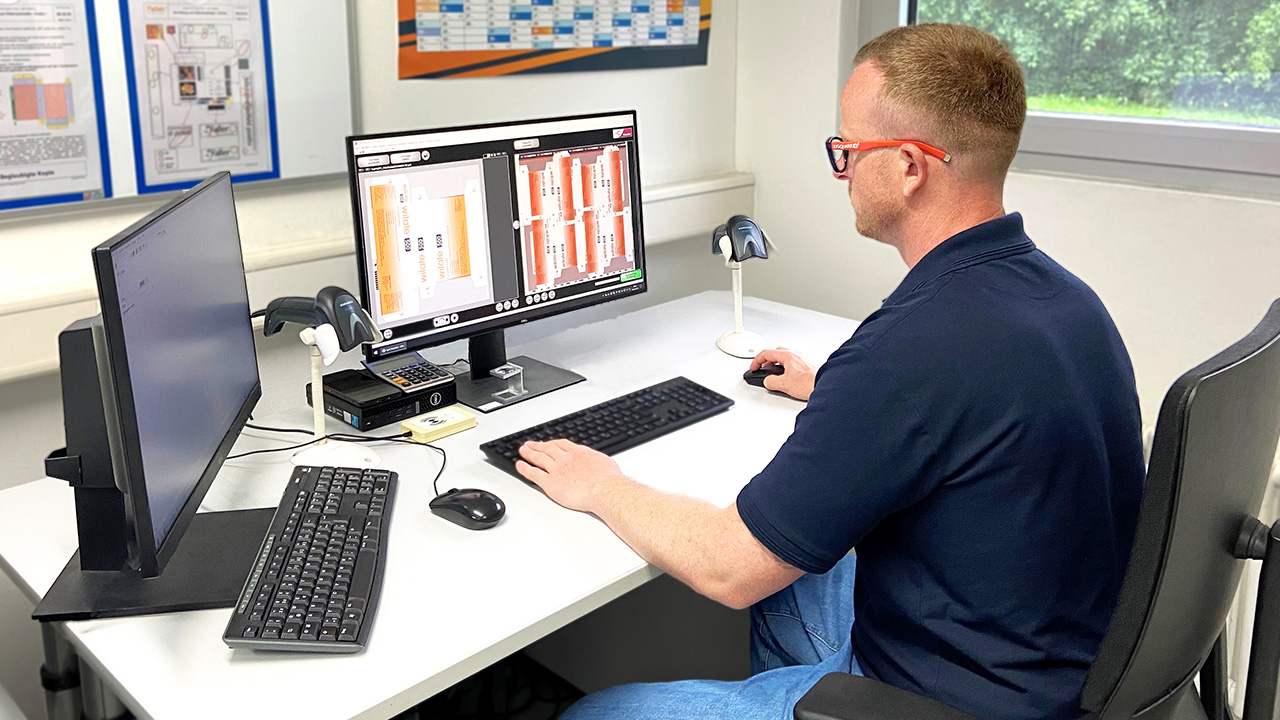
August Faller has installed EyeC Proofiler 1200 DT inspection systems at two plants in its Print Service division to enhance quality assurance for pharmaceutical packaging production, achieving zero-error tolerance in critical manufacturing processes.
The German pharmaceutical packaging specialist, which employs approximately 1,500 people across nine locations, has selected scanner-based off-line inspection technology to detect the smallest deviations in text, colors, graphics and codes before products advance to downstream processes.
'We aim to monitor production as reliably as possible, which is why we carry out a thorough inspection after every single process step within production,' said Andreas Hug, team lead print service at Faller Packaging.
The company sought a digital approach capable of preventing economic damage from defective products while increasing efficiency and process reliability.
Faller Packaging emphasized user-friendliness, flexibility and future-proofing when selecting the inspection technology. The EyeC system impressed with ease of use, quick familiarization and flexible adaptation of inspection parameters for different requirements, combined with high image resolution for precise detection.
'An important criterion was that the inspection system should be simple and clearly structured to minimize any sources of error during operation,' said Hug. ‘The pharmaceutical packaging industry demands the highest standards for accuracy, legibility and safety, where even minor errors can lead to costly rework and regulatory problems.’
The Proofiler 1200 DT systems combine intelligent software with high-resolution flatbed scanners, enabling objective quality control by digitally comparing print products against approved PDF templates. The technology checks both print quality and content accuracy, with the last printed sheet of each job inspected after the printing process.
'The inspection system ensures that only flawless goods are sent for further processing,' said Hug. 'This allows us to streamline rejects and rework, increase customer satisfaction and at the same time optimize the efficiency of our production processes.'
The implementation has enabled early identification of quality problems before defective products reach downstream processes. High image resolution and flexible parameter settings ensure consistently high standards across diverse product requirements for the company's folding cartons, leaflets, self-adhesive labels and combination products.
Faller Packaging has deployed EyeC systems across multiple sites, including Binzen, Gebesee, Schopfheim and Worms, for both print sample inspection and 100 percent inspection, demonstrating the company's commitment to quality and process reliability.
'EyeC is a reliable partner for us,' said Hug. 'They understand exactly what we need and work with us on approaches for the future.'
Stay up to date
Subscribe to the free Label News newsletter and receive the latest content every week. We'll never share your email address.