Digital all the way
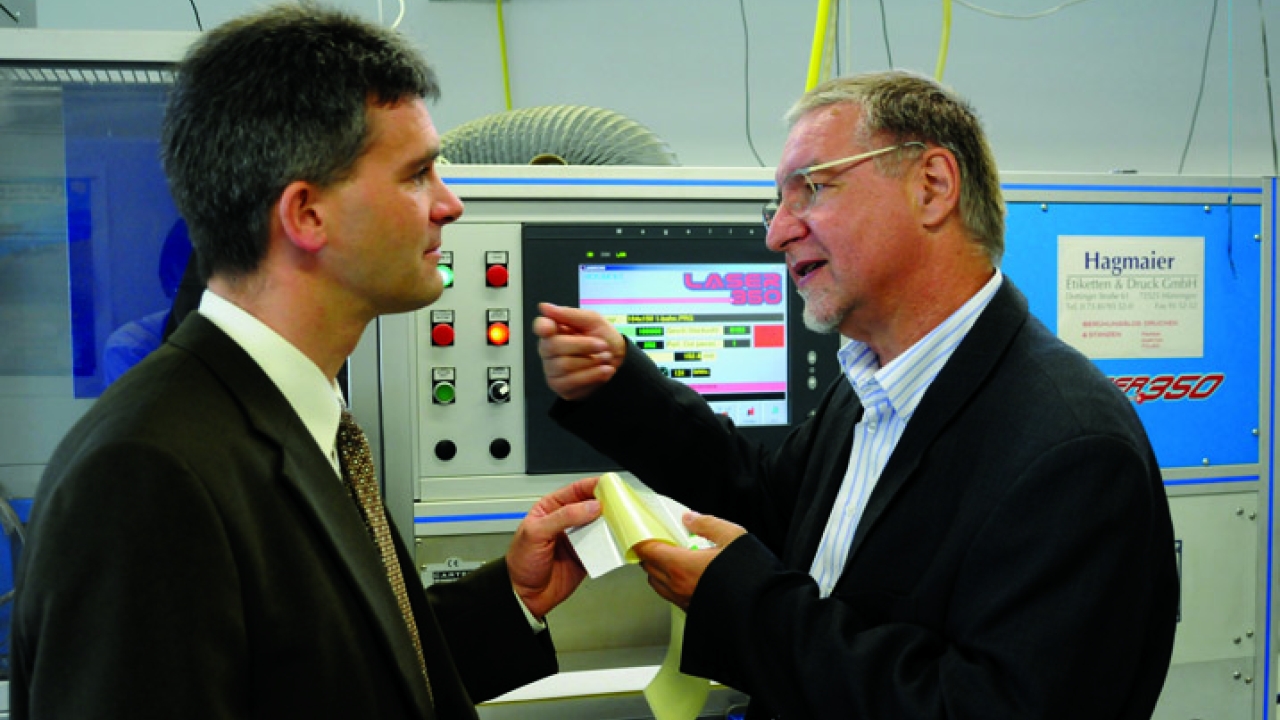
Leading German converter Hagmaier Etiketten is now printing and die-cutting some of its products in an entirely contactless operation. Andy Thomas reports on a joint industry project which also required adhesive coating to be applied within very small tolerances
In an unassuming industrial building in Münsingen business park in the hills of Swabia in southwest Germany, Werner and Thomas Hagmaier, the two managing directors of Hagmaier Etiketten – or Hagmaier for short – are at the forefront of the laser die-cutting revolution.
‘When we started to experiment more than 10 years ago, we dreamt of introducing contactless die-cutting one day, and of a quiet, maintenance and wear-free operation,’ says Werner Hagmaier. Although the brothers have long since realized the dream, ‘only now are we on the threshold of a boom in laser die-cutting,’ predicts Werner Hagmaier.
First all-digital production line
Hagmaier has commissioned what it believes to be one of the first all-digital production lines, based around a Cartes 350 laser die-cutting machine and CSAT LED inkjet printer.
The Cartes machine is producing labels virtually indistinguishable from conventionally cut labels, according to Werner Hagmaier, and has extended the application scope of labels into completely new segments.
A label that detects magnetic influence is one such example. It can be used to protect electricity meters against tampering. Another is a patented gravity indicator label, which indicates whether a product has been exposed to severe shock or impact. ‘That can be a critical factor,’ explains Hagmaier, ‘given that sensitive technical devices, such as computers and cameras, are being sent by parcel post these days. This label enables the addressee to refuse a parcel if he can see, without opening it, that it has already been dropped at least once.’
Such special-purpose labels consist of very delicate structures; some segments of the substrate are pierced 99.9 percent, but not cut all the way through. ‘It would be extremely costly to achieve the same result reliably, and in way that can be reproduced a million times, with a conventional die-cutter,’ points out Hagmaier. It is now easy to understand why the laser die-cutting machine, although originally intended for small jobs, is well established at Hagmaier in medium and large-job markets as well – especially for special-purpose labels.
Microexplosions
In order to operate with such precision, however, a laser die-cutting machine depends on the input materials – label materials, release liners and adhesive layers – complying with very small tolerances. Unlike a physical die-cutter, which exerts pressure on and displaces the adhesive until a defined stop point is reached, the laser generates an exactly metered amount of energy. Every second, the laser triggers as many as 50,000 microexplosions. In other words, it does not actually produce a cut, as those who are unfamiliar with the technology often assume. Instead, it blasts away or literally pulverizes the material. ‘We therefore have to adjust the laser to deliver the exact amount of energy required to blast away both the substrate and the adhesive layer,’ explains Hagmaier. If the explosive force is too great, the release liner is pierced, and if it is too slight, the adhesive is not entirely removed. Although the release liner and label material can generally be manufactured very precisely, with a consistent thickness, continues Hagmaier, ‘The adhesive presented us with a major challenge. Guaranteed tolerances are regularly around plus/minus three grams per square meter. This may sound like a small amount but, in view of the quantities of adhesive that are usually applied, such tolerances can give rise to variances of as much as 15 percent, which is beyond the bounds of precision required by the laser.
A question of tolerances
Hagmaier set out to find an adhesive material that was produced with especially high precision. After undertaking extensive trials with a variety of materials, the company decided in favor of Herma’s products. ‘For standard adhesives, Herma guarantees tolerances of just one and a half grams per square meter, which enables us to achieve outstanding cutting results,’ comments Werner Hagmaier. The low tolerances are beneficial elsewhere in the production chain too as a general rule, not only in connection with laser die-cutting. Two or three grams too little adhesive can have unpleasant consequences in the case of critical applications in particular. Labels applied to difficult, rough surfaces, for example, can fall off in some circumstances. If two to three grams too much adhesive is applied, on the other hand, difficulties can arise even with mechanical die-cutting, and with dispensing. Adhesive can escape and contaminate the tools or trigger unscheduled stops in the labeling systems. A consistent adhesive coating benefits print reliability as well. A lack
of consistency can be detrimental to print quality.
The key to delivering these tolerances is Herma’s long experience in curtain coating technology, says managing director Dr. Thomas Baumgärtner: ‘Curtain coating enables us to apply extremely consistent coats. A discernible transverse section, consisting of peaks and valleys of adhesive, no longer exists.’ As previously reported in L&L, Herma is now capable of using the technology to apply two different layers of adhesive simultaneously on an industrial scale, typically in order to achieve specific product characteristics.
Choosing inkjet
The next goal was to accomplish contactless die-cutting and printing – including on heat-sensitive thermal paper. This ruled out heat-producing printing processes that rely on toner. A high-performance inkjet printer with 100 percent LED UV curing appeared to be the answer. Eventually, CSAT, a German specialist manufacturer of industrial digital print.ing machines, – now owned by Heidelberg – built a machine capable of achieving the company's goal. According to Hagmaier, it was the first time that CSAT had ventured into the labels segment. ‘We reach a web speed of around 50 meters a minute,’ reports Hagmaier. Measured against conventional UV curing, LED UV curing reduces energy consumption by 90 percent. It allows thermal paper to be printed cold and gives rise to brilliant color quality without requiring the application of any lacquer or other finish, according to Werner Hagmaier.
Print sequence
A significant factor in the success of the Hagmaier contactless operation is cutting the labels before they are printed. Explains Werner Hagmaier: ‘the variation of the traditional sequence "printing - die-cutting" to "die-cutting - printing" means we can produce medium print runs of up to 10,000 meters more cost-effectively than with conventional presses. Furthermore, there is a technical reason. During the production of full surface printed labels this sequence avoids fine white edge lines. They are a consequence of the angle the laser hits the substrate. Because the laser hits the substrate at an angle the removed ink leaves a fine line at the cutting edge.’
Pictured: ‘We must define the energy of the laser exactly, which is why consistently coated adhesive material is so important for us’ – Werner Hagmaier (right) talking to Herma account manager Klaus Keller against the backdrop of the Cartes laser die-cutting machine
This article was published in L&L Issue 5, 2011
Stay up to date
Subscribe to the free Label News newsletter and receive the latest content every week. We'll never share your email address.