DuPont targets labels with round sleeve technology
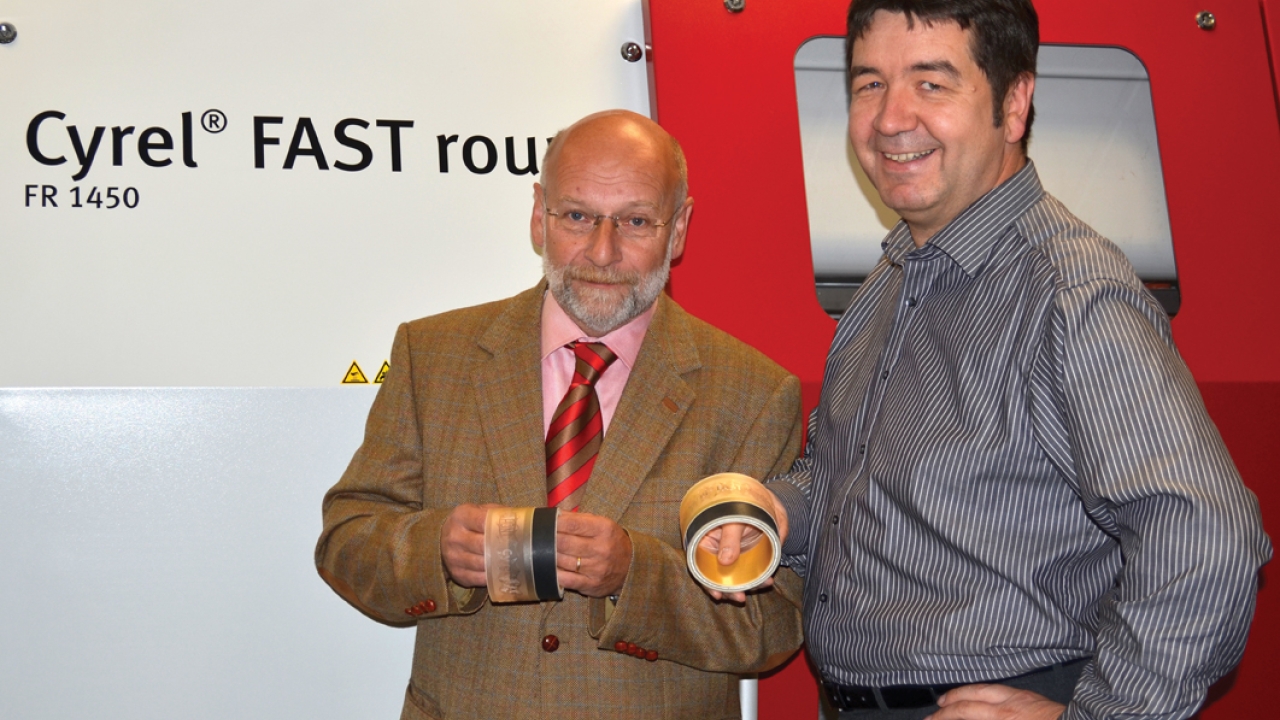
Although commonly regarded as a wide web format, DuPont Cyrel is now targeting its round sleeve technology at narrow web label and packaging converters
The CDI Round system uses either plates pre-mounted onto the sleeve before imaging, or sleeve material which can be imaged directly. After imaging, on the DuPont Cyrel Digital Imager (CDI) the sleeves are processed ‘in-the-round’.
The maximum sleeve length on the CDI Round imaging unit is 1.45m, and a dedicated tool allows this to be cut into multiple lengths. It can image both plates and conventional sleeves, and changeover between the two is a matter of minutes, simply a question of changing the clamping mechanism. A 6-color job can be imaged in one and a half hours. ‘These machines will make more sense being next to the press for rapid remakes,’ says Jan Scharfenberg, Cyrel FAST product manager, EMEA. Scharfenberg says in the future these will be matched with FAST in-the-round thermal sleeve processors, significantly speeding up platemaking times and eliminating chemicals from the sleeve development process.
Rising demand
Andreas Segelken, CEO at leading German pre-press service provider Bremer Carl Ostermann Erben (COE), says he is seeing a major trend towards in-the-round processed sleeves: ‘Our customers are increasingly asking for sleeves. The higher print quality and quick job changes in the flexo printing machine save the company money previously spent on machine set-up and change-over. With increasingly shorter runs, but an increasing number of orders, this can bring a distinct market advantage.’
Segelken notes that the direct imaging of sleeves ‘reduces the risk of registration problems and color variations in the grid area to zero. This advantage has been crucial in convincing many of our customers due to the increasing demands on quality and the trend towards even finer grids in flexo.’
Certainly there is a clear trend towards the use of sleeves by the major narrow web press manufacturers, for the reasons Segelken outlines above – sleeves reduce press setup time and eliminate fitting work and enable the press to be ready for production within a few rotations. Significantly improved registration accuracy over manually mounted plates can reduce material waste by anything up to 10 percent, according to Gerald Rettberg, one of DuPont’s Tag and Label specialists.
A key advantage of round sleeve technology is the reduction in the number of printing cylinders and adapters found in a conventional plate mounting operation. Rettberg notes that using the Cyrel round sleeve process, only one adapter is required for several sleeve sizes (repeats). ‘If there are approximately 96 classes of pitch in a pitch system, then the printer needs only about a third of the number of adapters. If the printer uses, for instance, pitches between 120 and 128, then he needs just three adapters for the nine pitch classes. This simplifies handling and reduces inventory costs.’
In-the-round sleeves do not require the printing plate to be pre-distorted, so the compensation factor can be omitted at the pre-press stage. A flat-lying flexographic printing plate lengthens during mounting to a printing cylinder, meaning the image must be corrected in pre-press. With sleeves, the round surface is imaged directly, which ensures that a correct representation of the actual image, with correct dimensioning, is achieved.
DuPont also says that sleeves can have a longer life than conventional plates. ‘Not only can they be mounted and de-mounted a virtually limitless number of times, but the elimination of mounting tape and the uniform surface of the adapter mean that lower impression weight is required and this makes a significant contribution to the useful life of the round printform,’ says Stephan Riechert of DuPont’s tag and label team.
Picture: Gerald Rettberg and Stephan Riechert, DuPont’s tag and label specialists
This article was published in L&L issue 1, 2012
Stay up to date
Subscribe to the free Label News newsletter and receive the latest content every week. We'll never share your email address.