Labelexpo Americas Technology Workshop
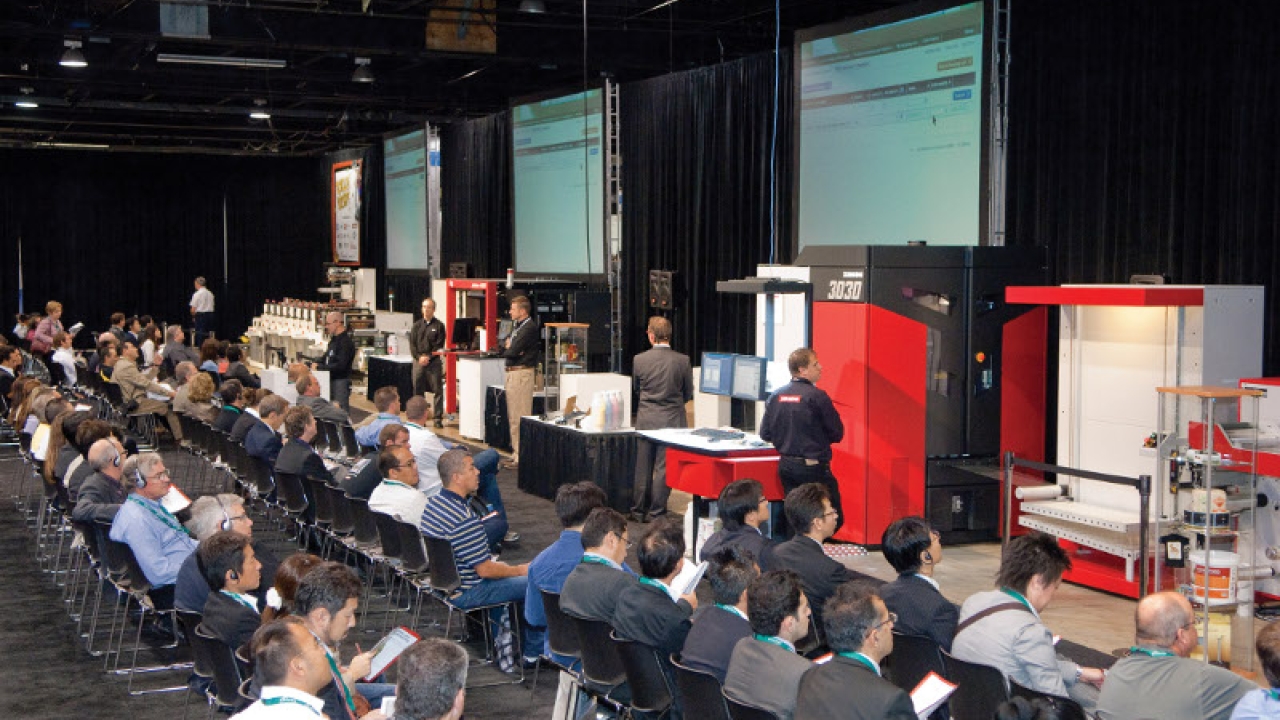
Jan De Roeck, EskoArtwork’s director solutions management, looks at the lessons learned from the Technology Workshops held for the first time at Labelexpo Americas in Chicago last September – and likely to be repeated this year in Brussels
Anyone who went to Labelexpo Americas was probably impressed with the Technology Workshops. Demonstrations were extremely well attended. Four working presses from Nilpeter (flexo), EFI Jetrion (inkjet), HP (liquid toner) and Xeikon (dry toner) ran alongside each other with a neutral moderator demonstrating how each press produced the same job on identical substrates. Without a doubt, the workshops provided an extraordinary forum to exhibit the quality and speed of each press. The sheer investment of vendor time – and resources – should be commended.
The aim of the workshop was to show attendees how to set up and run label presses, whether conventional or digital, to optimize label print performance and quality. It was also intended to teach how to assess new product and market opportunities, and to compare print quality and performance across different conventional and digital printing processes. EskoArtwork pre-press systems delivered the files to each press, and in some cases drove them, which gave us a unique perspective on the project.
The idea of a workshop came from Mike Fairley, whom we consider the ‘guru of labels’. He tested the idea with press vendors and asked us to develop the artwork for three benchmark labels.
MIS: critical for digital printing
While there is a significant demand for pre-press systems for digital presses, the pre-press workflow that was utilized for the Technology Workshop was pretty classic and, apart from trapping for the flexo press, automated. The challenge was automatically delivering the right file, of sufficient quality, along with correct color. The rules that dictate printing on a traditional press versus a digital printer are not quite as clear as just label quantity. It’s also the cost of the press, the number of colors, and the availability of the presses, among other parameters. However, with digital presses typically delivering jobs of smaller quantities, the challenge is not to have a customer service rep spend as much time on a 2,000-unit job as for one of 20,000 labels.
Most of our customers have conventional flexo and more than one digital press. While management information systems (MIS) are relevant for every flexo packaging run, it is more critical for digital presses, putting more pressure on order management systems and pre-press. That’s why our best advocates for more automation are among digital print companies. Integrating MIS can create a supercharged automation system, sharing workflow data and automatically driving pre-press. That’s why we decided, early on, to talk with MIS/ERP providers.
A few months before the event, we organized ideas with two MIS providers. We decided it would be best if we could look ‘like real’, starting with the MIS system, where every job begins. This meant demonstrating an integrated system that could deliver automatic file and data delivery from the MIS to pre-press. When a third MIS provider joined the group, it was more important to focus presentations on the automation between the MIS and pre-press, rather than the systems themselves. While making the labels is an important topic, we decided to look at the entire system rather than age-old topics of preflighting, trapping, color management, and step & repeat.
From EskoArtwork’s perspective, our digital front end automates the pre-press workflow. If it’s a new label, there may be some human intervention. If it’s a re-run, the MIS will tell the production software to find the existing label, make sure it still works, perform a quick step & repeat, and print the job.
Mike Fairley comments, ‘There were two real areas of work – agreeing on the pre-press files, and formulating the integration of workflow management and MIS systems. It turned into a real challenge.’
A press choice for everyone
One of the major objectives of the Technology Workshop was the comparison of printing done by a flexo press (with plates imaged using EskoArtwork’s HD Flexo), an inkjet press, a dry toner press, and a liquid toner press.
To be fair to every press vendor, three different label designs were created – all with intricate designs, and all relevant to real world jobs. A food label had a large image with soft tints and highlights. A shampoo label had a number of tints and vignettes, all starting with a zero dot. A pharmaceutical label had two spot colors, which were reproduced as CMYK builds. There was no different file preparation between the standard flexo and digital presses – for example, the tonal range.
‘I drew up the concept specifications,’ says Mike Fairley. ‘I wanted CMYK as a minimum plus a brand color and a mixture of text, solids and halftone images spread across the labels. For example, the personal care design was developed on transparent material so we could utilize white.’
The entire process was created with the expectation that there would be a color match between each of the presses. Each press vendor received files and an inkjet proof so they knew their color targets based on the ISO 12647 standard, pretty close to GRACoL. Of course, there are different tolerance expectations. How much ∆E is acceptable to a print buyer or provider?
At the workshops, there were differences, perhaps because press manufacturers sped up their presses to impress the crowd. Maybe the color controls were not quite in place at the events. But there is just so much reality that can be expected during a 60-minute demo. Yet, very few attendees took their samples and visited the reception desk to compare the target proofs to the printed results.
Mike Fairley concluded, ‘With all of the variables, and the rush to prepare the Workshops, the printed pieces still looked pretty close. Clearly, we could have worked longer. However, we were constantly coming up against issues. We were working not with one company, but ten. Given the real challenge, it was a success.’
HD Flexo: Matching flexo to digital
As an EskoArtwork representative, I would be remiss if I did not add a few comments about the use of our HD Flexo plates, produced very nicely by Phototype, on the Nilpeter press and how the press performed compared to the digital presses.
‘HD was somewhat unique to compare with digital. Nilpeter wanted to be involved, and EskoArtwork was happy to provide HD Flexo plates,’ explains Fairley. ‘The only real challenge of HD Flexo was that for each demonstration, the flexo press had to get up to speed. However, the results were quite impressive. They looked very similar to the untrained eye. It was only when you looked under a glass that you saw the weaknesses and challenges of each.’
We did not create any of the label designs to compensate for flexo inadequacies. On the contrary, HD Flexo was able to match any of the digital presses. The tonal range was most interesting. The actual file and printed job had the same 0-100 range. With the same tonal range of digital presses, flexo color matching was similar. There were no highlight blowouts, and the shadows, with Microcell screening technology, provided solid ink density in the shadows. This means that for brand owners, both digital and flexo are able to deliver the shelf impact they require, with bright solids, and a complete 256-level tonal range.
Thus, the question is not which process is better but, rather, comes down to understanding the differences of each process, and when and how each one is used. It also allows an MIS system to make a judgment as to which press to send a job based upon business requirements; not quality differences. There is no tonal conversion or other color process that might limit press decisions.
What happens next?
If nothing else, the Labelexpo Technology Workshop was an interesting learning exercise. ‘All the press, pre-press and MIS vendors, not to mention the substrate manufacturers, have all learned something from the project. And, from the packed out attendance, even at the last demo, the converters and printers seemed to benefit,’ observes Fairley. ‘We all broadened our knowledge of a standardized process as compared to offset or flexo. We are looking at the possibility of repeating the experiment at Brussels next year. Lessons from the Chicago Workshop will make the next Workshop even better.’
Given the rush to establish links to the pre-press system and the presses – as short as three weeks for one MIS vendor – it is quite extraordinary how much was done.
What might we do next time? We set a limit of five minutes for the presentations before each of the presses were demonstrated. Unfortunately, that is too little time to get serious about discussing MIS/pre-press integration. Ten minutes might still be short, but provides an opportunity to cover more ground. In particular, we believe that the process, starting with a web-to-print demonstration, might be interesting. It would be helpful to see how a job progresses from a web site, uploading a file and data, conducting preflighting and pre-press, and sending the job to the press.
From a label design perspective, the Technology Workshop will likely continue to stick to process inks or re-separate spot colors, yet color matching should be put more in the spotlight. Some digital presses may be limited to CMYK, and we do not want to give other presses an unfair advantage. It is smart to stay with process CMYK designs because most printing companies prefer to keep the differences between files and presses to a minimum. Designs were developed for the lowest common denominator – a real world consideration when you’re trying to match presses.
Stay tuned for the next Technology Workshop. This is an ambitious project, reflecting real world challenges, and it will only get better.
Pictured: Technology workshops in action
Click here for more stories about Labelexpo Americas on L&L.com.
Stay up to date
Subscribe to the free Label News newsletter and receive the latest content every week. We'll never share your email address.