Innovation brings APE a decisive edge
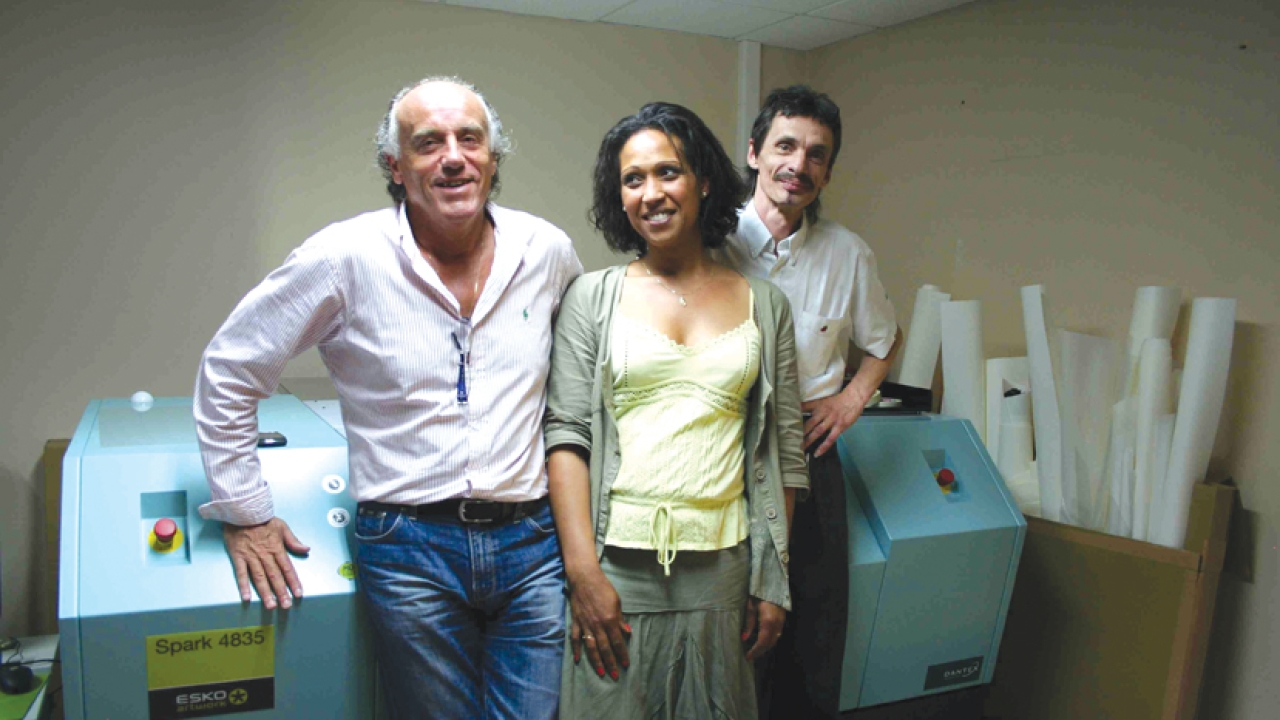
APE Etiquettes has adopted a digital water wash platemaking system supplied by Dantex as part of a major investment in machinery and manufacturing plant. Andy Thomas reports
Located in stunning countryside near Poitiers in south west France, APE Etiquettes is a company with 135 employees, running 80 print units converting over 14 million sqm of materials a year. Turnover has grown from 12 million euros in 2000 to 17m euros today.
APE was founded in 1974, when the company’s current owner, Christian Poirault was running a large format screen printing business. ‘I sold that business in 1998 and the guy who ran APE was retiring. So I was in the right place at the right time and bought APE in 1999. Since then we have doubled the number of employees.’
Christian Poirault is an extraordinary character, animated by a passion for extreme sports. He has driven regularly in the tough Dakar rally in a car sponsored by leading industry suppliers including Dantex and Nilpeter. Poirault’s intense interest in sporting excellence extends to his factory. When a new press is commissioned it is named after a champion sportsman or woman, and they are invited to a ceremony inaugurating the machine along with hundreds of guests. In addition, APE actively sponsors local cycling and soccer clubs.
APE services a wide range of end user markets, with food being the most important, followed by lubricants and automobile products, pharma, cosmetics and household cleaning products.
Almost 90 percent of APE’s production is PS labels, using equal amounts of paper and film face stocks. The remainder is wraparound films for food products like cheese, as well as a little folding carton work.
‘The French market has become a lot more competitive, particularly now we have converters from Spain coming here after business,’ asserts Christian Poirault.
But there are also more positive trends. ‘Between five to seven years ago we were worried our business would go to Eastern Europe. But for our French customers it is easier to come here from Paris to approve a job, and then we export the label to their Eastern European production plants.’
Some 10 percent of APE’s production is for export, mainly to Francophone West and North Africa and to Middle Eastern countries including Iran and Egypt, as well as to Europe and as far afield as Korea.
Production and innovation
APE runs the full range of print production processes including flexo, offset, letterpress, screen and digital. The digital operation is housed in a separate company called G9, and runs a Xeikon and two HP Indigo presses. APE claims to have been the first French converter to install digital presses 15 years ago. Run lengths under 5,000 meters will generally be put on the digital machines.
A key part of APE’s operation is the R&D lab, which drives the company’s innovation projects. APE specializes particularly in promotional and information-intensive labels, including booklet and multi-page labels.
As L&L was visiting the plant, APE was commissioning a highly sophisticated 11-color Nilpeter press, set up with the ability to produce, in-line, multi-layer labels with up to six pages. The FA4 press is configured with two unwinds, 11 UV-flexo heads, turner bar, de-lam and re-lam, crossover, two movable un-/re-wind towers on rails, a special dual web lamination cassette, automatic matrix removal and slitting. It is designed to run at 100 m/min with the multi-layer label process in operation.
‘This is an important innovation for many industry sectors,’ says Christian Poirault. ‘The Total (oil) label, as an example, has three layers and 27 languages. Before we had to produce that label in two passes – now we can produce it in one.’
The new Nilpeter press is the first machine is a brand new production hall. ‘The new building not only increases our capacity, but is a matter of customer faith,’ says Christian Poirault. ‘Customers require the security of having this two factory capacity with back up machines.’
Water wash CTP
APE has just finished installing a water wash digital flexo and letterpress platemaking system. All the equipment, along with support and training, was supplied by Dantex through its French general manager Marc Fiadino. The installation consists of a Dantex branded Esko Spark 4835 imager and an AquaFlex AQF 900FD digital in-line processor. The 900FD includes a LAM removal module and is specifically designed to work with the Aquaflex Optima LAM plates used by APE.
Why move to digital platemaking – and why specifically to a water wash plate system? Explains Christian Poirault: ‘Film suppliers are disappearing and this was a chance to reduce our use of chemicals. But the key benefits are quality and flexibility. Many of our customers come to the plant to sign jobs off, and if anything needs to be changed we can remake the plates very quickly.’
The digital flexo project is led by APE’s pre-press manager Pascal Coullouette, an 11-year company veteran. The switchover is planned to take just 2-3 months, although implementing the full workflow – including Esko Web Center – is expected to take up to a year.
Coullouette had never before worked with CTP, but found the move from analog surprisingly easy. ‘To train an operator to make analogue plates would take 3-4 months, but with the CTP and support from Dantex it was only 3-4 weeks.’
Before coming to work at APE, Coullouette did not have any experience working with water wash plates and was of the opinion they were of lower quality than solvent.
But Coullouette now says that the combination of the Spark imager and Dantex’s new water wash digital plates has been a revelation. ‘With analogue plates we were achieving a 1.6 percent dot, but with the Spark and Optima Aquaflex plate we hold a 0.6 percent dot at 175lpi.’
Coullouette says it is easier to manipulate the compensation curve on the digital compared to analogue plate. ‘Previously, we needed a bump curve, but with the Optima digital plate you do not. It is truly a WYSISYG. The 0.6 percent dot is printable and stable. And this reduces downtime on the press, making it easier to get into registration.’
A key advantage of water-based plate processing compared to solvents is the reduction in drying time. ‘We can have a plate from box to press-ready in just 40 minutes,’ says Coullouette. ‘The plate is dry within five minutes.’
The Aquaflex Optima plates are compatible with water, UV and solvent-based inks and can be stored for long periods without degradation. For some customers APE is using two year old plates for repeat work. To achieve high efficiency in plate archiving, a Dantex plate washer was also included in the package of equipment supplied by Dantex.
Water wash plates are certainly more expensive than solvent, but Coulloutette says the total cost of ownership is less, and there are additional sustainability benefits. For example there is no requirement for special air conditioning or ducting. All processing chemicals are eliminated, and the only waste product is the occasional removal of solid polymer waste.
Coullouette adds that the transition to water-wash was a one-stop-shop with Dantex. They were able to supply all the necessary equipment for plate making and filtration for the wastewater. ‘This eco-friendly system was attractive to our company and we wanted to continue protecting the environment. Dantex was also able to give us in-depth support in engineering and after sales training.’
Coullouette does not see any advantage in implementing High Definition Flexo. ‘We found there was nothing extraordinary in the print characteristics. With a well calibrated Spark we obtain as good quality and it is more productive without HD.’
Five year plan
Where does APE see itself in five years? ‘We are committed to innovation,’ says Christian Poirault. ‘You can see this from the Nilpeter press we have just installed, which is the first of this configuration in Europe. Digital will become more important but there will remain areas which digital cannot service – for example our new multi-label products. To just produce ordinary, everyday labels you must kill yourself to make them.’
Pictured: (L-R) Christian Poirault, managing director APE, Magali Bécot, head pre-press operator and Pascal Coullouette, pre-press manager
This article was published in L&L issue 5, 2012
Stay up to date
Subscribe to the free Label News newsletter and receive the latest content every week. We'll never share your email address.