Eurolabel adds Martin package to Nuova Gidue press
Italian label printer Eurolabel has installed a package of Martin Automatic equipment on its 380mm Nuova Gidue Xpannd press.
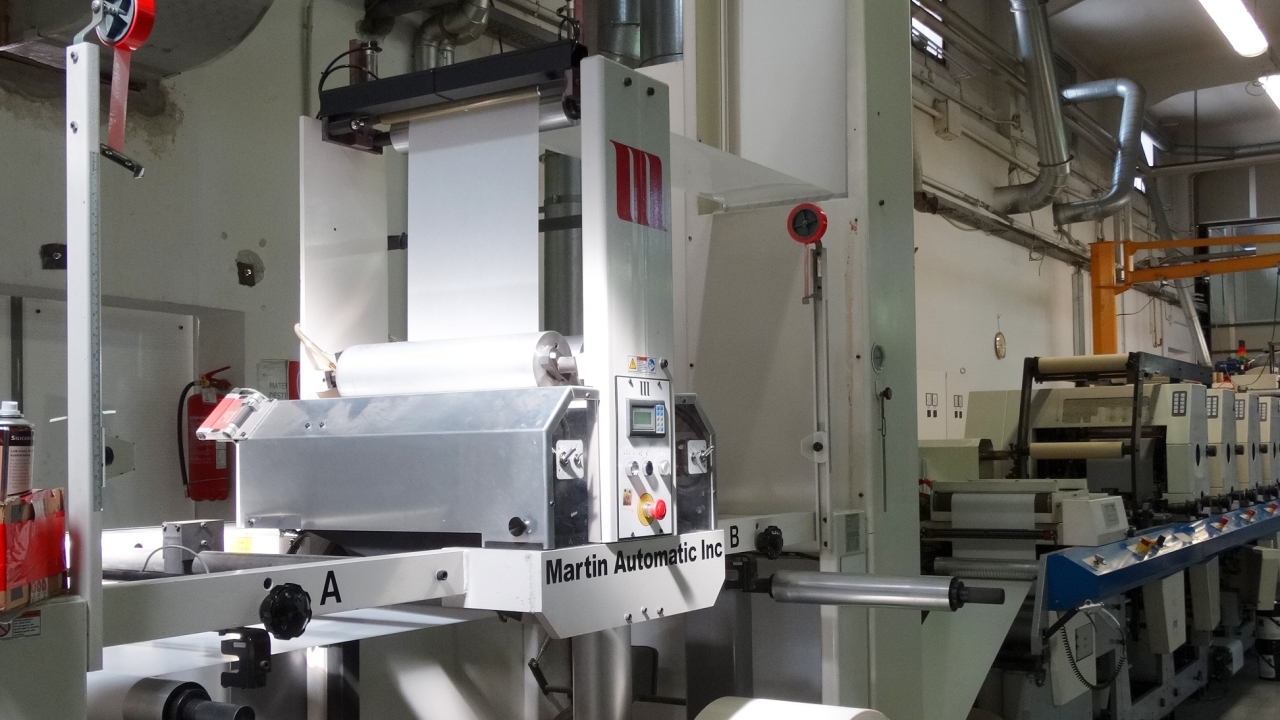
Eurolabel already has a package of Martin Automatic equipment installed on an MPS press that was installed in 2008. The MPS press is an eight-color flexo/screen/hot foil combination line, used largely to run clear-on-clear “no-label look” work on expensive substrates.
It also prints using an HP Indigo WS6000 digital press, Gallus R200B letterpress machines, a Comco Captain and two Arsomas, in addition to a full suite of Arpeco, Prati and AB Graphic finishing equipment.
The Martin MBS automatic unwind/splice and LRD rewind on the Nuova Gidue Xpannd is identical to those fitted to Eurolabel’s 410mm MPS line, and enable continuous running of both presses that are producing high-value labels on expensive substrates.
The Nuova Gidue press, with its narrower 380mm web width, offers Eurolabel a higher degree of flexible production. Fitted with five offset print stations and four flexo, the press can be converted to run with two screen units and hot foil. Dedicated to high-end labels mostly for the cosmetic and beauty product markets, it is fitted with 100 percent inspection technology.
Eurolabel general manager Aldo Franco said: ‘The Italian label market has been flat since the global crisis of 2008 so we have taken the decision to invest in flexible capacity to give us opportunities for growth.
‘We can handle short and long run work, from simple blank labels to complex RFID technology work, which strengthens our hand in what is a very competitive market place.’
Franco added: ‘With certain substrates we can run only 2,000m rolls, so have to change every 30 minutes or so. Done manually, it takes around four minutes and wastes 100m of material each change, besides the time taken to stop the machine and ramp it back up to commercial production.
‘With the Martin equipment there are no stoppages and the waste is practically eliminated. So, we save at least two hours a day in time, have cut waste by about a roll and a half each day, and by running the press continuously, can maintain print quality.’
Stay up to date
Subscribe to the free Label News newsletter and receive the latest content every week. We'll never share your email address.