Polish label specialist installs Esko automation engine
Polish packaging specialist Natalii has refocused its print production process to better manage fast turnaround short run work with Automation Engine and Equinox from Esko.
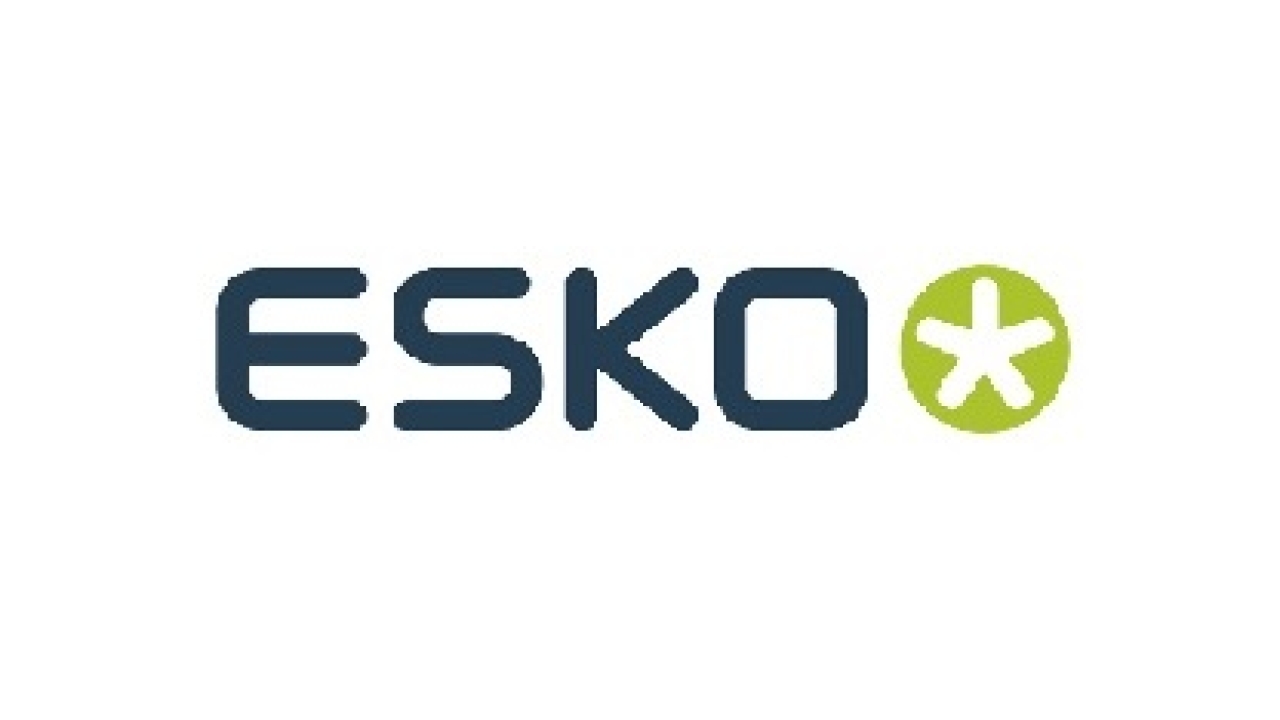
Established in 1985, the label specialist was the first in Eastern Europe to launch the in-mold label printing on polypropylene film for plastic package molding. It was also the first Polish label converter to invest in HD Flexo from Esko.
Tomasz Fiebich, production coordinator said, ‘We are committed to upgrading technology and continuous development of equipment. This ensures we are a reliable partner for any printing requirement and a strong market player despite stiff competition.’
Today, Natalii works with a number of large businesses, including food processing, chemical, cosmetic, automotive, pharmaceutical, and paper processing plants.
‘The market trend is for shorter runs, high quality print and tighter margins,’ Fiebich said. ‘We needed to innovate our label manufacturing process to enable us to achieve the same quality in our digital and flexo processes.’
The answer was Equinox to deliver the quality required and Automation Engine to streamline the process. Fiebich said: ‘We wanted to be the first to deliver higher quality, a better look for customers, and at the same time lower costs. We invested in a new proofer to print in Equinox and for the first time the proof is consistent with the print. The process is more stable.’
He continued: “Standardization of the prepress process translates into faster make-readies and now we can print most jobs in up to seven colors. Besides cost reductions, we now get more jobs printed with the extended gamut and have also achieved a quality match of digital print with flexo. We now run about 60 percent of new jobs on Equinox.’
The investment has also had a positive impact on production times: ‘Because you don’t have to clean the anilox rollers, set up is much faster,’ Fiebich said. ‘It used to be couple of hours to make ready, now it’s 15 minutes. It’s hard to imagine how we worked before.’
Stay up to date
Subscribe to the free Label News newsletter and receive the latest content every week. We'll never share your email address.