Signature Flexible Packaging takes second KBA-Flexotecnica EvoXD
US firm Signature Flexible Packaging is to take delivery of its second KBA-Flexotecnica EvoXD CI flexo press shortly as it seeks to match its recent growth and need for extra capacity.
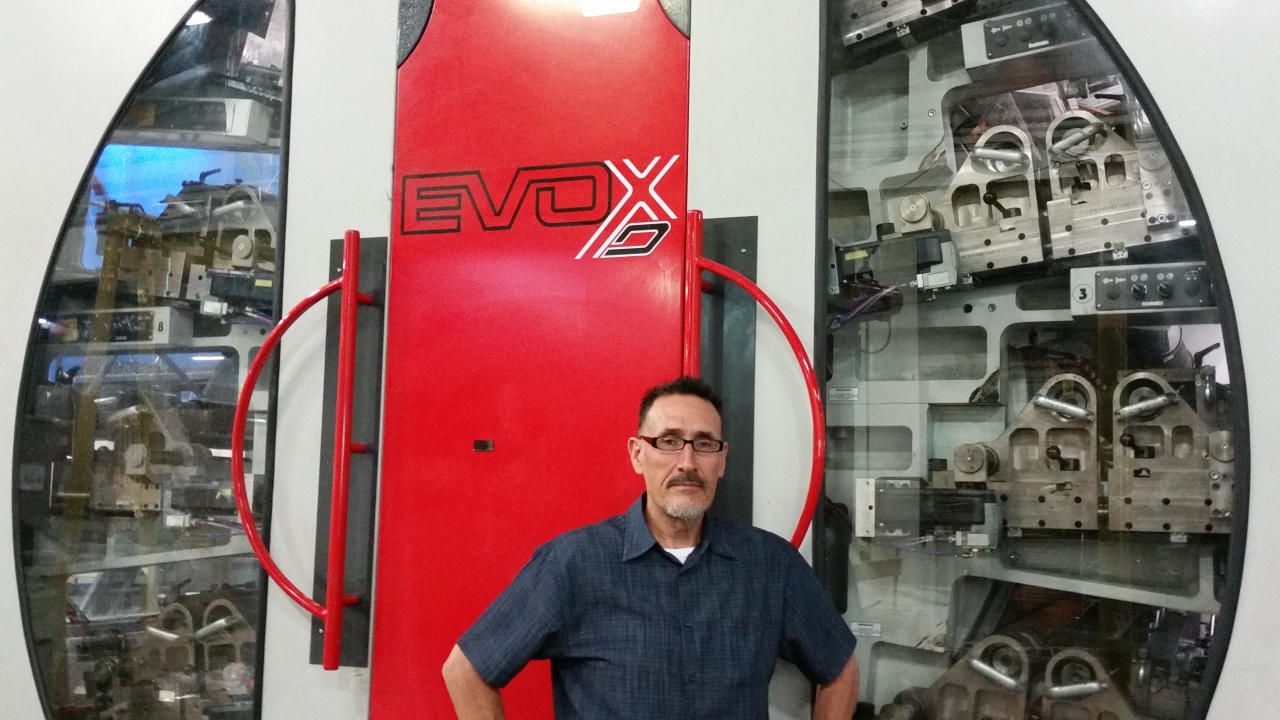
The 10-color gearless, sleeved CI flexo press will be installed at one of the flexible packaging producer’s facilities in the Los Angeles area this spring.
Adrian Backer, Signature Flexible Packaging president, said: ‘Our first KBA-Flexotecnica EvoXD press has been running very reliably since we installed it in April 2014. It is being used as our principal press for all of our products, but primarily for our high-end process work. Almost from the start, the EvoXD has been producing a clear majority of our printed products. In the last 12 months it has produced 73 percent of our total print production among three presses. It soon became clear that we can’t run our entire product on this one press even though it is more productive than our other presses.
‘So the solution to this dilemma was to order another EvoXD, thus giving our production scheduling some symmetry. We feel that the new incoming EvoXD will nicely work in tandem with the existing EvoXD press.’
Both KBA-Flexotecnica EvoXD 10-color presses at Signature Flexible Packaging feature a raft of new technology, including time-saving components like the Speedy Clean automatic wash-up system and in-line viscosity control with InkSpec viscometers, auto-impression setting, and click-and-drag zero-waste registration along with numerous quality control options, such as a 100 percent inspection camera and in-line color control.
The firm typically prints thin-gauge plastic film such as oriented polypropylene and oriented polyester on its EvoXD press.
Signature Flexible Packaging has opted for a downstream coater and an electron beam curing beam to be installed on the incoming EvoXD press. Having this capability will allow the company to use a mix of traditional inks and EB varnishes.
‘As customers try to differentiate their products in the marketplace, designs become more complex and varied,’ added Backer. ‘One trend we are seeing is customers that require a matte look with a window. So this requires us to reverse print on one side of the film and then print a matte varnish pattern in register on the opposite side. We have an insetter on this press from BST eltromat that allows us to do this. Our first EvoXD was configured with 10 units to give us more options on difficult jobs, and, when running jobs of five colors or less back-to-back to have the cylinders for the second job in press. The second EvoXD is configured the same way to give us maximum flexibility.’
Stay up to date
Subscribe to the free Label News newsletter and receive the latest content every week. We'll never share your email address.