Belgian abbey brewery moves to digitally printed self-adhesive labels
Unique removable self-adhesive labels have been produced digitally by Label’Or on Xeikon presses for Val-Dieu Brewery.
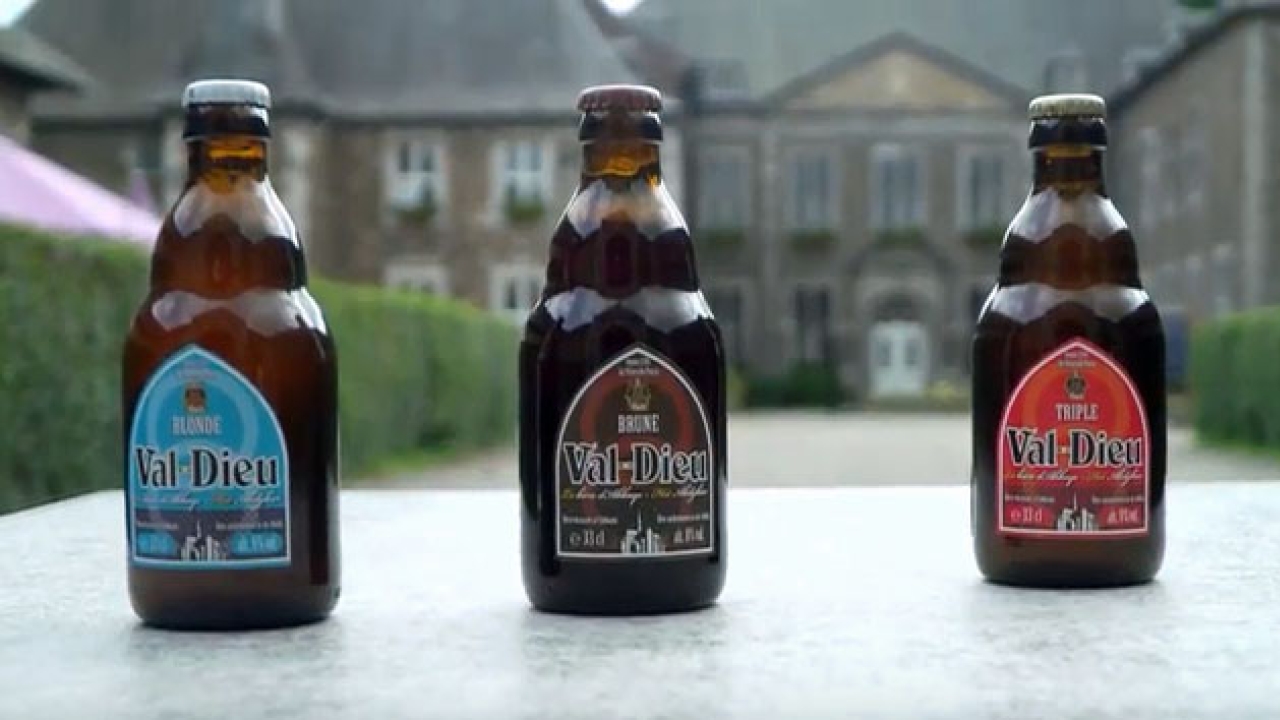
The Belgian abbey brewery had previously used wet-glue labels to decorate its bottles, but has now moved to removable self-adhesive labels. Val-Dieu, the only beer in Belgium still brewed inside an abbey, made the change as it sought to keep up with growing demand for its beers.
‘We needed to change our production process,’ said Alain Pinckaers, director of Val-Dieu Brewery. ‘As part of this, we decided to change the labels on our bottles. Where before we used wet-glue labels, we now switched to self-adhesive labels. As the bottles are washed and re-used, it was vital that the labels are easily removed.’
To achieve this, Val-Dieu worked with Belgian label specialist Label’Or to specify and choose a suitable machine removable label.
Jean-Marie Peters, owner of Label’Or, explained: ‘For the improvement of the production process, we looked at enhancing the brand image and presentation of the bottles. It was also very important to have washable labels, because of the switch to self-adhesive labels. We did a lot of research and testing, also working closely with paper suppliers, and finally found the solution. The rest just comes down to proximity, service, availability and short runs.’
Family-owned Label’Or started working with Xeikon in 2008 when a Xeikon 3300 5-color digital press was installed. A second Xeikon 3300 was added, followed by a Xeikon CX3, on which most of the Val-Dieu labels are produced.
‘Not only do we print four or five different colors, we also add a coating,’ said Peters. ‘Afterwards the large reels, which sometimes carry 2000m of paper, are sent to the roll slitting and rewinding machine, where the labels are cut and wound on reels for the labeling machine.
‘Xeikon’s digital presses allow us to respond adequately to market needs for several reasons. First, because of the outstanding printing quality and secondly because of the dry toner that allows for direct or indirect contact with food. With the short turnaround time and maximum use of the press in one shift, we can react swiftly and offer the client a fast service. And that is what’s expected today: quality and fast delivery.’
Stay up to date
Subscribe to the free Label News newsletter and receive the latest content every week. We'll never share your email address.