Heidelberg intros new Speedmaster presses
Heidelberg has introduced two new large format presses, the Speedmaster XL 145 and XL 162, which are targeted at the large volume package printing markets.
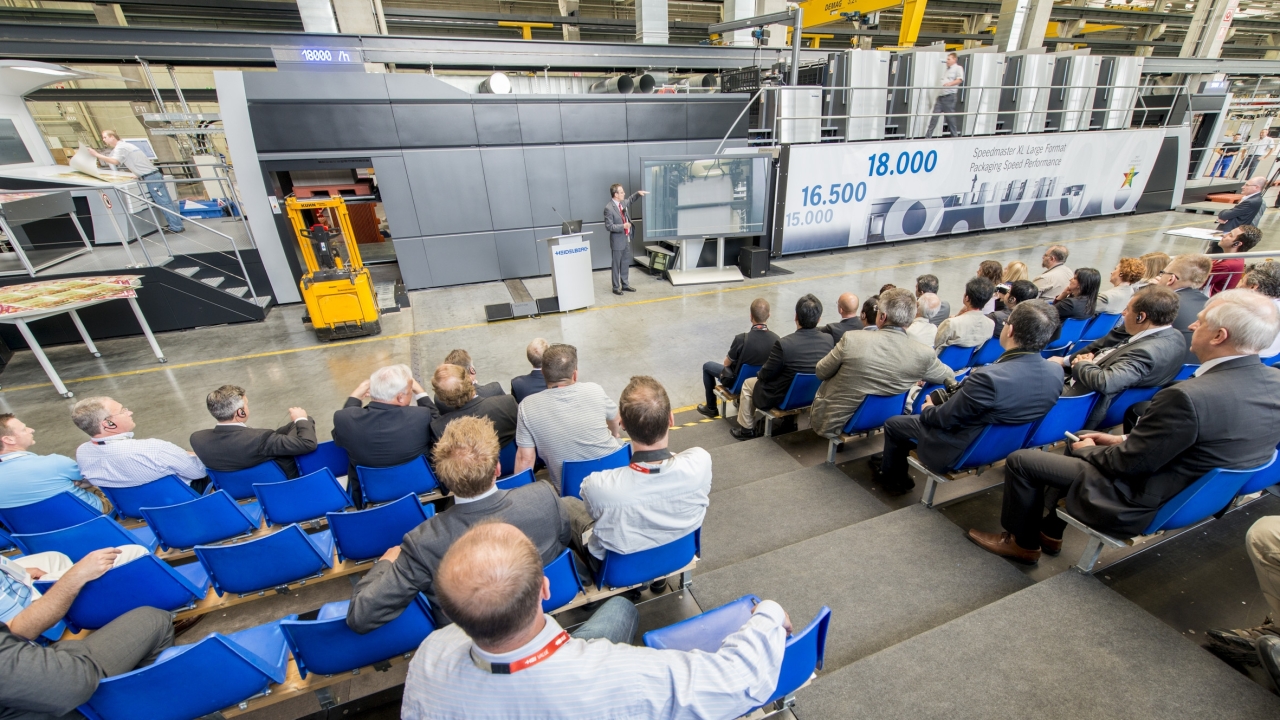
The new Packaging Speed Performance (PSP) speed classes at 16,500sph and 18,000sph are aimed at companies who are active in large volume printing primarily for packaging in the food and non-food sectors.
New and unique features of the PSP presses include a high-speed suction head, optimized sheet travel and a new chain guide in the delivery, coupled with new gripper bars and components such as the high-performance dryers. The delivery's modular structure supports drying sections that are coordinated with the relevant applications.
The Speedmaster XL 145 PSP and XL 162 PSP feature the longest drying sections on the market. They are equipped with seven slide-in units to ensure smooth production and complete drying at maximum speed.
The Speedmaster XL 145 has a top speed of 18,000sph, while the Speedmaster XL 162 can print up to 16,500sph. The Prinect Inpress Control spectrophotometric in-line measuring system aids operators when the press is operating at these speeds, as it controls and monitors color and register accuracy on the fly and ensures stable and reliable production.
Calculations have shown that a Speedmaster XL 145 with PSP working three shifts for six days a week produces twice as many sheets as a packaging press built in 2007 running at a speed of 15,000sph. The Speedmaster XL 145 with PSP can produce 70 million sheets or more each year.
More than 250 customers and folding carton experts from around the world were present at the recent Heidelberg Info Days, held at its Wiesloch-Walldorf site with a focus on peak performance in package printing, for the launch of the new presses.
The target groups for these presses are large, international packaging manufacturers that require maximum productivity with minimal waste for large volume printing.
Heidelberg said that the trend in the printing industry, and particularly in folding carton printing, is moving toward larger formats and ever shorter runs. Examples from the consumer goods industry include products with different model variants, such as smartphones and displays used to promote products at the point of sale.
The Speedmaster XL 145 and XL 162 models feature parallel washing using individual drive technology, synchronized plate changing and the Prinect Inpress Control spectrophotometric in-line measuring system. These components ensure minimal make-ready times with less paper waste.
The OEM added that premium packaging manufacturers, where 80 percent of work is in UV printing, have strict requirements for cost-efficient, green production. Large format machines in particular enable more efficient production thanks to a higher number of repeats. Print quality is a top priority, with the high-performance inking and dampening system of the Speedmaster XL 145/XL 162 ensuring consistent color and print quality throughout the run. Extremely high gloss levels can also be achieved at maximum speed due to dual coating technology and the long drying section, which ensures complete drying/curing of inks and coatings.
There are no limits to the surface finishes available, with the option of matte-gloss effects or combinations of different surface textures, such as metalized silver or gold substrates. Opaque white applications with maximum ink transfer for complete opacity reportedly deliver ‘amazing results’.
Heidelberg further offers an end-to-end workflow covering pre-press, press, and post-press, complete with services, consumables and consulting. For the first time, the Speedmaster XL 145 was shown at the Info Days working alongside the new Dymatrix XL 145 CSB high-performance die cutter. With the new Dyset XL optical feed system, the die cutter provides feed register accuracy and stable sheet travel at maximum speeds. It supports shorter make-ready times and reduced paper waste by preventing misaligned sheets.
Heidelberg noted that it has sold more than 100 large format presses in formats six and seven since the start of series production in 2009. Some 70 percent are used for packaging printing and are to be found across Europe, in the US and throughout Asia. The assembly line in Hall 11 at Wiesloch-Walldorf is running at full capacity until the end of the 2014/15 financial year and is recording the highest volume of orders since the start of series production.
Stay up to date
Subscribe to the free Label News newsletter and receive the latest content every week. We'll never share your email address.