Kocher + Beck unveils ‘intelligent’ nonstop winding system
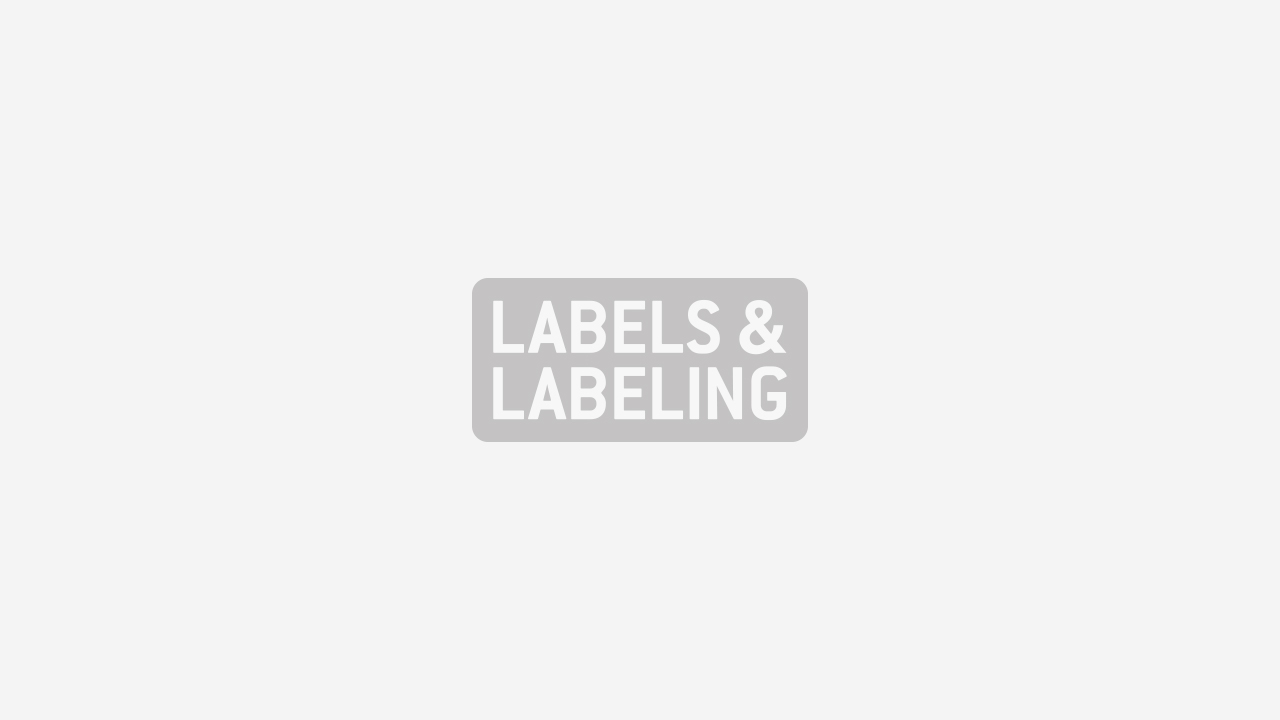
Kocher + Beck has developed an ‘intelligent’ nonstop winding system, UR Precision, which offers features for further optimization by using what the company calls ‘an ultramodern drive concept’. A major aspect of this is an integrated energy regeneration system.
‘Nonstop technology nowadays is no longer just for the typical long print runs within the label and narrow web printing industry, but is also finding a highly sophisticated field of application, primarily within complex process combination printing and value-adding equipment,’ said the company in a statement. ‘Such high end products must guarantee an ideal operating level in 3- and 4-shift models and such equipment must be designed for fast job change over with a minimum of energy, material and labor utilization.
An integrated isolation dancer provides a constant web tension which is unaffected by the splice cycle itself and the moment of inertia caused by the new roll acceleration. The preset web tension always remains constant while being fed to the printing and converting process.
This results in less waste and an improved printing result, says the company, in particular on processing tension sensitive materials.
A scissor cut transfer unit clamps the web instantaneously and cuts it before the actual web transfer happens. The web is then attached to the core with its linear edge. This method leads to a controlled web shift and avoids start-up waste at the core by means of zero fold-back.
Winding print inside or print outside without having to utilize a turn bar unit prior to the winding process is an additional advantage of this transfer method.
Removal of the finished reel does not require floor contact and therefore no contamination of the processed print substrate.
The servo based drive and control system allows for storing and recalling of job related winding parameters, such as web tension values, taper tension characteristics or roll diameters. On repeat orders, all values can be retrieved within seconds. This feature allows customers to avoid additional time and material expense for any re-parameterization.
Likewise, a presetting of new rolls at the loading position of the unwind splicer is carried out by means of an ultrasonic sensor which indicates the web diameter and web tension pre-adjustment to the drive system.
Roll diameter calculation starts straight after the splice cycle via an integrated encoder system. The remaining core waste is precisely defined independently from running speed. The company says that a high degree of process stability plus optimum use of material is guaranteed. Web tension accuracy is provided at all times by keeping the trailing edge attached to the core.
The main energy consumption in a typical label combination print environment is still by far the drying system UV / IR or hot air. Whereas dryer manufacturers are working extremely hard on developing new energy saving solutions, it is incidental that a process chain upgrade through nonstop winders automatically results in an additional saving potential up to 20 percent of the rated electrical power of the dryers.
Even though all well-established lamp systems are equipped with power supply units which are reducing its rated power input in standby mode, the latent consumption factor during process interruption significantly increases the overall energy usage.
Kocher + Beck’s UR Precision winding systems feature servo motors and drives which are triggered through a can bus system connected to an industrial PC. The drives themselves are linked to a regeneration system which avoids costly permanent air pressure as far as possible.
The power created from the motor braking energy at the automatic nonstop splicer is not reconverted into heat, but is mainly (up to 80 percent) supplied to the transfer rewinder in order to save energy and to reduce the impact on resources.
A monitoring phase is taking place at converter X-Label, the results of which will result in further technical development, says the company.
Click here for more stories about Kocher + Beck on L&L.com.
Stay up to date
Subscribe to the free Label News newsletter and receive the latest content every week. We'll never share your email address.