Konica Minolta develops AR glasses for industrial environments
Konica Minolta has developed AIRe Lens, a new wearable augmented reality (AR) technology designed to bring digitalization and AR to the assembly line.
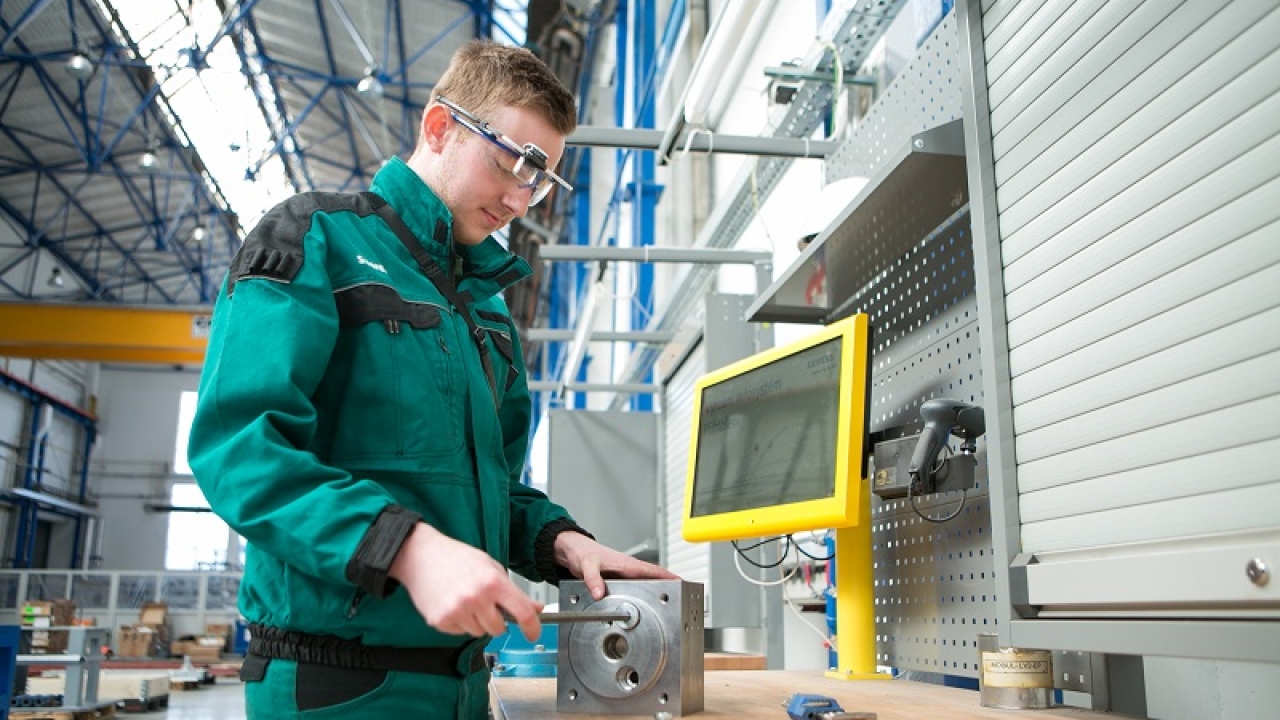
AIRe Lens has been developed specifically for industrial applications. The smart glasses deliver technical information and step-by-step guidance to wearers while maintaining mobility and hands-free production. The technology is designed to guide industry operators step-by-step through work processes, such as assembly, maintenance or quality assurance tasks. It is an optical, head-mounted AR device with a transparent display that can be controlled via simple gestures or the push of a button. Powered by a hot swappable seven-hour battery, AIRe Lens supports a full working shift. The technology is claimed to offer the durability, comfort and high optical quality required for all day use in manufacturing contexts, where precision and safety are paramount.
AIRe Lens is a unique Konica Minolta development. It is a collaborative creation of the company’s own Industrial Optical System Business Headquarters (IOH) in Japan and Konica Minolta’s European Business Innovation Centre (BIC). AIRe Lens has been initially introduced in Germany, Austria and the Czech Republic.
Zdeněk Vrbka, smart glasses program manager within the Konica Minolta BIC, explained: ‘While digitalization is shaping and improving many processes in the industry, it often still stops with the workers at the assembly line. Their work processes are frequently paper-based and therefore inefficient. This has had practical reasons in the past: Workers need their hands free, particularly when assembling complex and bulky machinery.’
Vrbka continued: ‘AIRe Lens is perfectly designed to support workers executing these tasks, streamlining production processes and significantly reducing the costs of training and supervision.’
AIRe Lens has been extensively tested with partners such as Siemens Brno. ‘At the Siemens factory we were able to achieve results that went even beyond the client’s expectations. The time required was reduced by as much as 42 percent and the necessity to have a supervisor overlook the process was reduced by 89 percent,’ stated Vrbka.
Julian Melsbach, project lead for smart glasses at Siemens Brno, said: ‘The feedback from the operators was very positive, not only with regard to the mobility and light weight of this solution, but also concerning the unhindered vision compared to other smart glasses solutions, thanks to the high transparency and position of the lens. Therefore, the device can be very well integrated into the employees PPE, which is why there is no impairment of occupational safety.’
Stay up to date
Subscribe to the free Label News newsletter and receive the latest content every week. We'll never share your email address.