Soma targets short runs with new flexo press
Press design aimed at entry level customers and existing print operations seeking to transfer short-run work from high performance lines
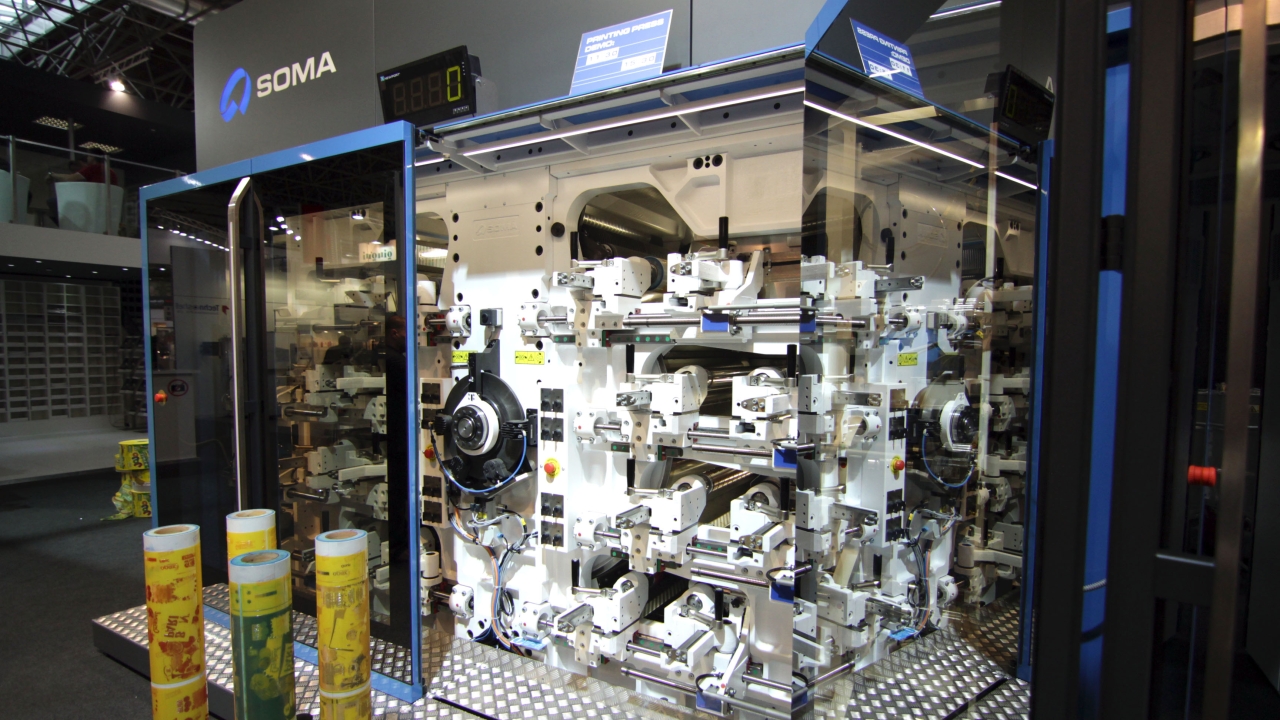
Soma Engineering has launched Optima, a flexo press designed to target short-run print work.
Available in printing widths of 620mm and 820mm, the Optima features a new ergonomic design concept that separates the print area from the material section for improved operator space and efficiency.
The press design is aimed at entry level customers and existing print operations seeking to transfer short-run work from high performance lines. The 620mm wide version is available for customers requiring a machine for test/laboratory purposes, or shrink film label production.
A modular design permits the addition of a full range of options comparable to those available for Soma’s top of the range models for as much or as little automation as required. These can be supplied at the time of purchase or at a later date to meet changes in market demands or production needs.
During the recent K plastics tradeshow, an 820mm-wide Optima was demonstrated in full production mode printing a five-color Bon Pari graphic on 0.20mm thickness BOPP using Kodak Flexcel plates and a 175lpi anilox screen.
A second five-color job was also printed on the same type of substrate that featured a Ricore graphic using DuPont DSP plates and the same specification anilox screen.
Subsequent converting was carried out on Soma’s latest Pluto III slitter rewinder. Both machines were sold off the stand to customers in Russia and Bulgaria.
To this end, Soma also used K to introduce a new version of its Lamiflex laminator. Available in widths from 950mm through to 1,500mm, the new Lamiflex solvent-free laminator offers a robust, entry level machine that resonates with current legislative trends toward the reduction of VOC emissions, the company said.
Designed to process a full range of films, paper and foils, the machine features a side tilting, sleeved transfer roller that permits sleeve changes within the machine. High efficiency material bonding is ensured through a three roll system that presses and forces out air during lamination.
‘We were delighted with the reception of the new Optima and interest exceeded expectations,’ said Pavla Kusa of Soma.
‘Customers perceived the development as filling a gap in the product offering currently available from top of the range press manufacturers.
‘I am also pleased to report on comments made by customers from various countries, for example, one from Malaysia compared the development of the machine with that of a well-known smartphone, the first to offer more functionality and added value than the rest.
‘From Turkey, again the impression was a “smart solution” that fills a gap in the market. A Russian customer was impressed that we were the only company running live jobs and providing samples and one from the USA admired the concept for future expansion in relation to market demands.
‘Finally from Latin America, we again heard the word “smart” and just what I’m looking for in a compact press, big on quality and low on price.’
Kusa added: ‘A high quality of sales leads is now being processed and the equipment can of course be seen at our new SomaGlobe Training and Development Centre.’
Read more about press technology here
Stay up to date
Subscribe to the free Label News newsletter and receive the latest content every week. We'll never share your email address.