Shrink experts step into printing spotlight
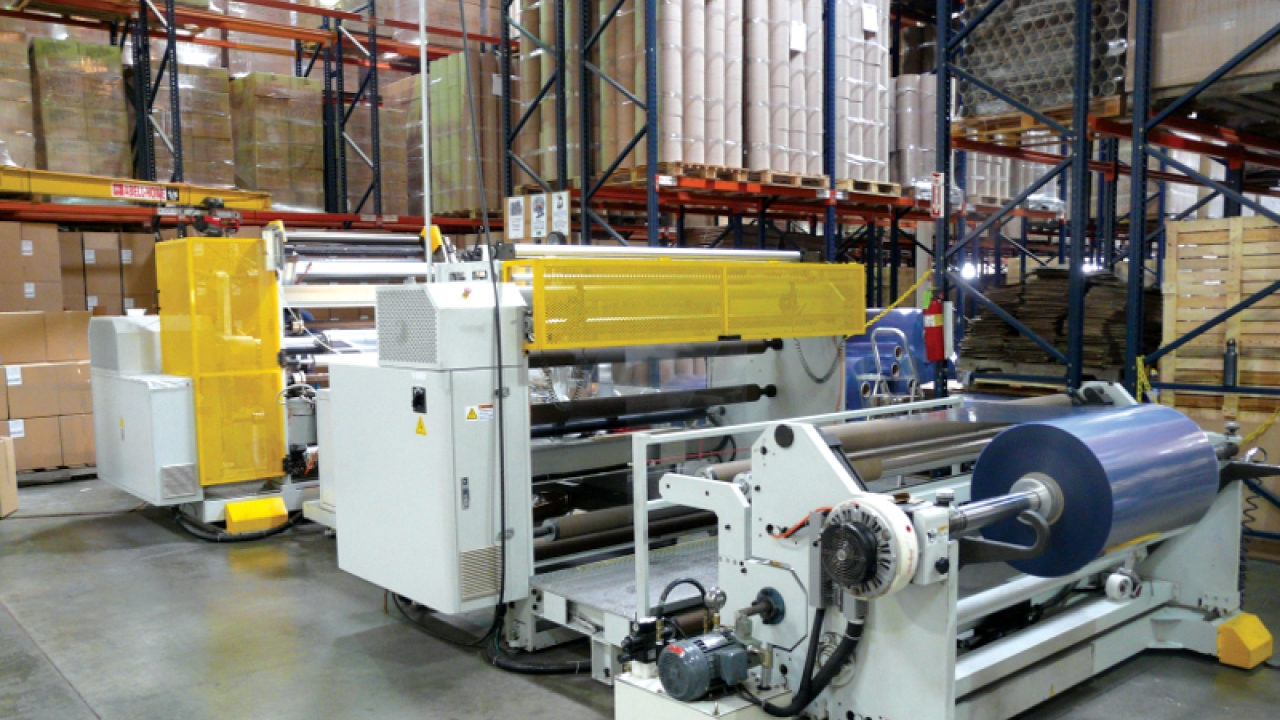
The Dwyer Group has installed an RDP Marathon variable repeat offset press to print shrink sleeve labels. Danielle Jerschefske reports
The 20-year old Dwyer Group, headquartered in Anaheim, California, in the south central suburbs of Los Angeles, has made a significant investment to move into process color offset shrink sleeve label production. Within 12 months the company installed an RDP Marathon IVCO press at its Pennsylvania location and an HP Indigo WS6000 digital press in California.
The Dwyer Group gained its strength in the preform business, supplying tamper evident seals for the bakery and dairy markets. Jim Dwyer, CEO of the Dwyer Group says, ‘Most of the commodity business has evolved into a bigger footprint for items such as party-sized fruit and salad trays with bigger containers, whereas printed shrink sleeves have increased in adoption in pharmaceuticals, dairy, beverage, household products and even pet food containers.’
The company is using the digital press to create prototypes to drive sales for the high volume offset press. Dwyer explains, ‘It came together as a philosophy that falls in line with the general principles of the business. Our whole business model is just-in-time delivery. The prototyping allows us to get our foot in the door to show the quality of the label we can produce, and it increases overall speed-to-market.’
Dwyer and his father joined forces in 1988 to create a packaging brokerage company selling nearly every material that can come on a core – polypropylene, polyester, metalized films, coextrusions, mainly to converters.
The business got involved in packaged salads early on, and introduced preforms to the produce market, most of which was coming from overseas. Dwyer Group found some Asian suppliers, but eventually started producing its own shrink bands when issues with lead times started to rise. Some new and second hand equipment was acquired, a slitting machine, seamers, cutters, and the business grew from there.
It now houses a Karlville 700mm lay flat converter with end fold and glue application, and turret rewinder running at 300m/min. The California location has a total size of 120,000 sq ft, much of which stores the various preforms, and employs two-thirds of the company’s 150 workers.
Dwyer says, ‘We were one of the first to do domestic converting on the commodity [preform] side. We went national by opening distribution sites in Chicago, Texas, Florida – basically a day or two from anywhere on the East Coast, which broke the business open. People back East were having trouble getting preforms in the time frame that they wanted. Just-in-time delivery is hard to manage, expensive and problematic but our customers want stuff when they want it; not when we want to supply it.’
The demand had existed for the materials, but the supply base was rather fragmented with a lot of small suppliers, and no one had made it easy for larger customers to reliably source the materials.
Printing Shrink Sleeve Labels
Dwyer plans to carry this JIT philosophy into the printing side of shrink label production. It partnered with other businesses in the past to offer printing capability to clients but Dwyer says, ‘it didn’t work because of lead times. So we came to a crossroads where we needed to decide what to do.’
The prospect of acquiring Ideal Sleeves in Wilkes Barre, Pennsylvania presented itself as a viable solution to move forward. Equipped with some older flexographic presses there was high potential to get into the printing business with a few equipment upgrades.
Dwyer looked at gravure, but steered away, fully realizing that there would be some trade offs and limitations in selecting another print process. Further research found that only a few other companies in North America are producing shrink sleeves with offset technology. Hence, the decision was made to invest in an RDP Marathon 8-color 38” Infinite Variable Cylinder Offset press.
All water-based, the offset press allows Dwyer to shorten lead times with its quick changeover capability. In combination with digital prototyping as a speed-to-market tool, Dwyer says, ‘we have compressed the time-line to get through the finished process in two to three weeks from concept to consumer. It’s all now possible with the technology.’
The only printing that’s done in California is digital. The HP Indigo has color matching software installed to match the digital print to the offset print. Rather than purchasing a new coating line, costs were reduced by combining a couple of flexo stations in-line to varnish and prime the materials for the digital machine.
‘Medium sized companies are our target customers, but there’s also the possibility to reach larger firms that are producing sleeves using flexography, but want the graphic quality of offset technology. Now, they can upgrade with no extra front and little added total cost.’
Design and layout for shrink sleeves is critical in order to avoid any distortion issues. Dwyer is concentrating on its CSR infrastructure and has implemented strict quality control procedures and processes to eliminate mistakes.
A number of upgrades were made in the finishing department in Pennsylvania including new slitting and seaming machines.
Dwyer Group has experienced a positive response to its new offset capabilities. ‘Potential clients have been eager to hear about offset, and it’s gotten our foot in the door.’
The company has launched a new marketing campaign to build up awareness about its new printing capabilities, including full production work on the digital press. Most sales are contracted through brokers and distributors on the East Coast since most purchasing decisions come from there.
‘Within three years we’d like to bring the same press into our California operations, to have offset capability here,’ explains Dwyer. ‘Then we’d be the only wider web sleeve offset printer within 1500 miles. But for the time being we are going to concentrate on pushing the limits of the technology, helping our customers to be courageous and try doing new things.’
RDP Marathon
RDP Marathon restored its original name in 2009 after being known in the market as Drent Goebel North America since 2006. In October of 2010 Sanden Machine Limited of Ontario, Canada and RDP Marathon Inc in Montreal, Canada formed an alliance to service the label and packaging markets of NAFTA region, including an exclusive distribution agreement with Edelmann Graphics in Beerfelden, Germany for the STAR Print (Sleeve Technology Advanced Rotation).
Sustainability
Dwyer has installed solar panels at its Pennsylvania facility to reduce the manufacturing sites’ pull on the grid. It recycles all pallets, boards and waste products at both locations.
This article was published in L&L issue 2, 2011
Stay up to date
Subscribe to the free Label News newsletter and receive the latest content every week. We'll never share your email address.