Barry Hunt: Trends in conventional and digital press technology
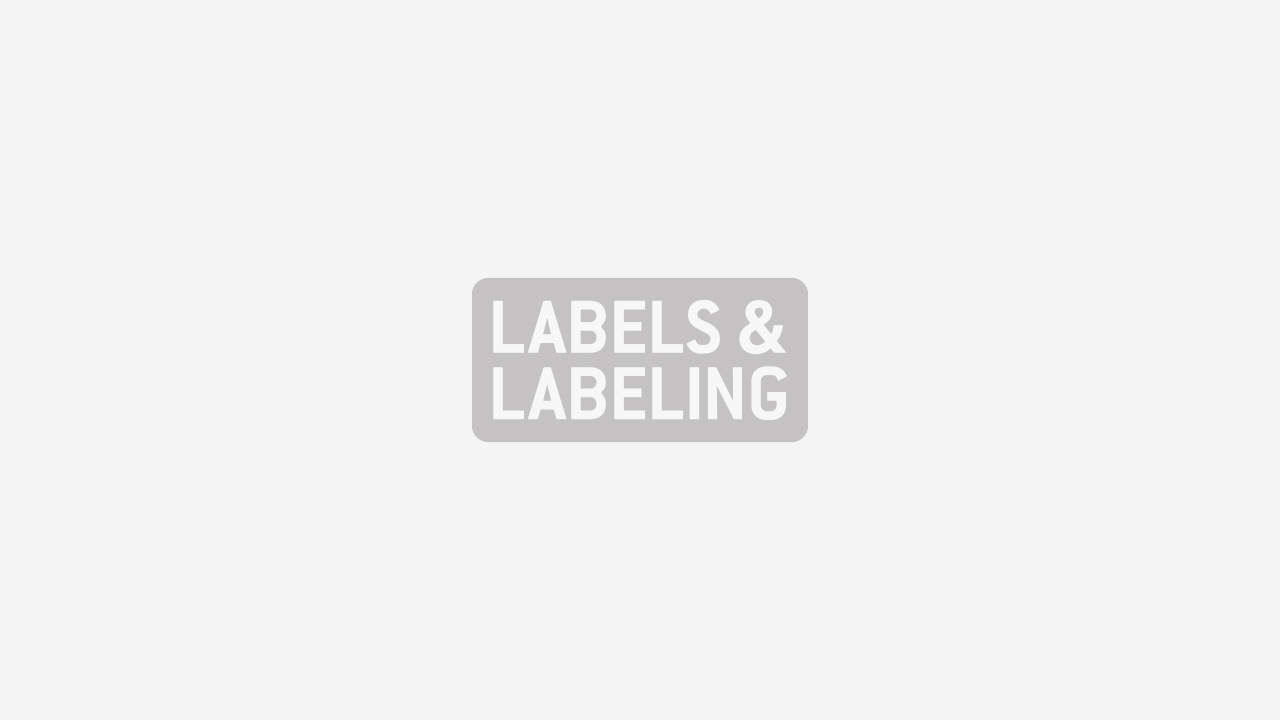
PressConventional and digital narrow web presses accurately reflect trends within the label and flexible packaging markets. The Labelexpo series of events mirror these trends. This year's show was especially useful because of what is happening in the conventional and digital sectors. Besides marking the beginning of a technological circle, the event also showed the robustness of our industry. That's not to say it is immune from the widespread economic gloom, but the industry's general dynamism and all-round optimism leaves it in better shape than any other graphic sector. In fact, many exhibitors – including a large number showing for the first time – gained a creditable number of sales and serious sales enquiries. Some said the show exceeded their expectations. This is reflected by the record-breaking attendance: over 28,600 visitors came from 118 countries. The European debut of the Digital Print Workshops involving liquid ink, dry toner and inkjet printing technologies printing like-for-like jobs proved an added-value attraction. The presence of a Package Printing Zone was another visitor attraction in step with current trends.
By operating within a highly globalized industry, press manufacturers are adapting to shifts in international market shares and the emergence of new production centers. For example, annual growth levels of pressure-sensitive labelstock volumes within much of Europe and North America show a declining trend. It is the emerging markets, especially those in South America, China, India and parts of the Middle East, where the double-digit annual growth is coming from. Established label printers, it is often said, must therefore tailor their production needs to mitigate the continuing volatility of global economies. This means developing new business opportunities in niche markets to reduce a dependency on low margin commodity labels.
Not surprisingly one of the big themes that governs label production is an ability to handle larger volumes of shorter run jobs. It reflects customers' demands for reduced inventories of labels and packaging, especially for products with shorter life-cycles, and is backed by increased needs for versioning. Major brand owners and packaging contractors also seek to reduce the volumes of packaging materials by down-gauging, reducing run lengths and rationalizing their packs. They may also require to be plugged into their suppliers' databases when placing and tracking orders, hence the rise of multi-level management information systems. The huge rise in supermarkets' own-label brands represents another factor in terms paper or filmic substrate choices, issues of sustainability and the creation of eye-catching decorative effects. High standards of color reproduction and color consistency are, of course, a given.
All of these demands place a heavy pressure on converters and press manufacturers alike. The latter strive to develop innovative features that reduce press set-up times and job changeovers. Producing saleable product, with minimal wastage of costly substrates, within a matter of minutes now informs the design and configurations of modern presses. Manufacturers have placed much effort in simplifying printing and die-cutting controls. Operators can far more easily concentrate on maintaining print quality and productivity, often aided by sophisticated inspection systems with interfaces to permit greater accuracy at the final inspection, slitting and rewinding stage. Many more press models offer high levels of flexibility aided by interchangeable print units, often rail mounted, as well as hot/cold foiling and rotary screen units.
Another defining trend is the growing popularity among certain converters to offer flexible packaging, such as shrink or roll-on sleeves, especially where buyers require a one-stop service. Many more press ranges include mid-web versions of existing designs, backed by servo-assisted press functions, automated electronic controls, and centralized consoles. They are supported by improved flexo plates and anilox roll technologies. The ability of rotary and semi-rotary offset – often combined with UV flexo, rotary screen and gravure units – to deliver the highest quality on mixed substrates ensures a steady market for these presses despite their higher costs. The presence of lightweight plate cylinder sleeves to allow fast changeovers with varying repeat lengths, which is practically universal on offset combination presses, is a major attraction for this high quality process.
For many visitors, the highlight of the show was an ability to see a wide spread of digital printing technology in a single dedicated hall. Presentations by inkjet systems vendors especially highlighted the improved quality of drop-on-demand, single-pass inkjet printing using more refined printheads. One recent development is the adoption of cooler LED curing, as opposed to UV curing, on certain models. As with the availability of laser cutting, rather than hard tooling, it offers a further choice. Several of the more bullish vendors at the show claimed that job run thresholds, perhaps including versioning, favored the short-run capabilities of this process over flexo. Over 30 vendors represented the many variants of inkjet printing, from basic desktop printers to fully integrated press lines with a wide choice of finishing modules.
Given a market share of somewhere near 70 percent by the two leading digital press manufacturers, economic logic would suggest that some pruning among vendors is a near racing certainty. However, the market for digital presses has grown strongly in recent years; almost 20 percent of all presses sold are forecast to be digital over the next few years. What the digital presence showed at Labelexpo was the wide variety of applications, from producing top quality primary labels with good screening gradations, to the more prosaic logistics labels and tags with variable alphanumeric characters and coding.
Barry Hunt
Technical editor
Labels & Labeling
Stay up to date
Subscribe to the free Label News newsletter and receive the latest content every week. We'll never share your email address.