Contact vs non-contact web cleaning
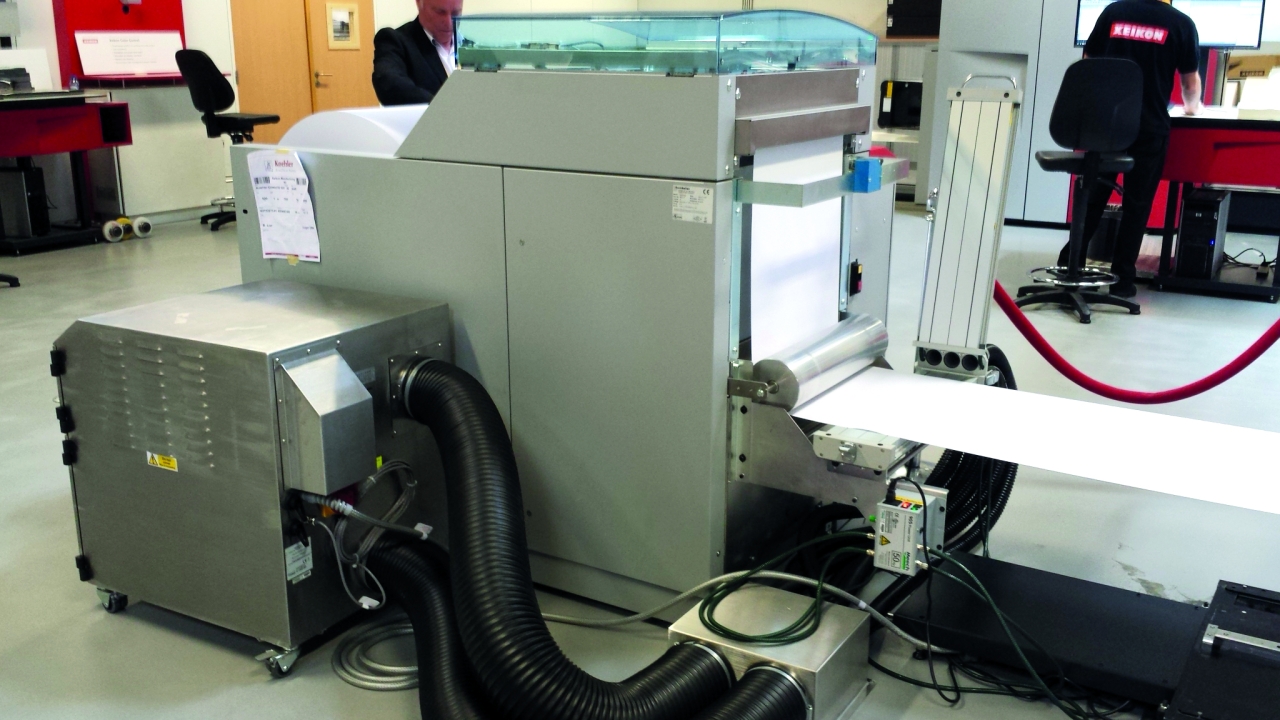
The need to minimize wastage and achieve higher levels of productivity is a key priority for label converters, who often struggle to determine whether contact or non-contact cleaners are the best option for dealing with the removal of contamination from their web process.
Narrow web presses used by label converters traditionally adopt tacky roller contact systems to efficiently remove contamination.
This method provides excellent cleaning and is mainly used for filmic substrates. For other substrates such as paper or board, which typically carry higher contamination levels, contact vacuum systems or non-contact systems are used.
Meech’s contact cleaning systems, the TakClean (tacky roller) and VacClean (vacuum), are employed mostly in the print and label printing sectors. Tacky roller contact cleaning systems in particular use elastomer rollers to remove dry, unbonded contamination from a moving web, which is then transferred onto adhesive roles where it is trapped. The design of the system also allows operators to see the contamination being collected on the adhesive roll.
However, there are some drawbacks to this method. While contact systems provide excellent cleaning, contamination will build up on the adhesive roll unless it is checked and changed on a regular basis.
This results in a gradual deterioration until the adhesive is refreshed and performance returns to 100 percent. As a result, tacky roller contact web cleaning may not be the ideal choice for more heavily contaminated materials.
In this case, non-contact or vacuum contact cleaning provide an alternative solution, as the system performance is not affected by the contamination level and no consumables are required, which helps reduce ongoing costs.
Non-contact
For example, CyClean, Meech’s latest non-contact web cleaning system, is capable of removing contamination to below 1 micron and incorporates fluid dynamic principles to deliver higher levels of cleanliness for label printing applications.
Cleaning systems on a narrow web press, are typically installed before the first print station, with static control systems before each of the other print stations to make sure the web stays static free, minimizing the potential of static induced re-contamination.
Two factors ensure successful cleaning. The boundary layer of air on the web must be broken, allowing contamination trapped under and within it to be removed, and the static charge on the web must be eliminated so that contamination can be removed. Only a system this thorough will result in a spotless web, which is of paramount importance in label printing.
This article first appeared in L&L issue 5, 2016, which can be read online here
Stay up to date
Subscribe to the free Label News newsletter and receive the latest content every week. We'll never share your email address.