Flexo? Offset? Digital? Hybrid?
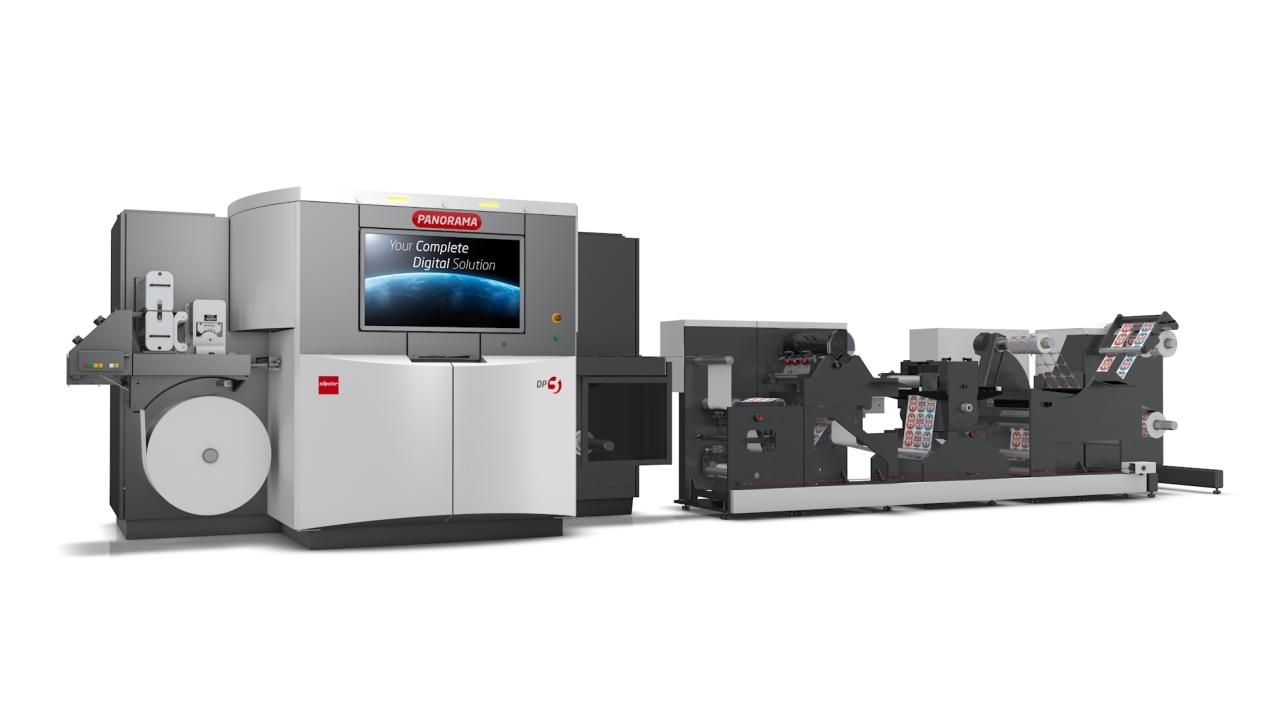
‘While the general printing industry continues to suffer with low margins, the packaging sector is continuing to thrive. This was particularly noticeable with all the major digital press manufacturers offering label, carton and flexible packaging options within their various programs. It was noticeable that the halls at drupa 2016 that seemed to be the busiest were the very halls where these products were being demonstrated. Despite the advance of digital processes, the conventional machinery suppliers were also in evidence. Presses with faster changeover times, hybrid alternatives and improved platemaking techniques continue to make advances. All in all, this is making the label producer’s choice of which investment to make for the future all the more difficult.’
John Bambery, chairman, BPIF Labels
‘Quality of any modern packaging printing process is, nowadays, “good enough”. Different packaging printing methods have their chance to grow, and although digital printing is gaining a lot of attention it will not be the major solution in the larger scale due to two main reasons: output speed and the cost of ink. Due to those two reasons, flexo has very large potential for growth – but not the traditional way of printing flexo. I am grateful that digital printing has solved the problem of purchasers complaining about the prices of small runs. Digital printing is easiest on fiber-based substrates, such as labels and POS, meanwhile we’ve even seen its advent for mid web plastic films. I see that purchasers and suppliers don’t use the most effective and economical way of producing small runs in flexo – although it is possible with expanded gamut printing. The short job length and ability to produce vastly variable data is the key to selecting digital printing, but the flexo re-revolution comes via co-printing of jobs, where the expanded gamut with fixed palette is the key to efficiency. The changeover times, production speed, productivity, the cost of ink are crucial in the total cost of the print – that’s why flexo will prevail as the best packaging printing process for labels, flexibles and corrugated in the coming years. Still, the way of working has to be changed.’
Kai Lankinen, managing director and co-owner, Marvaco
‘There can be no doubt that the ever-more-sophisticated digital print technologies are proving to be ideal tools in many sectors of label printing today, and in Finat we see digital label presses as perfect partners for analog narrow web label printing. Brand owners’ requirements are becoming increasingly complex, embracing short runs, personalization, product versioning, local language versioning, etc, and all within the context of faster speed to market. Digital print makes it all possible, at speeds which narrow web flexo presses cannot match. But there is no match for traditional narrow web presses when it comes to long runs and complex multi-process print, and today’s developing UV and LED technologies are enhancing ink curing speeds and delivering the economies of scale that the big brands want. Multiple ink colors, finishes, embosses and other haptic and optic effects come as standard with today’s highly flexible label presses; screen print units, security features and serialization complement their proven flexo capabilities. Hybrid presses combine the benefits of both technology pathways – but I believe they are specialist products with a limited market.’
Jules Lejeune, managing director, Finat
This article appeared in L&L issue 4, 2016, which can be read online here
See the results of the L&L poll, 'Which print process will be the most important to your business over the next three years?', here
Stay up to date
Subscribe to the free Label News newsletter and receive the latest content every week. We'll never share your email address.