The changing face of surface treatment
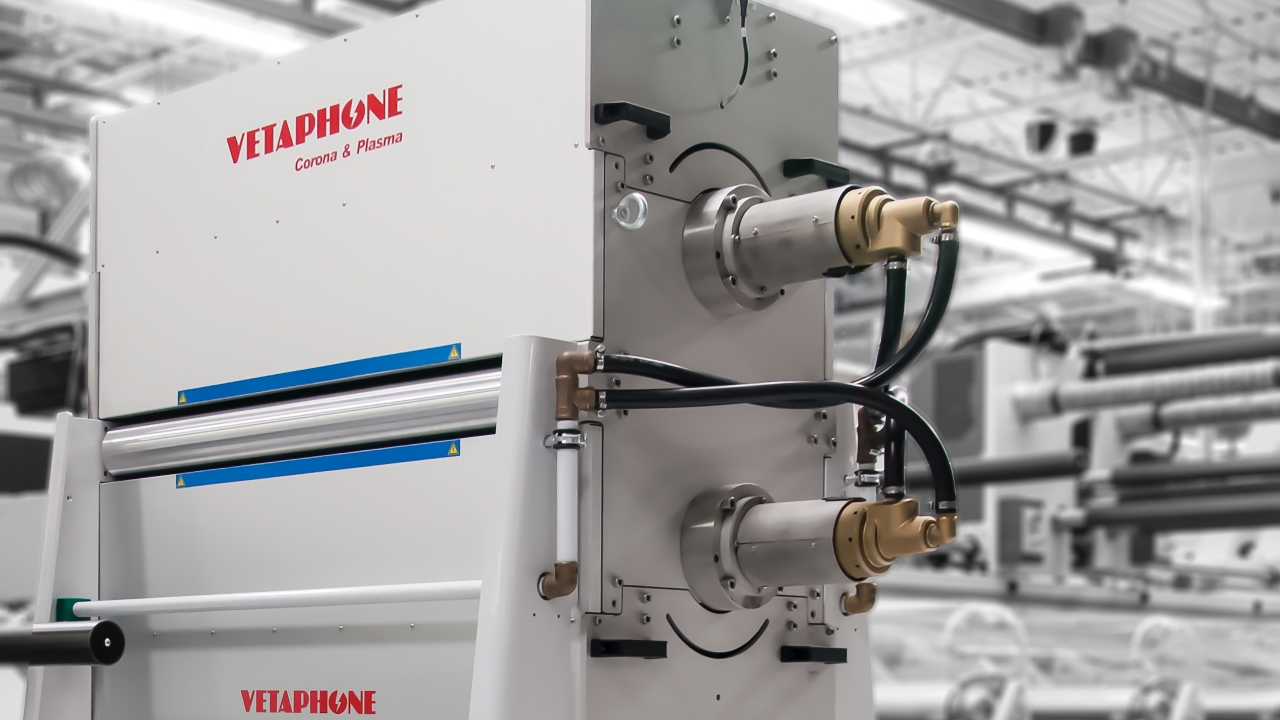
The need for surface treatment to improve the adhesive quality of ink and lacquers on plastic surfaces was established back in the 1950s, and the invention and development of corona treatment, as the process became known, has largely mirrored the requirements of the market in terms of performance over the intervening years.
But, it is fair to say that the problems facing narrow web converters now require a greater degree of understanding if the surface treatment applied is to be effective in today’s increasingly sophisticated market. Far from ‘buy, install, set, forget’, surface treatment has become as integral to quality production as any other part of the printing process, and to ensure you are using it correctly, you need to understand its operational parameters.
I will simplify matters by splitting the process into three clearly definable requirements. First, there is the need for simple corona treatment, and this applies to virtually all narrow web press applications. It will typically require a corona unit to deliver a power rating of 1.5-2.0 kW, and provide excellent performance on standard substrates run off at low to medium speeds.
The second section has been created by the development of new and more difficult substrates. These are run off on the latest generation of narrow web presses that have been optimized by manufacturers for high speed production. These factors place an increased demand on the corona unit to deliver the correct dyne level, which typically needs to be rated at 3.0-5.0 kW. To understand this concept, think of the similar situation with UV curing, where dwell time under the lamp, defined by power rating and running speed, are critical to achieving a complete cure.
The third section relates to those substrates that have been developed to produce what I will call ‘unique’ labels, typically using special inks and lacquers, lamination, multi web applications and other techniques to produce sophisticated products. The chemical constituents of these substrates require a chemical treatment process as well as a physical one, and in these instances plasma treatment is necessary to ensure bonding. Plasma should not be considered as a replacement for corona, more as a logical development of technology to keep pace with the requirements of more sophisticated materials and processes.
With print quality taken as a given in today’s market, it is essential that converters appreciate the importance of what can appear to be a minor ancillary process. It’s only as minor as expecting a performance car to run properly on low grade fuel. Converters need to wise-up on what all their technology can do for them, and not allow surface treatment to be the forgotten element.
Stay up to date
Subscribe to the free Label News newsletter and receive the latest content every week. We'll never share your email address.