Dealing with waste
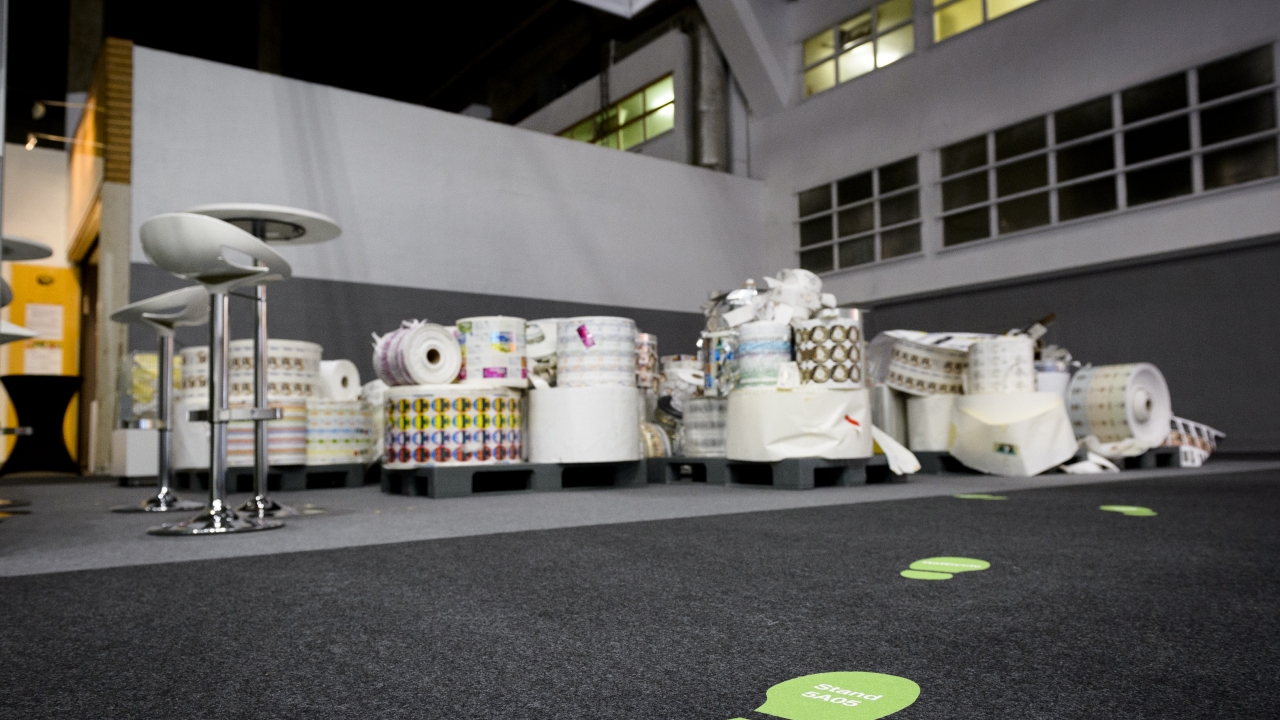
Solid waste streams in a label plant can consist of matrix, edge trim, and set-up material, plates, inks and containers. Today it is estimated that 85 percent of label industry-specific material waste, matrix and release liner, is sent to landfill.
There are three key barriers to overcome in order to increase label industry recycle rates in North America, and globally: logistics, volume and location. The cost of current options is greatly dependent on these barriers.
As part of its Strategic Plan, TLMI intends to be a leader in overcoming these challenges, and has set goals to reduce the volume of matrix and liner becoming waste by thirty percent. Converters across the US and Canada are actively looking to find alternative options to landfill.
There are benefits found in retaining the value of label material waste: landfill avoidance; revenue stream, as natural resources increase in value; cost savings, based on regional disposal costs; reduced methane emissions; reduced gas usage and related air pollution, based on location.
Reducing waste to landfill
Grand Rapids Label, based in Michigan, has achieved year over year improvement in reducing waste to landfill, surpassing its goal of increasing its recycling rate by 2 percent annually. Today the converter recycles all of its solid waste material, except for matrix. It hopes to find a sustainable solution by the end of next year.
Yerecic Label, located outside Pittsburgh, Pennsylvania, has moved from 99 percent matrix waste to landfill in 2010, to +99 percent waste to energy (WTE) in 2017. For the last four consecutive years, Yerecic Label has sent less than one percent of its waste to landfill. The WTE program partner replaces coal with matrix waste to fire cement kilns. Data shows that waste matrix from the converter generates a higher heat value than coal per pound. Since participation, Yerecic Label’s waste recovery volume equates to heating 800 Pennsylvania homes for one year.
Maryland-based Hub Label also partners with a local recycler to transform matrix waste into energy used as an alternative fuel in concrete production. In order to participate in this process, the converter must sort the material. It established a visual management system to communicate each receptacle to employees and visitors, achieving nearly 40 percent reduction in landfill waste between 2012-2016 by adopting this WTE program.
TLMI’s appointment of Rosalyn Bandy to director of environmental strategies and outreach will support the organization and membership in achieving their goals, and overcoming the obstacles in confirming viable waste recovery channels for converters throughout the US.
This opinion article was first published in the 2018 L&L Yearbook, available to read online here
Stay up to date
Subscribe to the free Label News newsletter and receive the latest content every week. We'll never share your email address.