Reflecting on 45 years in the flexo label industry
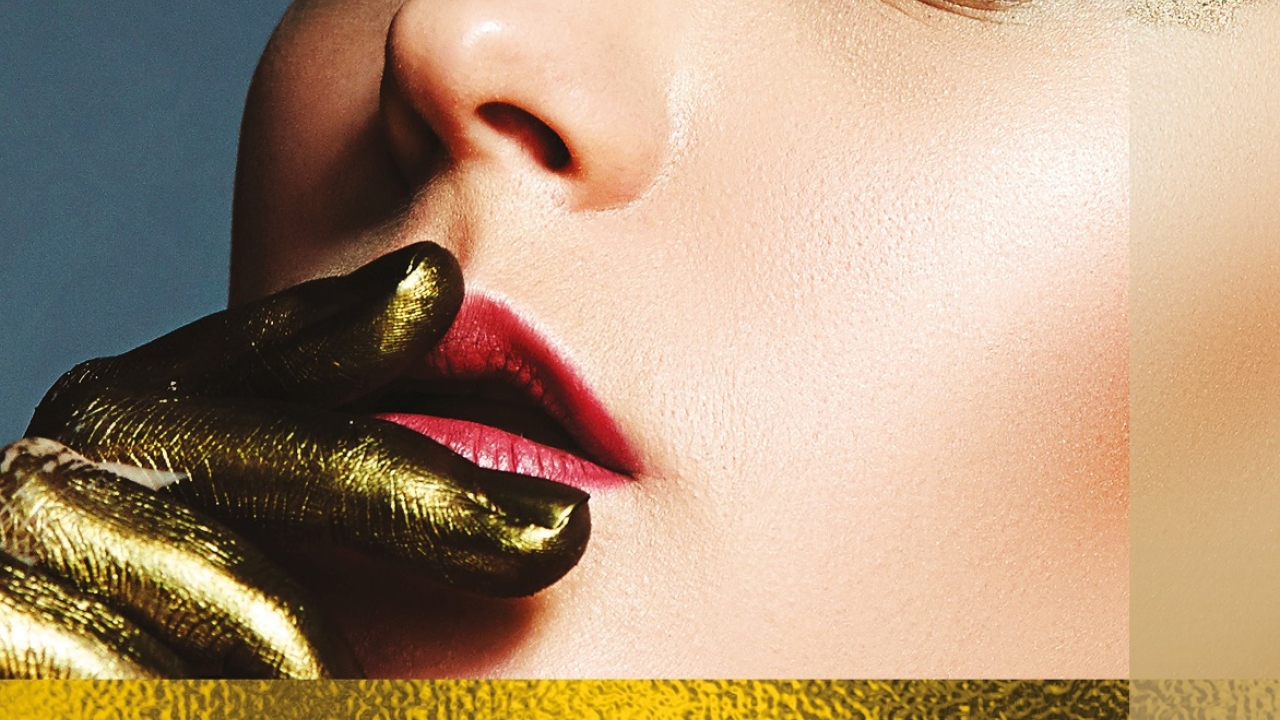
Asahi Photoproducts is a specialist in flexographic photopolymer plate development. It was founded as a subsidiary of the Asahi Kasei Corporation in 1971, holding its European Headquarters in Belgium.
Photopolymer plate technology first came to market in 1974, based on free radical polymer chemistry that uses UV light to form 3D relief graphic images
Dr David Galton, European sales director at Asahi Photoproducts Europe, comments: ‘Forty-five years is a long time, and much has changed. Forty-five years ago, the narrow web reel-to-reel market was dominated by two flexographic printing press manufacturers: Mark Andy and Webron. As the need for labels became more complex, other manufacturers, Nilpeter, Comco and the Canadian Primoflex Systems (CPS), started to emerge with novel design features. The rapid expansion of the label market combined with growing competition meant that better flexographic printing equipment was available, and by 1972 the first commercial four-color process printing was possible. Today, flexographic printing is competitive with both offset and gravure – and even with digital except for very short runs below 1,000 linear meters.
‘It’s been a great deal of progress, and we are proud of the role we have been able to play in fostering this progress through the introduction of innovative flexographic plates and plate processors.’
Galton continues: ‘The introduction of the Apple Macintosh in 1984, the first mass market computer featuring a graphical user interface, built-in screen and mouse, had a revolutionary impact on pre-press for labels. And the Danish company Purup Electronics (Eskofot) followed in 1988 by bringing computer imaging systems to market that revolutionized the creation of label images and artwork. This set the stage for many other innovations that have driven the market forward, including the introduction at drupa 1995 by DuPont of the first flexographic computer-to-plate system. Today, computers play an integral role in everything from sparking the first design ideas to getting the final product on the shelf.
‘Forty-five years ago, cell counts did not exceed a maximum of 550 cells per linear inch. Many anilox rolls worked with ink film thicknesses of 4-7 microns. In 1990, an 800 lpi design with a 60o hexagon cell was developed by Harper and was a phenomenal success. This new cell pattern also helped reduce ink film thickness. This new roll could control ink film thicknesses to 0.5-1.5 microns and quickly became the industry standard. Cell patterns can now be etched at 30o, 40o, 60o, and recently random patterns are used, with cell counts reaching of up to 1,800 cells per inch.
‘Cleaning of anilox rollers with such fine screen engravings is paramount. Some manufacturers coat their rollers to help keep the cells free from drying ink. Conventional off-press cleaning methods include ultrasonic cleaners or soda blasting, in addition to fine bristle brushes.’
The development of photopolymer plate technology has been of equal importance, notes Galton. First coming to market in 1974 and based on free radical polymer chemistry that uses UV light to form 3D relief graphic images, these plates continue to undergo development advances, ‘that have been critical to the ability of flexographic printing to not only be competitive with other printing technologies, but to become the leading label production printing technology,’ notes Galton.
‘This is where Asahi’s more than 45 years of experience with innovation in polymers has truly come into play.
‘In 1982, we launched our AFP family of plates with specific benefits for labels. AFP plates are manufactured using Butadiene and Styrene to improve the malleability of the plate and the drape of the plate around small circumference cylinders. This solved plate lifting issues. AFP also was the first solid plate to have a wide exposure latitude which enabled solids and halftones with one main exposure. This was a major development in flexography. In 1985, Asahi invented the dry germicidal UVC lamp anti-tack process that eliminated the wet process by bromide.
‘Then in 2000, we began manufacturing the first aqueous plate technology for the label industry. Years later, this was combined with Clean Transfer Technology; the result was plates from Asahi Photoproducts that have been specifically engineered to transfer all remaining ink to the printed substrate. This is due to the plate’s lower surface energy. Clean Transfer Technology plates do not need to be cleaned as often as conventional digital solvent plates. Reduction of plate cleaning stops creates a significant productivity improvement. More specifically, it reduces ink filling, particularly important for mid-tone printing, and that means fewer press stops for plate cleaning as well as consistent printing quality over the entire production run. The result is significant improvement in printing press OEE. Unique Asahi engineering also facilitates kiss touch printing pressure. Lighter printing pressure ensures constant repeatability of printing quality during the production run as well as longer plate life.
‘Our Clean Transfer Technology has received great market reception in our line of water-washable plates, and we are now excited to be extending this capability to other plate categories in our portfolio. Not only will this help flexographic printers increase productivity, but it will also extend the range of applications they can offer customers, including the ability to transfer even more work from offset to flexo.’
Asahi Photoproducts Europe is also to introduce a new AWP water-washable flexographic plate and a brand-new plate family, AFP BFT H and M.
Akihiro Kato, managing director at Asahi Photoproducts Europe, adds: ‘Looking ahead to 2019, we have more innovation coming, and we are excited to be in a position to help continue the forward progress in flexography.
‘We are looking forward to continuing momentum in 2019, and we have new innovations in the works that we will be sharing at Labelexpo Europe 2019 and drupa 2020.’
Galton predicts: ‘We believe flexography will continue to be the dominant printing technology for labels for some time to come, and in addition to extending Clean Transfer Technology to other plates in our portfolio, we are working hard to continue to bring innovations to market, including both plate and processing technology, so that 45 years from now, we can again look back on a history of innovation and contributions to the market.’
Read more predictions from the label and package printing industry for 2019 here
Read about UK repro company Creation and its use of Asahi technology in Labels & Labeling issue 4, 2018 and here
Labels & Labeling issue 6, 2018 is a special 40th anniversary edition celebrating four decades since the magazine was first published. With input from across the label and package printing supply chain, from around the world, we reflect on the development of the industry over the last 40 years and look to the future
Stay up to date
Subscribe to the free Label News newsletter and receive the latest content every week. We'll never share your email address.