The unseen problem with labels
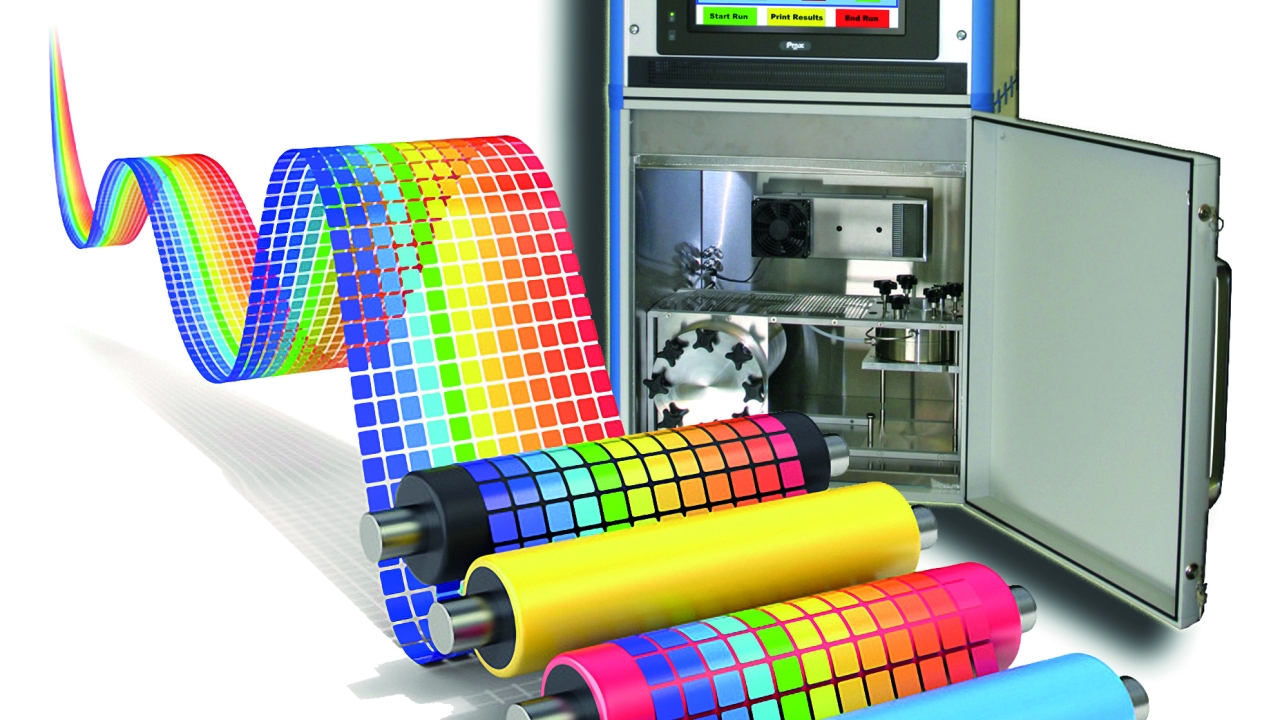
When you look deeply into the technology behind any industry you find a lot of practical issues that seem to get in the way of ‘the perfect job’. With the label industry there’s a particularly big one that, surprisingly, most people don’t know much about, yet it not only affects print quality, surface, adhesion and sometimes the physical stability of a label, but it is often critically important in these areas.
The problem is vapor permeability – the way a vapor can sneak, molecule by molecule, through paper or plastic in a way that liquids can’t. It doesn’t sound important, does it? But let me give you a surprising example – cellulose, EVOH and PVOH are all widely used plastics and form great barriers to liquid water. However, water, as a vapor, can pass straight through all of these, almost as if they weren’t there.
The same thing is true with every material, to a greater or lesser extent. It affects both the gasses that help cure inks and adhesives plus the vapors from inks, toners, solvents and adhesives themselves. Even more complicated is the fact that each and every material acts differently for each and every vapor. Don’t get me wrong, sometimes this is a good thing – for example the way inks dry and print quality both depend on it. But with the wrong choice of coating, substrate or laminate, issues can arise and you can lose print quality, adhesion and physical strength to name but a few things.
Carbonated water
Carbonated water is another example where problems can arise from vapor permeability. Lots of people like ‘fizzy water’ and have been drinking it since it was first produced artificially in the 1750s. One problem is that the glass bottles traditionally used are heavy and expensive. When plastic bottles were introduced in the mid-1900s they were seen as a wonder product, and when PET bottles arrived in the 1970s they must have seemed like the ultimate answer for fizzy drinks. But in just 12 weeks a plastic bottle can lose up to 15 percent of its carbon dioxide content.
With the advent of shrink sleeves, it was realized that if you make the label from the right barrier material, with the right permeability to carbon dioxide, you can keep the water fizzy for longer. The same applies to lots of products that decay, from cheese through to strawberries, with packaging now used explicitly to preserve content. Incidentally, if you pack either cheese or strawberries in the other’s packaging they actually go off far more quickly.
Every paper, board or plastic, label, ink, toner and solvent requires an individual option to optimize vapor permeability, but, nonetheless the system works. In a very similar way, print quality, adhesive strength/ durability/curing, and sometimes even the physical strength of the label, can all be affected by the way vapor permeates through the substrate, as can label swimming, caustic label removal and the print (especially on paper) surface as, during manufacture, air becomes entrapped in microscopic ganglia.
Competing requirements
The answer to the problem, at first sight, seems obvious; a good choice of substrate, a suitable coating or laminate and the problem is solved. Not so.
Many characteristics have competing requirements, for example, a paper coating that optimizes print quality, may well affect adhesion. And, more importantly, a coating that is good for a specific ink or color, will almost certainly be wrong for many solvents and adhesives. The vapors that evaporate from solvents, adhesives, inks and toners are highly complex and each molecule has an individual vapor permeability value for every substrate and coating.
Great strides have been made in the last few decades in understanding the detailed physics behind this process, but it is still not completely understood. In the real world, the best option is invariably a compromise between the competing requirements, and there is a growing trend towards multiple coatings using different materials to give the most appropriate ‘designer solutions’. The question becomes, how do you achieve this for your specific requirements?
Well, those nice fellows who design and produce coatings usually have a lot of experience and an understanding of the physics and chemistry of it all. Don’t worry, you don’t need to understand everything, but you do need to understand the principles and have a grasp of what they do.
How do you measure permeability?
Until 30 years ago the most realistic way to measure vapor permeability was using gravimetrics, which involved sealing a little cup filled with vapor-absorbent granules, weighing it, exposing it to the vapor for some weeks or months, and then weighing it again to see how much vapor had passed through.
Today, we use instrumental techniques that measure it both quickly and accurately. First of all, coating(s) is/are added to a specific, strong and stable base. Then the sample is fixed in a chamber and its two sides are exposed to different controlled atmospheres, one being the vapor under test, the other an inert gas.
Where required, perhaps for a shrink sleeve, the system can measure permeability under a range of temperatures and pressures, which both affect permeability in non-linear ways. Basically, the vapor under test flows across one side of the coated sample or film, molecules from the vapor pass through the coating and are counted when they reach the other side. Different vapors and environments need different sensors to do this but they have become extremely sensitive, with accuracies ranging from parts per million through to parts per billion.
You can actually measure the overall permeability of a bottle of fizzy water complete with its shrink sleeve, simply by placing it in a container with the inert gas flowing around the outside of bottle.
Getting it right
Using a material with the right vapor barrier properties for your labels, no matter if they are paper, plastic, card or anything else, can make a huge difference to the finished product. This is why coated papers represent a 40 billion USD industry.
There is a growing trend towards customizing coatings to make products suitable for specific applications. This same trend took off some while ago in the food industry, kicked off by the needs of modified atmosphere packaging, but is now spreading throughout the drinks industry and beyond.
Getting it right can lead to better print quality, adhesion and improved products with better performance. With permeability, what starts out to be a barrier may well end up as a solution.
This article appears in L&L, issue 1, 2017
Stay up to date
Subscribe to the free Label News newsletter and receive the latest content every week. We'll never share your email address.