‘Dual Cure’ smoothens switch to UV LED
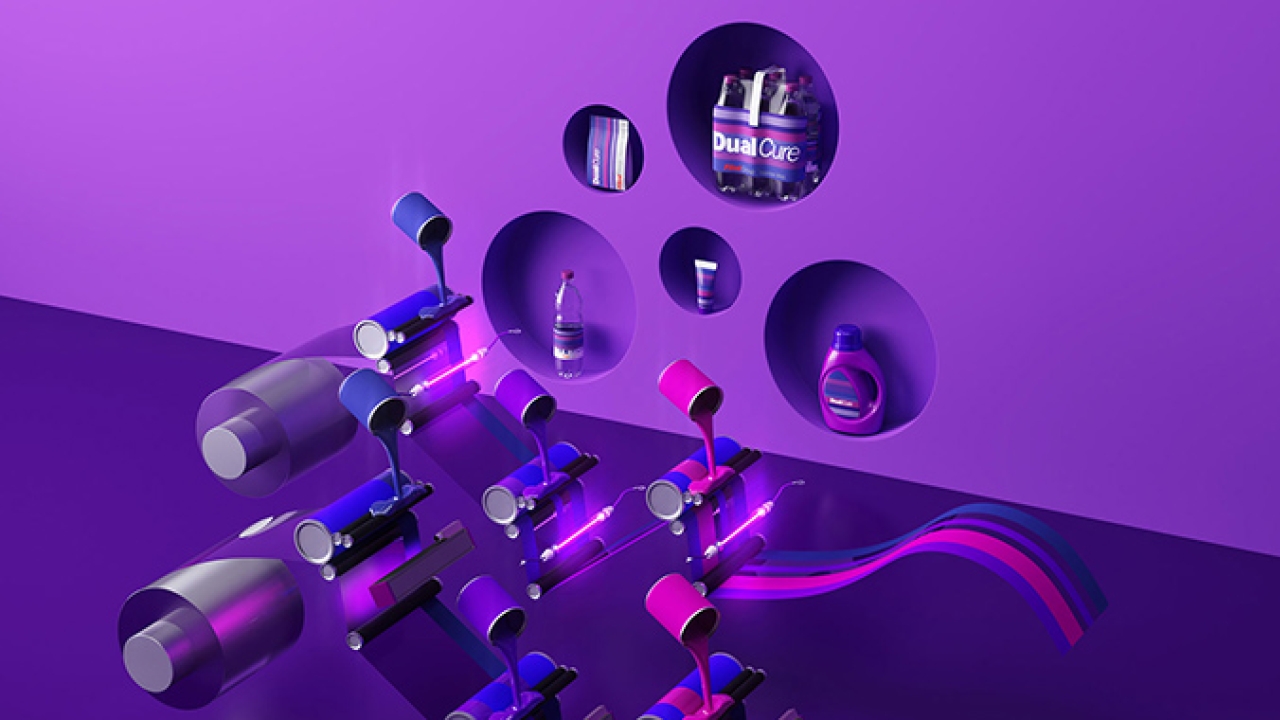
Nearly a decade after their introduction, UV LED curable inks are being adopted at an accelerated pace by label converters. The ink’s benefits over ‘conventional’ mercury UV inks – better and faster curing, improved sustainability and lower running costs – are becoming more widely understood. Additionally, the technology is becoming more easily accessible as press manufacturers offer to include a wider range of long-life lamps on their lines.
Moreover, there is a greater incentive for converters to consider switching to LED, because the risks and costs of doing so are reducing. This is being facilitated by the arrival of a new generation of ‘dual cure’ inks and coatings that can be run under both LED and mercury lamps, allowing converters to adopt the technology in steps, rather than abruptly.
The main difference between a conventional mercury lamp and an LED lamp is the wavelengths emitted for curing to take place. The mercury-vapor lamp radiates energy across a spectrum between 220 and 400 nanometers (nm), while LED lamps have a narrower wavelength between about 375nm and 410nm and peaking at around 395nm.
UV LED inks are cured in the same way as conventional UV inks, but are sensitive to a narrow wavelength of light. They differ from each other, therefore, by the group of photoinitiators used to initiate the curing reaction; the pigments, oligomers and monomers used are the same.
UV LED curing offers strong environmental, quality, and safety advantages over conventional curing. The process uses no mercury or ozone, so no extraction system is needed to remove ozone from around the printing press.
It offers long-term efficiencies too. The LED lamp can be turned on and off with no need for warm-up or cool-down time, providing optimum performance from the moment it is switched on. There is no need for shutters to protect the substrate if the lamp is switched off.
Energy costs of UV LED are lower: it has no infra-red emission and thus produces less heat as a byproduct, making lower heat management costs possible, as no heat-reducing measures are needed to protect the substrate during production. The lower heat emission is a major contributing factor to the longer life of LED lamp components: some LED lamp manufacturers claim lifespans of up to 20,000 hours, while a mercury lamp may function for around 2,000 hours. It also enables thinner filmic substrates to be run without risk of warping.
While a mercury UV lamp cures from the surface downwards, LED achieves a thorough and faster cure, because its energy penetrates through the ink, initiating the cure at the substrate interface where the bond is crucial to anchorage. This is advantageous for migration-restrictive applications like food and pharmaceutical packaging: the more thorough the cure, the less the migration potential. The thorough ‘bottom-up’ cure overcomes problems experienced with curing dark blue, black and opaque colors – notably whites – under conventional lamps.
More effective curing opens up the possibility of faster production speeds, especially for pure flexo applications where there is no die-cutting, such as shrink sleeves and flexible packaging. High curing speeds have also helped drive greater market acceptance. We see UV LED flexo inks performing at up to 1,000ft/ min, and at Flint Group, we validate at test speeds of 750ft/min.
Converting to pure UV LED ink
With this strong combination of benefits, UV LED offers long-term improvements to the label converter’s bottom line. Even so, many label converters still find the prospect of switching to UV LED daunting, because of the disruption it may cause.
The concern is justified, if one switches to an ink set that only cures under LED, as it would mean an abrupt switch, requiring significant upfront costs and planning to coordinate the changes. The most obvious considerations would be the cost of a complete lamp conversion on each flexo station, and the lost output due to press downtime during the conversion. Also, depleting and replacing ink stocks in a short time-frame would mean a surge in logistics, especially in warehousing, procurement and the ink kitchen, where turning over the dispenser will result in disposing unused old ink. A steep learning curve would be needed as operators seek to achieve identical color targets.
The transition from conventional cure to UV LED, therefore, is an important strategic decision for our customers. That is why we have worked to reduce the risk associated with that transition, by developing an ink set that works with their current and future capabilities.
Our strategy has been to reformulate our complete program of narrow web inks, so that they fully cure under LED or mercury lamps. By carefully choosing the mix of photoinitiators to initiate the curing process in both situations, our chemists have developed a ‘Dual Cure’ ink range. It covers process and Pantone colors, plus the vast majority of coatings, tested and qualified on many application-specific substrates.
Coming under our EkoCure brand, these are formulated at the same strength as their conventional counterparts, making color-matching simple. EkoCure F is suited for printing on almost all film and paper labelstocks, as well as cartons and tags. EkoCure XS is specifically for shrink sleeve labels, and can shrink by up to 70 percent without deterioration of the printed image. For the most stringent food contact applications, EkoCure Ancora complies with the Swiss Ordinance list and is manufactured in accordance with EuPIA good manufacturing processes.
The chemistry of a Dual Cure ink is much the same as one cured by a mercury lamp. Once cured, the ink behaves similarly to a conventionally cured ink on the substrate. This makes it possible to run the ink alongside conventionally cured inks in the same pass – and on a single printing station if desired, without compromising quality.
With this versatility, Dual Cure ink gives the converter the freedom to switch to UV LED at a speed that fits their business – one color or one press at a time, perhaps – without the prohibitive expense of needing to install a new LED lamp on every station.
Some converters have gained their first experience of LED by installing a lamp on a single station, for example to test a specific color, without needing to carry a dual inventory. In this way, the transition can stretch over a period of time, enabling the operators to become accustomed to handling the new ink, avoid a total press shutdown, and also see productivity improvements.
For instance, running a dual-cure black ink after the CMY positions is an effective way of appreciating the technology’s benefits: cured from the bottom up, adhesion is achieved more effectively in a shorter time, allowing the printer to achieve faster line speeds. Many lamp manufacturers offer to retrofit an LED lamp for trialing purposes, reducing the risk of investment.
Our technical team works with customers to help them manage the risk of their transitions, from planning to validation. We help customers choose the investment in time, materials and learning that is right for them. With our printing and plate-making division we are able to conduct testing on the converter’s behalf, enabling a seamless transition without the risk of remakes.
R&D focus
Our research and development teams continue their work in expanding and optimizing the range of UV LED inks and coatings, also supporting customers that seek a solution for a specific application. Products are validated in our laboratory, on a test press using lamps from leading manufacturers, using a wide range of film and paper laminates found in the market.
Through internal testing at our R&D sites in Rogers, USA, and Trelleborg, Sweden, and in real life situations with our customers, we have gained significant practical knowledge around formulation, behavior on press, ink room challenges and performance in numerous applications. Our team members, several of whom have decades of experience to draw on, collaborate with co-suppliers to access new technologies and research conducted in other industries, such as automotive, to find solutions to our customers’ challenges.
The advance in the performance of UV LED coatings, applied after the printing process, is one example. Aided by supply systems for better viscosity control, flexo printers are turning to new UV coatings that enhance visual and tactile appeal in innovative ways, for instance with the velvet touch and metallic effects. Using new photoinitiators on the market, we have reformulated our LED-curable coatings so they offer improved clarity, ensuring that the color of the underlying graphic remains unchanged throughout the label’s working life – without the risk of ‘yellowing’.
In our experience, successful transitions to UV LED are ‘evolution,’ rather than ‘revolution’, with printing lines upgraded in logical phases that allow for learning along the way without jeopardizing delivery to customers, before moving on to a full conversion. Taking that journey in stages with a Dual Cure ink, the converter can better manage its ink inventory through the transition, with fewer quality claims, reduced material scrap, no need to waste ink, and no risk of downtime through running the wrong ink on their press or station.
With an ink supplier with a wide program of inks and coatings, including specialty products, and the capability to provide comprehensive support, including ongoing R&D collaboration, the converter is best placed to achieve the transition smoothly.
Stay up to date
Subscribe to the free Label News newsletter and receive the latest content every week. We'll never share your email address.