Asan Pack sees bright future in labels
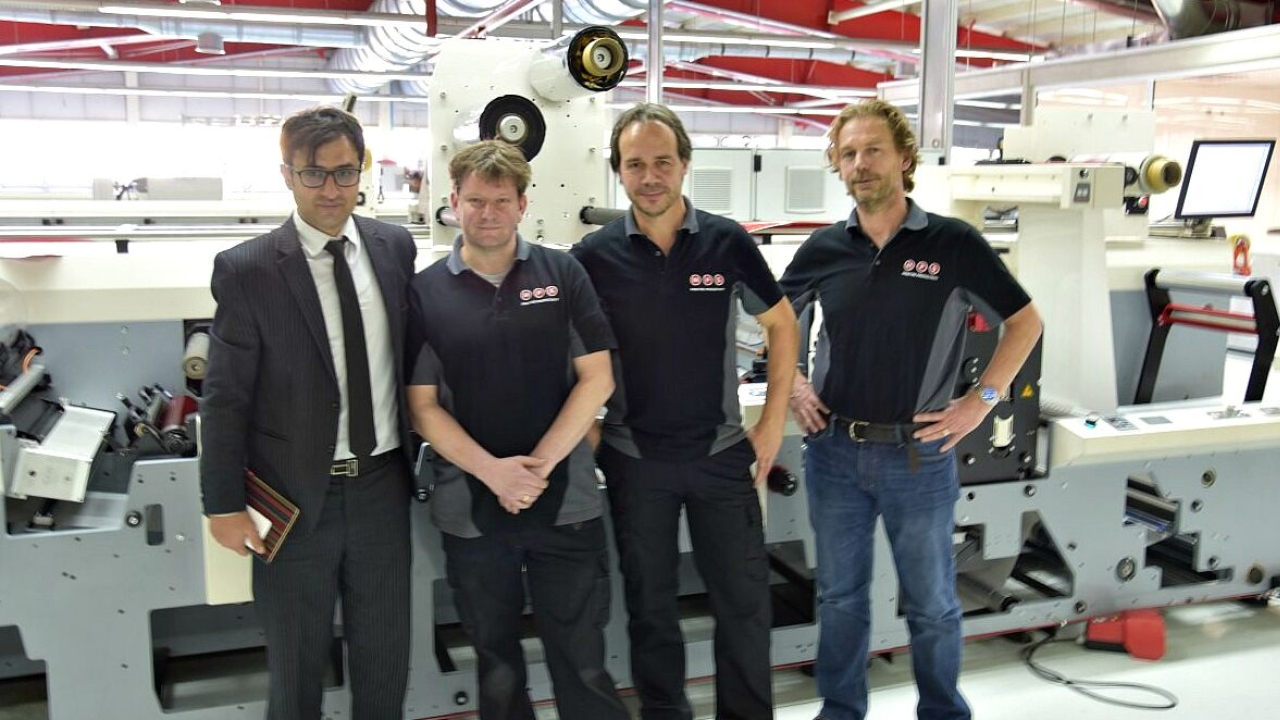
Producing 70,000 tons of corrugated cartons and 20,000 tons of cardboard packaging with multi-color printing per year, Asan Pack supplies reputable brands such as Nestlé, Danone, BAT (KENT), Sony and Samsung, in addition to many other well-known local Iranian businesses. With Iran’s population of more than 75 million people, Asan Pack is ideally positioned to enter the niche narrow web label market, with focus on customers in Iran and neighboring countries.
Adding label and flexible packaging to its portfolio, Asan Pack can now offer its customers a one-stop shop for self-adhesive labels, wrap-around/shrink packaging, plastic or aluminum lids and other label products.
Asan Pack has built an extension to its existing 45,000 square meter state-of-the-art board manufacturing and printing plant in Qazvin, Iran, for the production of label and flexible packaging.
The entire factory was completely reworked with a new air conditioning system, new offices, and construction of an ultra-modern infrastructure for its new label production plant. Asan Pack is very ambitious and is investing now for future expansions.
At the heart of Asan Pack’s new factory for label production are three new flexo MPS presses: two EB machines and an EF press. Asan Pack is initiating label production on its two MPS EB full UV label presses with eight print stations and equipped with cold foil and lamination options, double Quick Change Die stations with iStrip matrix rewind and dual rewind options.
The third EF 430mm multi-substrate MPS press offers customers the choice of flexible packaging as well as board and aluminum printing possibilities. The EF press is a fully equipped UV press with delam/relam for adhesive printing on two print stations, a multi-laminating unit for both laminating and cold foiling, a Stork silkscreen print unit, dual Quick Change Die station and iStrip matrix rewind. All three MPS machines have the standard MPS rail system for optimal flexibility of the machines and all converting options for future enhancements.
High standards
Mehrdad Nabatchian, CEO at Asan Pack explains why the company chose MPS for all three presses: ‘All of our printing machinery is represented by top European brands, as we seek high standards in our production investments. We identified MPS as a reliable partner with superior technology, who also offered a thorough training program for our operators new to flexo and the label printing process. With our new MPS presses, and expertise shared by MPS, we are ready for the world of narrow web label and flexible packaging printing.’
John Beltman, MPS project manager, comments: ‘The Asan Pack technical staff were a tremendous help with logistics in preparing the site, ensuring all fittings to the three machines fitted perfectly, and assisting during the set-up and install of the presses. Close attention was also given to ensure the area surrounding the presses was pristine and organized, resulting in a very pleasing environment to work in.’
Prior to delivery of the presses, the MPS training and consultation services for Asan Pack began at MPS headquarters in Arnhem, the Netherlands, where newly hired Asan Pack press operators received their first introduction and basic training in flexo printing. During the course of two weeks, four Asan Pack press operators learned how to operate flexo presses. All four operators received certificates recognizing their initial basic training program.
Full operation of the new label plant began in January 2017. During the pre-start-up phase, MPS’ print manager Hans Poortinga and application specialist Richard Meurs spent two weeks on-site at Asan Pack with factory staff, starting at the pre-press department where training was given on platemaking, followed by plate mounting, press set-up and finishing.
As the Asan Pack operators had already received basic training at MPS, label production began quickly. While Richard Meurs worked alongside the Asan Pack operators, Hans Poortinga concentrated on the press room logistics, educating support staff on all relevant parts of the complete process.
At the end of the two weeks, the first real commercial product was produced for a local customer – several thousand tea tags were printed on the MPS EF press.
Stay up to date
Subscribe to the free Label News newsletter and receive the latest content every week. We'll never share your email address.