The ascent of Abbott Label
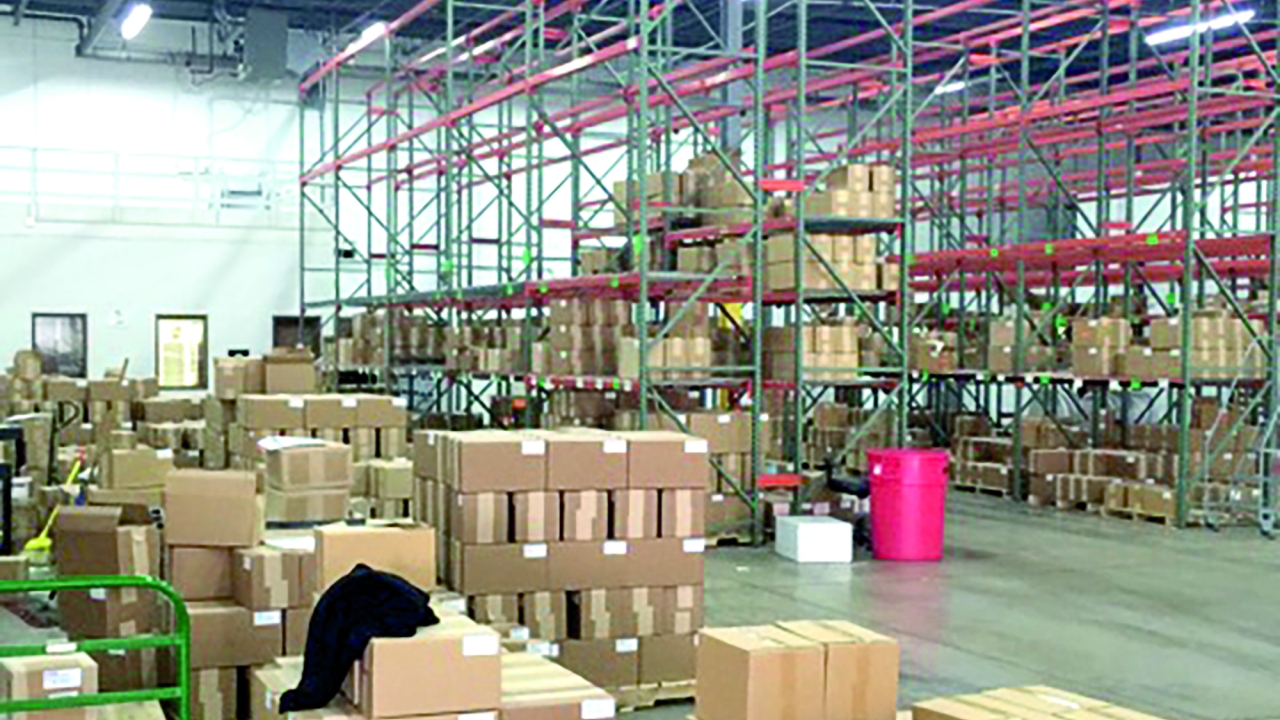
In 15 years Abbott Label has grown into one of the largest wholesale label manufacturers in the US. Headquartered in Dallas, Texas, it has satellite production locations in: Atlanta, Georgia; Santa Fe Springs, California; and Itasca, Illinois.
Explains John Abbott, Abbott Label founder and president, ‘We have chosen our locations because that’s where our key suppliers have easy distribution. Every one of our plants can get material the same day or the next day, and that’s part of the service. We firmly believe that you can’t service people unless you have the equipment there.’
The converter produces for resellers only, stocking a vast array of materials including thermal transfer, direct thermal, and laser stocks for applications such as warehousing, shipping and receiving labels. Abbott Label produces a lot of work for the packaging industry, for example box suppliers interested in bidding on label business that provides potential customers single source service.
‘Labels become a part of what some of our customer base is trying to sell,’ says Abbott. ‘These guys need someone to support them in manufacturing, and we do.’
Abbott Label prides itself on delivering orders the same or next day. It has flexographic printing equipment in 10 inch and 17 inch widths with four to eight color stations for producing commodity labels as well as food, beverage and industrial prime labels. It can also produce integrated label forms, some flexible packaging and short run full color digitally printed labels.
Each facility has at least one stand-alone die-cutting station to realize off-line finishing. There is redundancy built into the press and finishing assets used at each of the plant locations to ensure speedy turnaround times as expected by Abbott Label customers.
The converter has more than 10,000 different solid dies warehoused plus a growing number of magnetic cylinders and dies. Die usage is tracked between the plants and when a piece is borrowed more than once, then the facility purchases its own die to have on hand.
Abbott continues, ‘Thirty percent of our work is with other label manufacturers who don’t have the same capabilities as we have or the ability to turn work around like we can.’
Stay up to date
Subscribe to the free Label News newsletter and receive the latest content every week. We'll never share your email address.