Automatic plate mounting
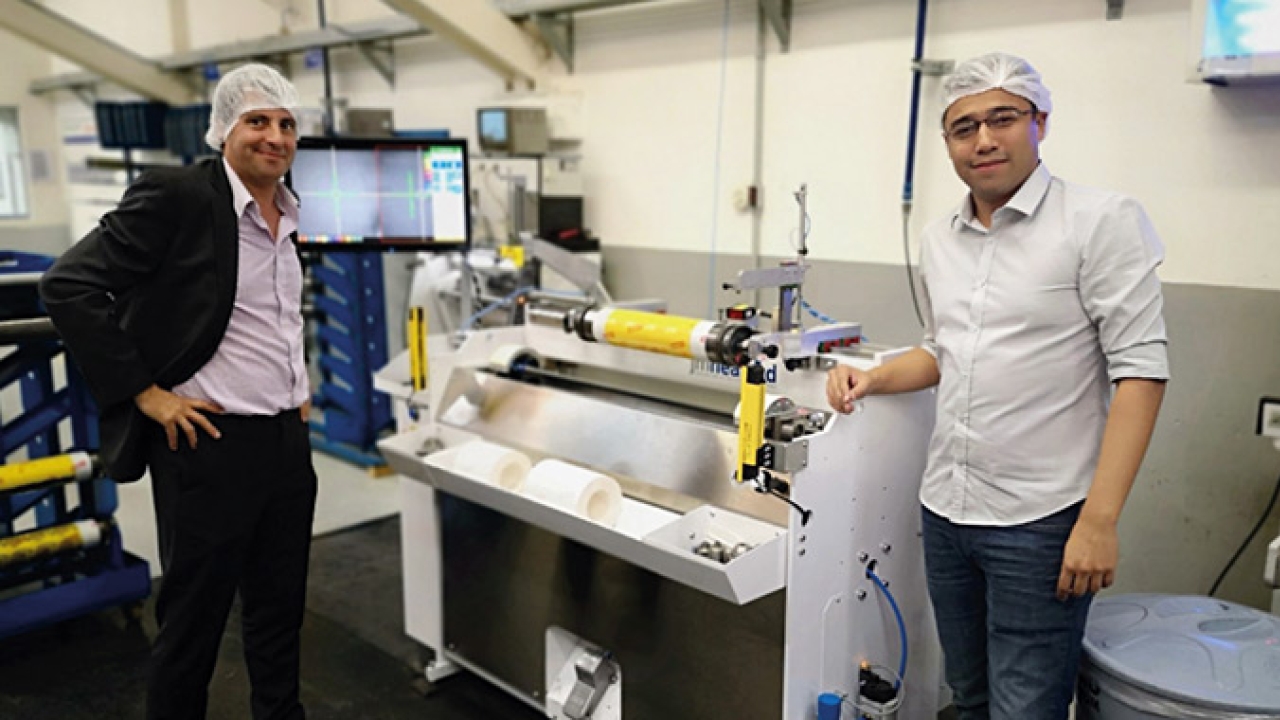
The automatic mounting of photopolymer plates in flexographic printing is well documented in mid and wide web applications. Significantly, these automatic mounters are also being supplied in the narrow web market with many label manufacturers now adopting this technology – not just larger label converting groups with multiple presses and facilities but also smaller independents who see the flexibility gains of equipment that doesn’t need highly skilled operators. Many press manufacturers are also recommending automatic mounters to their customers, as they complement the continuous advancements they are making in technologies to improve flexographic print quality. With this shift to automation, we explore how they work and what advantages they offer over other conventional plate mounters.
Speed of mounting is an important variable in the mounting and printing workflow, but printers are also looking for machines that are operator independent and have repeatable results. Accurate and repeatable consistency eliminates the possibility of time-consuming re-mounts, reducing press downtime, as well as wasted substrates, inks etc. Often, mounting machines are used to service multiple presses, and therefore it’s critical to ensure that mounting doesn’t become a bottleneck in the job set-up process, which can lead to reduced press productivity, and ultimately reduced profitability. Reducing run lengths increases the number of job changeovers per shift, making fast, ‘right first time’ job set-up/changeover critical, ‘as the press is only generating revenue when printing products of commercial value’, to quote our founder John Heaford. Some mounting machine manufacturers have responded to these market demands with automatic mounting machines, so that mounting is not only fast, but is highly accurate, repeatable and an easy process with consistent results.
Automatic mounting
Typically, most automatic mounting machines work in a very similar way. The plate is positioned in the mounter, so that the registration marks are in the field of view of the camera; the mounter's image recognition system searches for the register mark - usually trying to match a register mark on the plate to a pre-selected register mark in the image database. Once it recognizes the register mark, the ‘actual’ position is compared with the ‘target/pre-programmed’ position. This positional data is sent to the mounter's computer which in turn sends instructions to the mounter's drives/motors to move the plate to the correct position. Different manufacturers have different systems for doing this positioning, and with different margins of precision.
Once positioned in the correct mounting position the mounter automatically sticks the plate to the pre-taped sleeve, usually with a pressure roller to eliminate air bubbles between the plate and the tape. Different manufacturers do this in different ways, but the result is plates that are mounted automatically with little or no operator interference, with great accuracy and with consistent, repeatable results. These same mounters also have systems to check the accuracy of the mount. This automation follows the trend of automation and data exchange in manufacturing technologies, as is the philosophy of Industry 4.0. As the operator's variable input is eliminated, and it is the machine mounting automatically, this reduces or eliminates the need for re-mounting.
Automatic mounters work by using different methods and algorithms in image recognition, from the most basic systems that take a photo/frame of an image and search for a near-perfect match, to those that use more sophisticated methods to identify a wider range of register marks. It is important to note that the more basic ‘photo-matching’ systems work well in situations where there is very little variation in the registration mark and its surrounding area. However, in practice, especially with the smaller register marks and used plates, these methods are limited and more complex algorithms based on synthetic target models and multiple matching systems are required to ensure consistent image recognition across a reasonable range of ‘real life’ used registration marks. If one can only use new, perfect plates with large register marks, then this is not a real-life scenario in a flexographic printing factory.
The different image recognition systems and software to identify, recognize and match the database of the different register mark/microdot types is crucial – if the automatic mounter does not recognize the target, it cannot be automatically mounted and has to be done manually, or the register mark model has to be entered into the mounter's database manually, which reduces automation and increases mounting time. The precision to which the system recognizes the registration mark is fundamental, because, if the recommended tolerance by the manufacturer is 0,6mm, for example, but the registration marks of the plate are 0.3mm, as is the case in many plates, the automatic mounter does not recognize the register mark of the plate and it cannot be mounted automatically. Therefore, the smaller the tolerance of the recognized register mark size, the better. The Heaford ‘Label AutoMounter’ automatic mounting machine, for example, recognizes down to 0.25mm register mark diameter.
Also, the type of register mark or microdot can affect its recognition, or not, depending on the technology. In discussions with the technical department of a leading plate manufacturer, they reported that in mid and wide web applications most of their customers now use negative microdots, and although these are typically larger, the tolerances of each manufacturer are still the difference between a truly automatic mounting machine and one that has to be stopped for the mounting machine to be reprogrammed to recognize the register mark. With negative microdots, some automatic mounters recommend 0.6-1mm minimum microdot diameter, while the Heaford AutoMounter recognizes down to 0.40mm diameter negative microdots. Although in the label industry register crosses are more common than microdots, ensuring an automatic mounter can automatically mount smaller register marks is essential.
The other big advantage of automatic mounting machines over traditional mounters is that while the mounter is mounting a plate, the operator can do other tasks in the pre-press process, such as preparing subsequent jobs or removing used plates from a used sleeve. These tasks are important when we determine ‘mounting times’, because mounting time is not only the physical time to mount the plate, but also the time needed for each step of the process, such as removing used plates, cleaning, preparing plates, taping the sleeve, entering data into the mounter for jobs or recalling repeat jobs, mounting of the plates, and transferring the mounted plates to the press.
Critical work
Antonio Oliveira of Prakolar Rotulos Brazil (part of the Sato Group), which installed an AutoMounter in 2018, says: ‘Today, my operators do not have to worry about the precision of the mounting to be done, they only have to position the plate in the machine and, while the AutoMounter does the critical work, they can prepare the other elements in the process.’
Many customers around the world have invested in this type of automatic mounting, and although they have a higher initial investment, they typically have a return on investment of approximately 12-18 months, as they significantly reduce or eliminate re-mounts, stopped printing presses, whilst enabling faster job start-up and increasing the efficiency of their operators. Antonio Oliveira comments: ‘We have drastically reduced the number of remounted plates, all plates are accurately mounted together, preventing remounting and helping us to achieve better color matching for critical registration jobs.’ In Prakolar the AutoMounter replaced three traditional mounting machines, and also reduced mounting times by 20 percent.
These time savings can be even greater. E-Z Stick Labels of Santa Fe Springs, California, which also installed a Label AutoMounter in 2018, has achieved a 75 percent reduction in plate mounting times since its installation. According to owner Richard Martinez, it is already saving about 50 hours of work per week.
One of the important features in the use of automatic mounting machines is their ease of use. Richard Martinez says the ease of use of the Heaford AutoMounter was the first big surprise. ‘I think the slogan at the show was something like “so easy to use your boss can mount”. I assumed those were just marketing words, until I actually used it,’ reports Martinez. ‘Actually, everyone in our factory has been trained in how to use it. We've been using it since day one without any dedicated operators and it has been absolutely accurate each and every time.’
It is this repeatability and operator independence that attracts label manufacturers to this technology, as reducing remounts and increasing productivity of operators leads to a faster workflow. So, if you are thinking of investing in a new plate mounter to service multiple presses, either cylinder or sleeve based, automatic mounters should be considered in your capital expenditure.
For further info:
JM Heaford’s Label AutoMounter will be on display at Labelexpo Americas 2022 in Chicago
Stay up to date
Subscribe to the free Label News newsletter and receive the latest content every week. We'll never share your email address.