Barcom aces expansion strategy
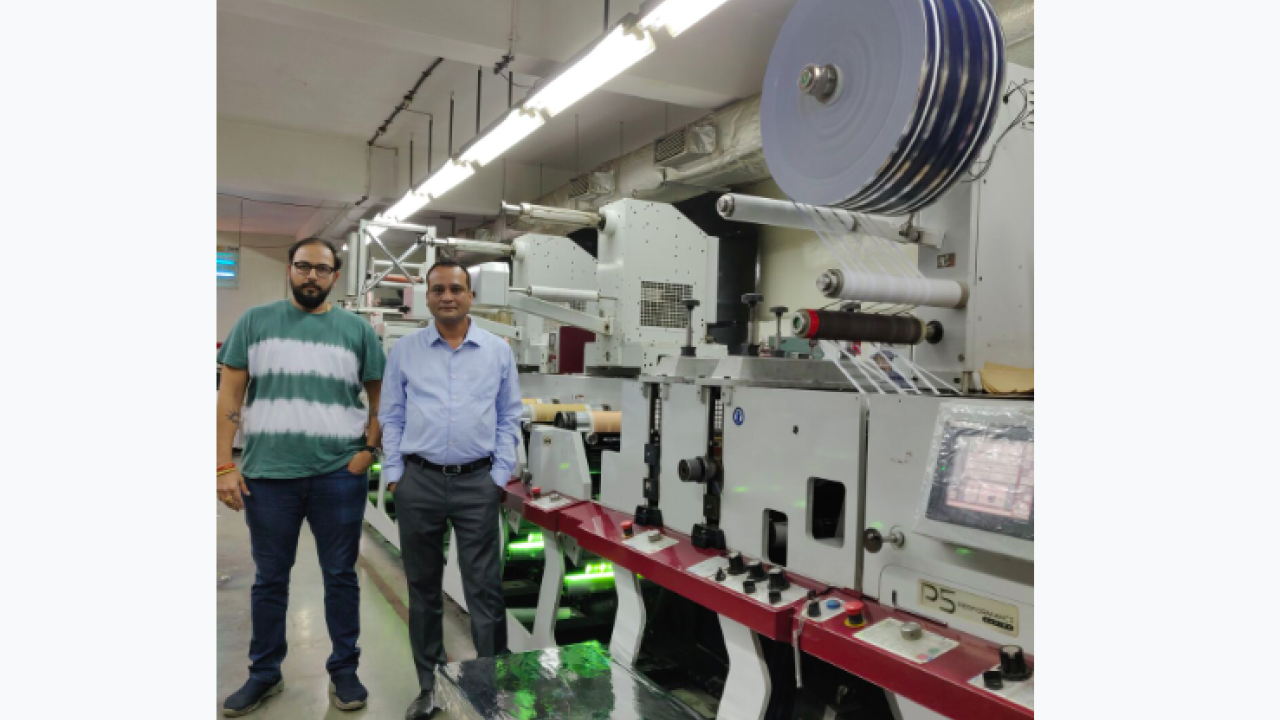
Prasanna Sahu, chairman at Barcom Industries, says: ‘We are growing with our customers because of the service we provide them. Label printing is a service-oriented industry and we don’t hesitate to dedicate a press to the job of our customers, if required.’
Barcom Industries was established in 2002 as a trading company and started printing labels in-house in 2004 on a refurbished 4-color Mark Andy 830 press alongside an off-line flatbed punching machine from Ondo. The first new press at Barcom was a 7-color Mark Andy Scout in 2006. ‘There has been no looking back ever since. We have been expanding capacity by installing a press almost every year since,’ says Sahu.
The company today runs ten Mark Andy presses that include an 830, a Scout, three 2200, four Performance Series P5, and a Digital One machine. A new inkjet press from Monotech Systems was also installed in 2019.
Alongside the presses, it runs a fleet of finishing and ancillary equipment including eight Rotoflex inspection slitter rewinders with 100 percent defect detection system. These include four Rotoflex HSI with horizontal orientation and one bi-directional inspection machine mainly for pharmaceutical labels, an array of punching and counting machines, and off-line hot foiling machines, among others.
Recent investments
Barcom was the first company in Asia to install a Mark Andy Digital One press in 2018. ‘We print short run jobs on this press to deliver them faster and free up flexo capacity. Not to mention other advantages that digital printing offers such as eliminating several processes including the need of making plates, registration, color matching, reduced wastage, time, and it requires less labor,’ says Sahu.
Gauging market demand and to further expand its capabilities, the company opted to invest in inkjet technology at Labelexpo India 2018 and chose Monotech’s Jetsci Colornovo UV inkjet press. Installed in June 2019, it is a CMYK+W machine that features a flexo unit, varnish station, lamination, cold foil, semi-rotary die-cutting and a slitter unit with dual rewind.
‘Colornovo prints variable data with value addition on short to medium run jobs which is required for security printing and other jobs. The inkjet head also allows ink deposition of more than 30gsm that enables a screen effect on a label. This decoration technique has made a comeback in the label industry and has a great value on short run labels with variable data,’ Sahu explains.
While catering to several industries including FMCG, liquor, lubricant oil, agrochemicals, barcoding, and pharmaceutical, among others, Barcom prints about one million sqm of labelstock a month. It now aims to increase its market share by diversifying to printing in-mold labels (IML). While labels can be printed on its existing presses, the company has made further investment in IML slitter rewinder, die-cutting and sheet cutting machines.
To cater to these ever-growing volumes more efficiently, Barcom opted for a Colorsat Match, an automated ink dispensing machine by GSE with automatic proofer in October 2018. ‘We mix about 2,500kg of ink a month with delta value of less than three. This system has reduced our ink wastage by 80 percent, resulting in huge savings and making our ink kitchen very efficient and quick,’ reports Sahu.
Barcom is one of the few companies to have designated areas for UV inks and water-based inks. It uses food grade water based inks mainly for food and pharmaceutical industries and UV inks for all other jobs. Segregating the areas ensures high quality and smooth workflow.
‘We offer low migration labels by not only using low migration inks but also separating labelstock used for different applications, printing on discrete presses, and even changing the air flow in the plant,’ details Sahu.
Barcom is also developing its customized ERP system to link all its departments. ‘Authorized personnel in each department will have access to the ERP that will not only centralize all information but will also provide real time job status,’ says Sahu.
Job security
The company opted to have pre-press infrastructure in-house that includes Esko CDI 4835 along with software including Esko’s Packedge, FlexoTools and FlexRip and DuPont Cyrel Fast Thermal Workflow for plate finishing.
‘With pre-press support, we can cater to customers’ demands in the shortest possible turnaround time and at a competitive price. More importantly, our customers trust us with their job security and quality. We are an ethical company and do not take any chances with exposing jobs for counterfeiting. We constantly work towards making a good reputation and cementing trust in our customers which has enabled our fast growth,’ says Sahu.
In line with this commitment, Barcom shreds all its printed waste in the factory, compacts it in a brick form before sending it for disposal. ‘We are a certified supplier for labels in the US, which requires shredding waste for security purposes,’ says Sahu.
Security is increasingly becoming a critical aspect in the label printing business. While brand owners demand shorter lead times, high quality print and value addition, anti-counterfeiting solutions are becoming a key part of Barcom’s portfolio. ‘Therefore, we do our best to print with latest techniques and use security inks and labelstock. We even sign a tri-party bond for certain materials to safeguard the interest of our customer,’ says Sahu.
Continuing to make investments in this direction, Barcom has installed a Nikka ODRI scanner inspection system that checks text from the PDF sent by the client before it is sent for printing. At 600 or 1,200 DPI, the ODRI software can detect very small defects such as missing accents, i dots and misprints in foreign languages including Japanese, Chinese and Arabic. It can even detect pre-press errors and print defects, thereby reducing waste.
‘Efficiency, quality, credibility and service are important to remain relevant and profitable in this industry and we are leaving no stone unturned to ensure just that,’ says Sahu.
From being a trader to a barcode printer to being one of the top printing companies in India, Barcom continues to evolve into a smarter company that understands the market evolution. ‘We have been careful to partner with suppliers who help us move in the right direction with their continued service and support,’ concludes Sahu.
Stay up to date
Subscribe to the free Label News newsletter and receive the latest content every week. We'll never share your email address.