Bobst launches Digital Master series
Following on from the DM5 ‘all-in-one’ format digital press, Bobst has launched the next generation machine, the Digital Master in web widths up to 510mm.
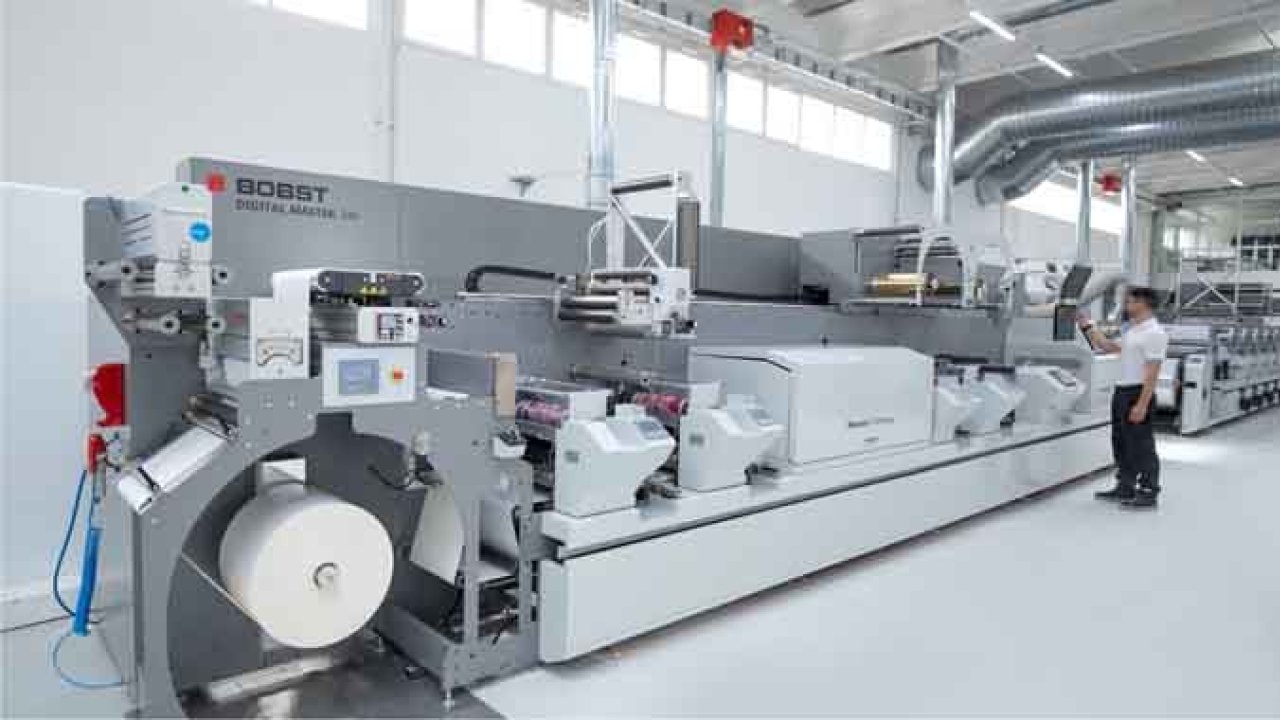
Leveraging its proven flexo experience and recent innovations in inkjet development, Bobst has enhanced its in-line portfolio with the new Digital Master press series. Available in two web widths, 340mm and 510mm, the Digital Master is designed to be a fully digitalized and automated production line, from printing to embellishment and cutting. The Digital Master presses are based on a fully modular and upgradeable architecture, enabling customers to build their own press and evolve it over time.
‘Developments in label production are moving at pace with brand owners looking for converters that have the ability to deliver faster, better and at more competitive prices,’ says Bobst strategic marketing manager Patrick Graber. ‘In this context, the Bobst All-in-One platform is a great answer as digitally printed labels can be produced in high quality, with exceptional productivity and at lower costs, from short to long runs.
‘With the Digital Master series, we want to solve our customers’ challenges as they try to overcome the lack of skilled workforce while moving to industrial productivity and longer run lengths with digital equipment; and to bring more agility and flexibility to the production floor.’
The Digital Master series will be available in 340mm (13.5in) and 510mm (20in) widths, printing at a native resolution of 1,200 x 1,200 DPI. The Digital Master presses run at speeds up to 100m/min (328ft/min) in four or six colors plus optional digital white.
Like the Master DM5 it supersedes, the Digital Master offers printing, embellishment and cutting in a single pass, with native integration between the UV inkjet engine and the flexo and converting modules. The introduction of a 510mm version adds new opportunities to expand application versatility into larger-sized labels, industrial and chemical markets, wraparound, shrink sleeves, and other special applications.
Adds Graber, ‘The Digital Master 510 provides higher production volume but still only needs one operator to run the press. The press really bridges the gap between traditional digital and flexo machines. The Digital Master series stands for flexibility, fast turnaround, and inline end-to-end label production, with exceptional quality and productivity in increasing run lengths.’
Modular architecture
The modular architecture of the Digital Series presses allows customers to configure the machine they need, from a digital-only version to highly customized configuration integrating all modules available in in-line flexo. ‘It also provides the possibility to be upgraded on-site at a later stage when new technologies for these platforms are released,’ says Graber.
Typical applications for the flexo modules include priming demanding substrates, high-ink coverage jobs for long print runs to save on digital ink, applications with high white coverage, or for printing Pantone colors. Available embellishment features include varnishing, tactile and holographic effects, cold foil glue-applied, UV lamination, and security printing.
For end-to-end label production, fully automated semi-rotary die-cutting or rotary die-cutting are ready for integration. The semi-rotary die-cutting module has a repeat range up to 17in, while the rotary die-cutting module allows for full converting options such as embossing and sheeting.
The introduction of a 510mm version adds new opportunities to expand application versatility into larger-sized labels, industrial and chemical markets, wraparound, shrink sleeves, and other special applications
Also available are modules for special applications including multi-layer labels, back-side printing, coupon and others. ‘Each print, embellishment and finishing module is digitally automated for high uptime, low waste, and repeatability regardless of the operator’s skills,’ continues Graber.
Quality control is handled by the inclusion of a Bobst Accucheck 100 percent in-line inspection system operating at full press speed. This technology checks registration, quality, and color consistency of digital and flexo print and all embellishments including foil and varnish.
The Accucheck system detects a broad range of print defects including spots, streaks, missing text, color variations, registration errors, substrate integrity and double printing. It also incorporates missing jet detection.
To maximize productivity during longer runs the presses are fitted as standard with 1,000mm (39in) jumbo unwinders and rewinders with automated roll-lift to reduce the number of roll changes. A single interface controls the whole machine, which can be connected to the Cloud and is open for MIS integration.
Other standard equipment includes web cleaner, corona unit, web-guide, simplex mark reader for second pass printing, splice detector, chilled roller and maintenance automation system along with Digital Front End server for fast data processing.
Stay up to date
Subscribe to the free Label News newsletter and receive the latest content every week. We'll never share your email address.