Coating and lamination
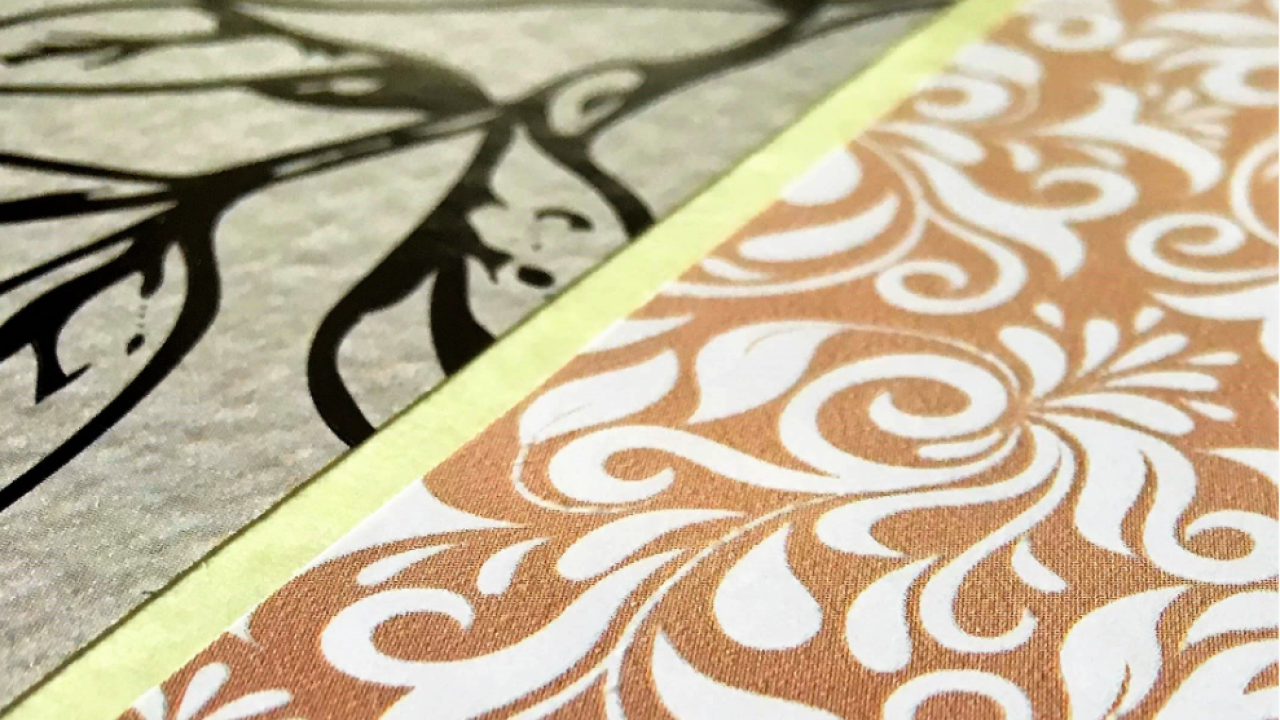
The task of the label is not only to inform but in many cases also to meet legislative requirements which must be legible right through the life-cycle of the label. The label must also be capable of being used in high-speed labeling machines working at mind-bending speeds to satisfy consumer demand for everyday products. This is where the surface of the label needs protection, be it manufactured from paper or film substrates, and where coating and lamination technology is vital in performing these functions. Pretty straightforward you might think – but don’t forget about disposal after its main function is completed: recycling is equally as important as the main use of the label.
This article looks at the different technologies which are used to protect or embellish labels and packaging along with a typical machine for applying the coating or laminate.
Coating technology
A coating is basically designed to protect a label from damage by scuffing or friction during its useful working life. In addition many different finishes can be applied to the label to enhance its appearance and attract the consumer. These specialist coatings can come in several surface finishes including gloss, matte, glitter and sensory applications etc. They can be used to highlight specific areas of a design by using spot varnish techniques. A practical application in the pharmaceutical industry is the provision of raised Braille characters. Other applications include adding covert security protection for high value products to prevent counterfeiting.
Two companies providing a wide range of coatings for the label industry are Lintec Corporation and Pulse Roll Label Products. Lintec offers coatings for a wide variety of uses including protection from damage during the life of the label and UV protection. It also produces a wide range of adhesive formulations which can be used in release liner production.
Narrow web ink specialist Pulse Roll Label Products manufactures coatings and varnishes for label printing to suit requirements which range from decoration and embellishment, to functionality and compliance.
Complementing its flagship UV flexo ink system, PureTone, the company also formulates specialist UV flexo coatings and varnishes. These products include its well-established PurePeel peel and read release varnish, its PureFX rough texture matte varnish, launched at Labelexpo Europe 2017, and its PureFinish UV flexo varnishes formulated for the overprinting of digital inks.
Coatings for functionality
The market for peel and read labels has grown significantly over recent years, fueled by regulatory demands for extra information required on labels particularly in sectors such as pharma, healthcare, cosmetics and household and industrial products.
Multilayer labels are suitable for application on a wide range of packaging, containers and bottles, and provide additional surface area on a pack allowing extended content without sacrificing branding, graphics and shelf appeal. From a coating perspective, it is critical that the adhesive used on this type of label allows the layer to be easily peeled, released and resealed on a ‘repeatable’ basis.
Mikaela Harding, product manager, Pulse Roll Label Products, says: ‘Our PurePeel UV flexo release varnish is used by narrow web printers worldwide and provides proven smooth, even and repeatable release properties. Ten years after its launch, this continues to be the release coating of choice for many leading label manufacturers.’
With the continued growth in digital label printing, UV flexo varnishes are often used for overprinting digital inks and require high resistant properties to protect the print underneath. Gloss and matte varnishes are widely used and other specialty varnishes are becoming increasingly popular as companies seek to embellish and finish digitally printed labels to create eye-catching and interesting effects.
Coatings for premium effects
In addition to products developed primarily for functional purposes, advancements in varnish technology, press technology, plates and anilox rollers have enabled label coatings to become highly sophisticated in the way they are applied and the striking effects that can be achieved.
The days of a simple flood coat varnish on a label have been left far behind, with high quality products emerging today ranging from high gloss and super matte to soft touch and rough texture coatings. A combination of different spot varnishes, for example, can create many contrasting and attractive effects, adding value to a brand by enhancing shelf appeal via its label. Increasingly, brand owners are differentiating their products by incorporating sensory packaging that engages with the consumer.
The growing popularity of craft beer and gin, artisan products and other specialty food and drink products, in particular, appears to have influenced the label industry trend towards the use of specialist varnishes and coatings for decorative and embellishment purposes. Sarah Harriman, marketing and communications manager, Pulse Roll Label Products, comments: ‘We have seen a surge of interest in label varnishes and coatings which create premium visual and tactile effects. Specialist coatings are being used more and more to boost brand appeal and help to make a product stand out on the shelf. Tactile effects are proving particularly popular. Our PureFX UV flexo rough texture varnish was formulated to satisfy this need, as brand owners focus more on delivering a touch and feel experience to the consumer.’
Mikaela Harding adds: ‘It’s important for us to support our customers in delivering outstanding quality and optimal performance on press. To achieve this, when we develop a new coating or varnish, we work closely with other industry suppliers including anilox companies, repro houses and plate manufacturers. Our collaboration with industry experts such as Creation Reprographics and anilox manufacturer Sandon Global, for example, means that we can help to deliver the highest-standard print solutions for our customers and their customers, the brand owners and retailers. These partnerships add real value as we bring together knowledge and expertise from leading industry suppliers to provide high quality coatings and varnishes.’
As finishing technologies become increasingly advanced, one can expect to see further developments in high quality decorative label embellishments and the creative use of varnishes and coatings for increased brand appeal.
Lamination technology
Why laminate a label? What are the advantages? Lamination (or over-lamination) is normally associated with totally encapsulating a printed or non-printed label to offer robust protection against damage by friction, scuffing, aggressive liquids and challenging environments. No matter in which application segment the label is to be used, there will always be an element capable of damaging its surface. Take for example household products, where fairly aggressive liquids might be spilt on the label surface. Or cosmetic labels, which are subject to damp and moist conditions. In both cases the label must be protected from damage by wet hands or continuous attack by hot water. Then again, labels which are used outdoors need the most protection as they are exposed to intense UV radiation from the sun, heat in the summer and freezing conditions in the winter including snow and ice. Meanwhile, at all times during the life-cycle of the label important information must be preserved, such as conditions of use and safety information. All of this means that over lamination of a label with the correct final surface is crucial.
Most people are familiar with the domestic lamination equipment which can provide basic film protection for a poster or notice from damage and normally has a glossy finish. In the world of professional over-lamination many different surface finishes are available as well as various film qualities which have properties designed to protect the surface of the printed label as well as the actual printed information.
Methods of application of the laminate include: thermal lamination, where the laminate is bonded to the substrate using heat and pressure; aqueous adhesive, eliminating solvents from the coating area; silicone adhesives, when special release properties are required such as a peel and reseal; UV-cured adhesives; acrylic adhesives, for applications where a high level of adhesion is required or where overprinting of digital printing is important.
Polypropylene is currently the most popular lamination film and is the least expensive. It has excellent clarity and can be supplied in a 2mil thickness. The surface can be modified to improve ink adhesion of overprinting is required. The laminate provides an excellent solvent and abrasion finish.
Polyester is widely used and protects the label surface from abrasion, oils, chemicals and solvents. Again it can be supplied in a 2mil thickness using a pressure-sensitive adhesive. Thicker films are available which give improved dimensional stability and can even offer more protection for outdoor use. Other uses of polyester include top coating to accept thermal transfer printing and a special coating product designed to protect the label from high levels of UV experienced outdoors and subsequent fading.
The surfaces of both these laminate films can be supplied in clear or matte finishes and with the introduction of new super clear adhesives gives added clarity to the finished label. This clarity is extremely important so that barcodes at checkout tills can be read easily and quickly.
Summary
Almost gone are the days when a plain paper or film label can be seen on a typical supermarket shelf. Some form of protection has become necessary, beginning with the application in a fast-running labeling line through to transporting the tin or pack to the supermarket shelf. Who wants to buy a product with half the information about the product missing? Even when the customer takes the product off the shelf, deposits it in a metal shopping trolley, takes it home and stores it in a cupboard or uses it in the kitchen or bathroom, the vital information must still be legible. This is even more important with pharmaceutical products where information on the pack is vital.
The use of coating or laminating technology has become an integral part of everyday life. The label which has been enhanced by the use of discreet coating finishes often acts as persuader for making the purchasing decision. The future of both technologies is set to expand and develop with new applications and new barrier properties being offered.
Article was written by Tony White, L&L’s new technical editor, Labels & Labeling.
Stay up to date
Subscribe to the free Label News newsletter and receive the latest content every week. We'll never share your email address.