Deji invests in new Omet press
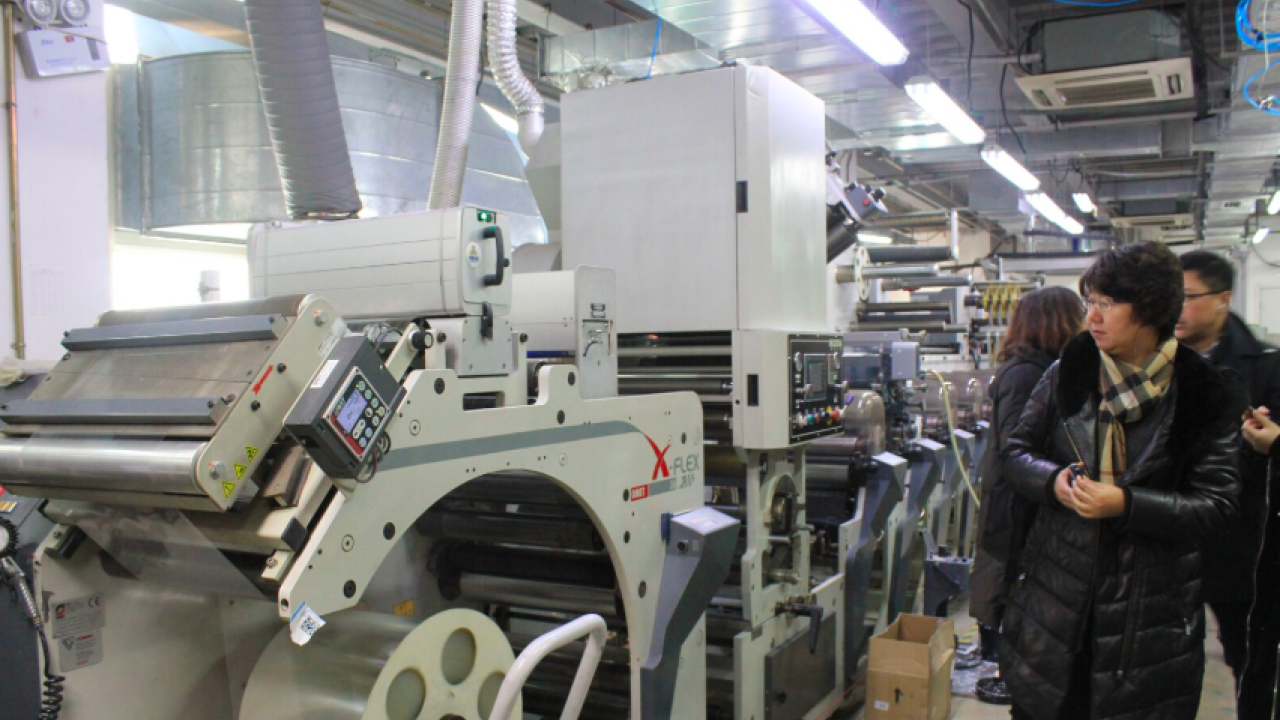
The company installed its first Omet XFlex in 2013. It will receive its second in April – an investment which emphasizes Deji’s success at a time of slow growth in the Chinese market, and founder Yu Dayang’s optimism about a potential upturn. Thanks to the rising cost of raw materials and pressure brought by new environmental regulation, many local converters are struggling to maintain the status quo, rather than investing in new facilities and high-end machinery.
‘We have also had our low moments in recent years,’ says Yu Dayang, ‘but as someone who has worked in the field for more than 20 years, I am very optimistic about the future development of the Chinese label printing market. As long as you can make good use of them, current challenges can be converted into opportunities.’
This confidence is evidenced by the investment in a second Omet Xflex X6, and shows the company’s determination to increase productivity and create high quality work for its customers.
‘The installation of a second Omet XFlex flexo press meets our growing production demands,’ explains Yu. ‘Equally importantly, it allows us to schedule work between the two machines for more efficient production, avoiding bottlenecks and having a back-up if there is a problem with one press. It is also a significant boost to our supplying better, quicker and more responsible services to our customers. The press offers international-level quality as well as security and speed during production.’
Dario Urbinati, managing director, China and Southeast Asia for Omet, says: ‘The XFlex X6 is one of Omet’s most representative machines, especially in its incomparable performance in material and labor savings, automation and intelligent control. We hope that Deji will make full use of the press, not only as a printing tool, but also as a way of increasing the automation of its processes.’
The Omet XFlex X6 can handle almost any type of substrate used in the production of labels and packaging. In addition to producing pressure-sensitive labels – Deji’s core area of business – the press can print on unsupported film down to 12 micron.
According to Yu Dayang, Deji is investigating the markets for shrink sleeve, wraparound and in-mold labels. ‘We will learn from Western enterprises and address our weaknesses in short and medium run printing with the support of the XFlex X6’s capabilities,’ he says.
Quality
Established in 2004, Deji specializes in printing high-quality self-adhesive labels and digital anti-counterfeit labels. R&D, design and production are all integrated in its new 4,000sqm plant, located in Yongle Industrial Park in Beijing’s Tongzhou District, which hosts 70 employees.
Deji’s labels serve a wide variety of industries, including electronics, chemical, pharmaceutical, wine, food and beverage. It produces 3 billion labels a year, and counts Maotai Group, Red Star Wine, COFCO Wine, JNC Group, Sony, Junlebao Dairy and Tongrentang among its clients.
Yu Dayang says Deji owes its success to investment in high-level technology, and its rigorous adherence to quality, environmental and governmental standards. Apart from the two Omet presses, Deji runs a Nipson digital press, 9-color and 12-color letterpress machines, Esko pre-press software and equipment, Luster LightTech inspection, and an RFID insertion system. Its scope extends from conventional printing to variable data printing, RFID label production, digital information management and the production of anti-counterfeiting products.
Deji has been granted governmental licenses and certificates for industrial production, printing, adherence to environmental standards, barcode printing and anti-counterfeiting technology, as well as achieving ISO 9000/14000 quality and environmental standards. It has a number of patents, including for anti-tamper packaging and package sealing.
‘The economy in China has entered a new normalization phase and the label industry is also experiencing great changes,’ says Yu. ‘A company must reform itself and adapt to trends in order to find its own way to growth.
‘The introduction of the second Omet press, and the exploration of technical topics in our seminar are important parts of our reformation. Deji will build a digitalized and automated workflow, and a safe factory with high quality production.
‘Our development comes under strict industrial policies and amid fierce local competition, and so implies our customers’ trust in us. We must set a good example and contribute to the national dream of invigorating the country through industry.’
Preparation
The seminar at Deji’s factory served as preparation for the installation of the Omet XFlex X6. Partner suppliers hosted technical brainstorming sessions to advise on various processes, including image processing, platemaking, surface treatment, printing, inspection, temperature and humidity control and more.
‘The idea for the seminar was inspired by our customers,’ says Yu. ‘Nowadays, the quality demands from end users are increasing. The converter must take all steps of production into consideration. We provide design services to customers, and then discuss with them the overall packaging solution they require and to analyze the market. We are not only a label converter: we can provide many practical suggestions based on our production experience.’
The suppliers present told attendees about the technology they had provided. Marco Yang, application engineer at Esko, described how the pre-press expert had supplied a fully automated pre-press management system to Deji. Addressing the converter’s move into printing films, Wang Yu, general manager of Beijing Webcon Science &Technology Development, and Henry Ma, general manager of Beijing Dynabond Tech, provided practical advice on surface treatment.
Qiao Yingzhe, product planning department director at Luster LightTech discussed how in-line and off-line automatic inspection can lower the rate of product defects and reduce labor costs. Jimmy Cao, sales manager at SPGPrints, talked about the silkscreen unit his company had supplied on the Omet press. Tianjin Jiejing Engineering drafted a customized solution for creating a dust-free environment at Deji’s facilities.
After the seminar, Yu Dayang expressed his satisfaction. ‘By surveying industrial experts in this way, we are trying to connect the label printing supply chain in order to be able to react to different trends in the future. With regards to the layout, configuration and construction of the new workshop, we are confident about achieving better, more efficient and more secure services to our customers.’
Stay up to date
Subscribe to the free Label News newsletter and receive the latest content every week. We'll never share your email address.