Selling the sheet-fed digital package
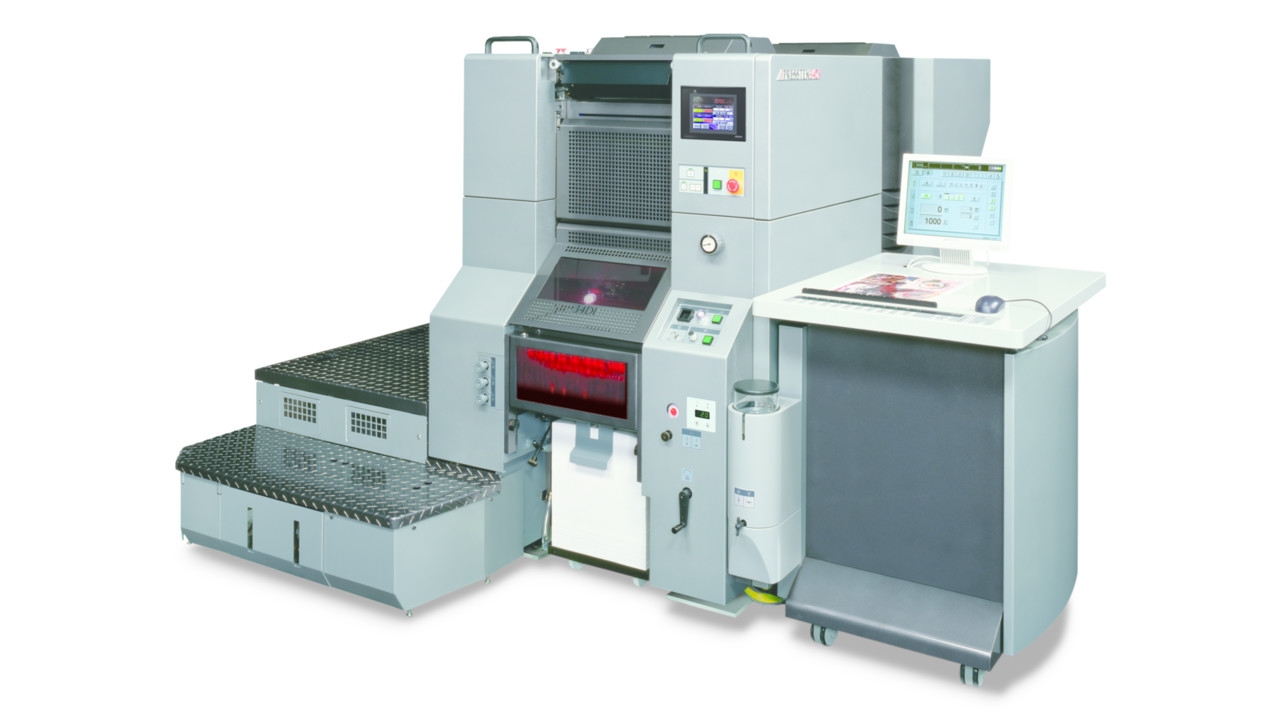
Label converters pay scant attention to sheet-fed digital printing. Some may recall it kick-started the concept of print-on-demand in respect of booklets, manuals and similar documents. Yet, over the years, various imaging technologies have ensured its place not only in full-color commercial printing, but also in several package print markets. This influence may expand still further with the latest page-wide UV inkjet presses.
The story really begins with drupa 2012, when several prototype sheet-fed UV inkjet presses appeared, notably from Screen, Fujifilm, Konica-Minolta, MGI and Delphax. Four years on and several of them have reached commercial fruition. Crucially, the uncertainties surrounding their ability to compete with toner-based printers, and HP Indigo’s liquid ink system, in terms of print quality and operating speeds, seem no longer an issue.
Again, the current showcase was drupa, but this time with an increased emphasis on package printing following the noteworthy input of such leading offset-litho press manufacturers as Heidelberg, Komori and KBA. They supplied the press platforms and sheet handling technology for new inkjet models, while their OEM inkjet partners developed new single-pass printheads and control systems.
The press manufacturers see these joint ventures as key to ensuring their long-term future. While successfully involved with package printing, their mainstream commercial print markets are declining, or about to disappear. There is a parallel here with what happened in the business forms and direct mailer markets from the mid-1990s, albeit from a web-offset perspective. By contrast, the disruptive effects of the internet, online shopping and other computer-based activities have hardly affected the packaging industry.
With a growing short-run dynamic now in play, sheet-fed UV inkjet is considered as an expedient way of handling it, while helping end-users reduce inventories and minimize waste. Equipped with variable data and encoding facilities, the latest inkjet presses also offer versioning and customized packaging.
So while the traditional offset, flexo and gravure processes will remain essential for longer runs, further advances in digital press speeds, substrate sizes and overall flexibility will erode their commanding role. Arguably there is a two-edged sword here: these benefits could encourage more brand owners to set-up their own digitally-based print services in-house, especially where reconciliation of the packaging with the product is absolutely vital.
Technically, the new inkjet presses offer a near-perfect synergy: most are B2 format models with maximum sheet sizes of 500 x 707mm (19.6 x 28in). Nearly all can print carton board, while some print directly to micro-flute corrugated board or sheeted films for flexible packaging. Backed with suitable cutting and creasing equipment, press owners can produce small folding cartons for the cosmetics, food, luxury goods and pharmaceutical sectors in short-to-medium run lengths. The same press could print the leaflets for consumer information or mandatory pharmaceutical data.
Arguably wet-glue (glue-applied) labels are on the menu, however the run lengths would have to be considerably smaller than those required for supplying cut labels for application on high-speed filling/ bottling lines. The global growth of semi-automatic wet-glue and hot-melt label applicators for labeling pharmaceutical vials and similar round containers offers a possible market. Other applications could include customized or versionized cut-and-stack film labels, in-mold labels and sheeted pressure-sensitive labels for, say, premium wines and spirits, or point-of-sale applications.
Long before UV inkjet became acceptable for good quality package printing, it’s worth noting that HP Indigo’s sheet-fed models helped pioneer this sector. The current top-end model, the 30000 B2-plus press, prints carton board with a seven-color ink set at up to 4,600sph. Other models in the series also produce short-run cartons, flexible packaging, swing tags and similar products. Interestingly, one of the first European users of the 7-color HP Indigo 12000 B2+ press is a commercial print group. Nava Press, part of the Rotolito Lombarda group in Italy, installed it to augment its existing HP Indigo 7800 and 10000 presses. The company not only prints commercial products, but also short-run packaging for luxury goods and cosmetics.
This crossover is also apparent with Presstek’s plateless four-color direct imaging (DI) presses. They print on substrates ranging from thin films up to carton board. They are said to offer printers a smooth transition into package printing, and seemingly end-users too: a Californian bottler of mineral waters uses a DI press to produce in-house customized cut-and-stack filmic labels.
Not only is there more emphasis on package printing, firms outside the converting industry are also taking note, as are industry commentators. Dr Harvey R Levenson, professor emeritus and former department head of Graphic Communication at Cal Poly State University in California, is one of them. He highlights the singular growth of package printing when compared with traditional print segments in a white paper entitled ‘The lure of digital packaging: a growth area in the printing industry’.
‘The growth and focus on packaging by OEMs and service providers (printers) is a statement on the viability of the industrial, capitalist and market-driven material interests of the western world, and is rapidly becoming a value in Asia and elsewhere,’ he observes.
This societal value is nothing new, he adds, stating that it explains why nearly every digital press vendor now focuses on packaging. He cites the Smithers Pira 2013 report, ‘The Future of Digital Print for Packaging to 2018’, which links population increases and income growth in industrialized regions with increased packaging growth.
Geographically, Europe/Middle East/Africa (EMEA) and North America are the largest markets for color digital label and packaging presses. Asia-Pacific and Japan, and the rest of world, are the smaller but faster-growing regions. Meanwhile, in more developed regions, average household sizes are falling, reducing the size of average print runs and, therefore, playing to the strengths of digital packaging. The report says the estimated worth of digitally-printed packaging in 2013 was 6.6 billion USD, and is forecast to reach 14.4 billion USD by 2018.
Sheet-fed inkjet technology
As unveiled at drupa, the partnership between Heidelberg and Fujifilm yielded the Primefire 106, based on the larger B1 format (700mm x 1,000mm) Speedmaster XL 106 packaging press. (‘Fire’ is the umbrella name for Heidelberg’s digital products, such as Labelfire the former Gallus DCS 340 press and the Versafire CP/CV dry-toner series developed with Ricoh.)
The Primefire 106 uses Fujifilm’s Samba piezoelectric print bars printing CMYK, orange, green and violet to cover 90+ percent of the Pantone color space with four levels of grayscale at a native resolution of 1,200 x 1,200 DPI. Top speed is 2,500 sheets/hour, printing carton board up to 0.8mm thick using food-safe inks. It includes Heidelberg’s Prinect Digital Center Inline with Perfect Stack technology to ensure the delivery of good sheets. Combined with the Prinect digital front-end, the press is said to offer seamless integration within the user’s existing overall workflow. Operators can output test sheets directly to the control panel at the push of a button for visual quality checks.
Fujifilm’s own J Press 720, introduced in 2012, popularized the concept of sending ripped PDF files directly to the press without requiring plates or make-ready for short-run work. The upgraded J Press 720S version prints most uncoated and coated offset stocks to a maximum sheet size of 533mm x 748mm (21in x 29.5in) using Samba print bars. The top speed is 2,700 sheets/hour. (As widely known, Fujifilm has a commercial link with the Graphium hybrid inkjet roll-label press from FFEI, which uses Xaar’s printheads.)
Komori’s partner is Konica Minolta, whose latest MEMS printheads are integrated in the four-color Impremia IS29 press. With a native resolution of 1,200 x 1,200 DPI, the IS29 prints on standard stocks for commercial print and package printing applications to a maximum sheet size of 585mm x 750mm. A simplex and duplex capability offers respective speeds of 3,000sph and 1,500sph. Post-press equipment includes the Komori Appresia CT115/CT137 programmable cutter and DC105 die-cutter for packaging products.
Komori also offers the innovative Impremia NS40 digital press, which uses the long-awaited nanotechnology print engine developed under license from the Landa Corporation. The B1-sized press prints carton board at up to 6,500sph.
Konica Minolta’s own 4-color AccurioJet KM-1 has a similar B2+ format for commercial and packaging print, including cartons. Order processing, file handling and material stock control on the KM-1 is through cloud-based web2print technology from Vpress while an integrated Tharsten MIS creates the production workflow. It prints up to 3,000 sheet/hour in simplex mode using offset coated and uncoated substrates, including textured grades, to a sheet thickness of 0.6mm, with LED curing.
Konica Minolta recently increased its financial and technical stake in MGI Digital Technology. Its Jetvarnish 3DW spot UV varnishing, hot-foiling and embossing system (which was shown at Labelexpo Americas) can integrate with the KM-1 (as well as with KM’s new bizhub C71hc SRA3 sheet-fed inkjet commercial press). The Jetvarnish 3D Evolution is a B1+ version. MGI also supplies the established Meteor DP series of toner-based digital presses, which have a multi-substrate capability, including carton board.
KBA Sheet-fed Solutions, part of the Koenig & Bauer Group, markets its VariJet 106 to folding carton printers. Based on the KBA Rapida 106 offset press it runs with integrated Xerox’s Impika inkjet technology and High Fusion inks. The B1+ format gives a sheet size of 750mm x 1,060mm (29.5 in x 41.7in) and the top speed is 4,500 sheets/hour. Optional in-line capabilities include coating, cold foiling, rotary die-cutting, creasing and perforating.
First shown at Ipex 2010, the B2 format Truepress JetSX from Screen prints 1,620 simplex sheets/hour or half that rate for duplex printing. It prints with quick-drying water-based inks using conventional coated or uncoated offset and inkjet substrates, including thin carton board, with an integrated postcoating process. The Equios digital workflow system uses a spot color editor to match the closest CMYK reproduction for specific spot colors.
One was recently installed at Brogle Druck, an integrated media company in Switzerland. It mainly uses Heidelberg Speedmaster offset-litho presses, but has an established digital strategy. Roger Brogle said the latest Truepress JetSX emulates offset quality, with a resolution up to 1,440 x 1,440 DPI and variable grayscale. ‘The fact that the press prints sheets up to 0.6mm thick was also special,’ adding that Brogle Druck is preparing for expansion into the packaging sector.
Developments like these underline the growing influence of sheet-fed digital printing for short-run packaging. Its growing appeal among offset-litho printers seeking new business opportunities is a newer phenomenon, but one that reflects the shifting of tectonic plates within the graphics industry. It also implies that finishing equipment suppliers have an opportunity to capitalize on the new opportunities it presents. It could be based on adapting existing systems, such as Esko’s Kongsberg XE series designed to handle small-format digital cutting and creasing.
Riviera Beverages
Riviera Beverages in southern California uses a Presstek 34 direct imaging (DI) press to print cut-and-stack labels in-house for customized bottled waters. Batches may include versioning for special events, such as weddings. Run lengths range from a few hundred to several thousand labels using a 0.05mm substrate from Exxon Mobile. To meet increased demand Riviera plans to upgrade to a 52 DI press fitted with Presstek’s energy-efficient ECO UV system.
The DI’s V-shaped central-impression design eliminates sheet transfers between units, so reducing substrate waste and make-ready times. The water and air-cooled lamps operate within a narrow waveband to reduce IR heat without ozone emissions. The presses give consistent color quality at 300 lpi, plus FM screening with minimal dot gain at 10,000 sheets/hour.
Ian Pollock, sales director of Presstek Europe, says plateless direct imaging is ideal for short runs of sheeted labels and folded cartons. ‘Presstek DI with ECO UV technology still allows the greatest range of substrates with minimal pre-treatment prior to printing. Toner systems have stock limitations and inkjet technology costs are still fairly high. This means inkjet is more suited to extra short print runs, as opposed to short-to-medium run lengths.’
Stay up to date
Subscribe to the free Label News newsletter and receive the latest content every week. We'll never share your email address.