Durst’s 510mm inkjet press takes on flexo
UV inkjet is now challenging flexography in terms of print quality and productivity. This was the main message from Durst’s recent open house event.
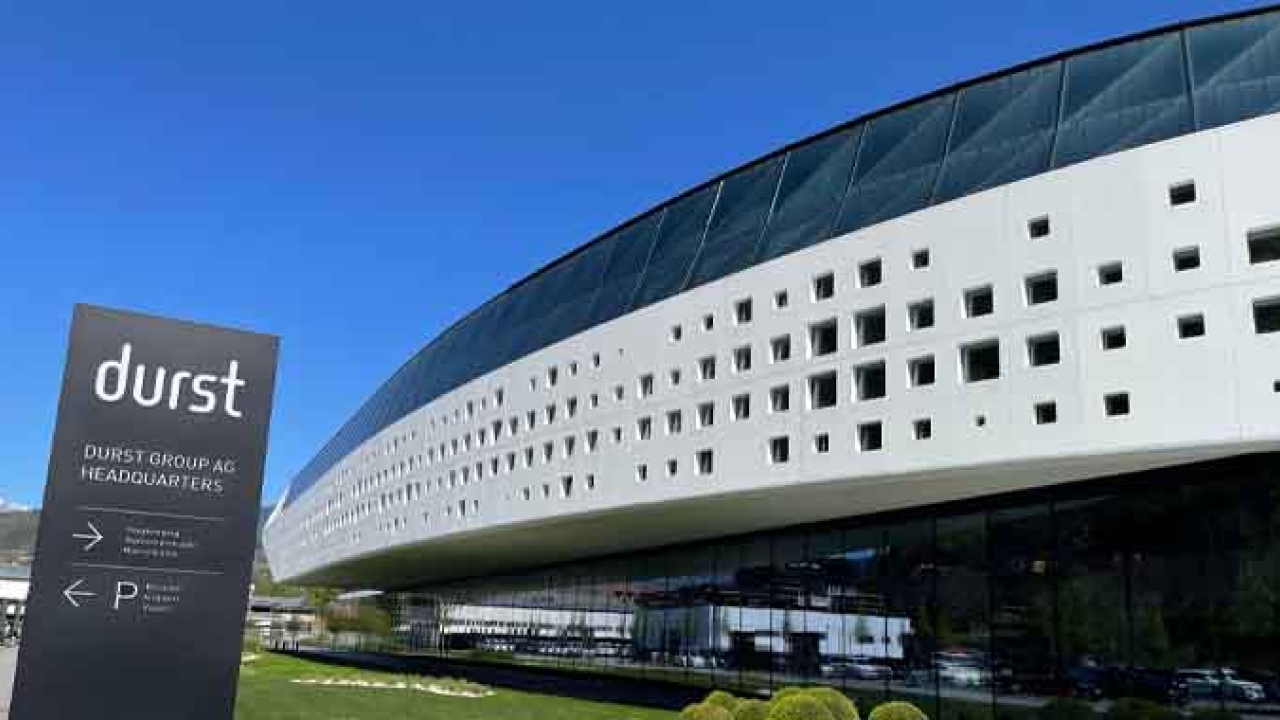
Durst’s Expo Label 2022 event, held at the company’s impressive headquarters in Brixen, Italy, gave visitors a chance to look at the company’s latest digital print technology.
The star of the show was without doubt the Tau RSCi, which takes UV inkjet print productivity to a level where it matches flexo on a wide range of medium and even long run work.
The RSCi press in the Brixen demo center is 510mm (20in) wide and was demonstrated printing at 100m/min in four colors. Press speed is 80m/min at full resolution and drops to 52m/min when printing white. A specialty white mode, achieving 80 percent opacity, is available at 40m/min.
The RSCi press is configurated with high productivity in mind, incorporating a jumbo winder, including roll lift, capable of taking rolls up to 1,106mm (43.5in) diameter. For maximum material flexibility the press is equipped with a chill roll as standard.
We have several customers which produce volume jobs on our presses. In 2021 we had customers printing in 12 months more than 2 million sqm on a single press
The RSCi at Brixen is configured with two flexo stations positioned before and after the digital print engine. Typical uses for the flexo stations would include first down white and post-print varnish, although there are also interesting applications for mixing spot flexo and UV inkjet inks to extend the viable run length. The first flexo unit could also be used to add a primer for more challenging materials, or on uncoated stocks where color matching is critical.
The flexo units are fitted with slide in/out carriages to aid loading and unloading of the ink pan, pick-up and anilox roller. Other features of the press include a hardware secure remote access facility and integrated inspection table. ABG demonstrated a 530mm-wide Digicon finishing line to match the 510mm web width of the Tau RSCi. The Digicon line incorporated varnish, lamination and high speed semi-rotary die-cutting and stripping. It can be configured for either in-line or near line operation.
Martin Leitner, product manager, Label & Flexible Packaging, Durst Group, believes that systems like the 510mm Tau RSCi mark a turning point for UV inkjet digital printing. ‘Digital is competing with flexo in terms of print quality – the Tau RSC print quality is as good or even better than flexo. Some customers compare it even with offset. Also, productivity-wise the presses are extremely competitive with low set-up times combined with high printing speeds. Keep in mind that the minimum printing speed on our presses is 40m/min, so the operator cannot go lower, which he is often doing on other technologies.’
Leitner says Durst already sees multiple customers substituting conventional flexo presses with UV inkjet technology. ‘To give you some numbers, we have several customers which really produce
volume jobs on our presses. In 2021 we had customers printing in 12 months more than 2 million sqm on a single press, or multiple customers with regularly daily productions between 20-25,000sqm,
so 60-75,000 linear meters a day.
‘I do not say that UV inkjet is today a full substitution for flexo. Each technology has its space and advantages, but in the past two years UV inkjet made huge steps forwards and provides customers
with more and more advantages.’
Entry-level
Two more UV inkjet presses were on demonstration, representing different steps on the Tau ladder.
The Tau 330 RSC E is Durst’s entry-level press, running at 52m/min, but with the ability to be field upgraded to the 8-color Tau 330 RSC running at 80m/min.
Although entry-level, the press shares key features with the most advanced of the Tau press series, including automated nozzle compensation based around an in-line camera. All the Tau machines print to a resolution of 1,200 x 1,200 DPI with 2 picoliter drop size using FujiFilm Dimatix Samba 3GL print heads.
Like its other stablemates, the RSC-E press allows either standard RSC UV inks or low migration (LM) inks to be used.
The next step up is the Tau 330 RSC, which runs at 80m/min (262ft/min) and includes the high opacity (80 percent) white mode, making the press particularly suitable for added value toiletries and cosmetics applications.
The press runs the extended gamut (CMYK+OGV) RSC ink set, but Durst’s tests demonstrate that up to 85 percent of the Pantone range can be achieved with just CMYK to a delta of under 2 (the quoted test was conducted on HermaPE label material). Using the full CMYK+OGV ink set allows up to 95 percent of the Pantone range to be hit.
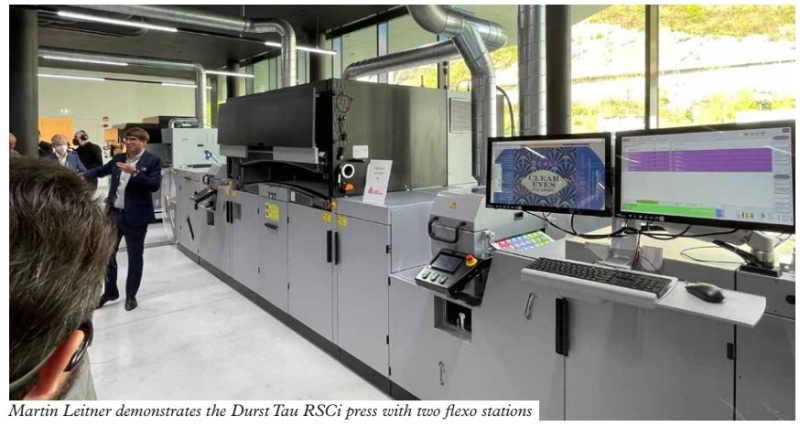
The RSC press at Brixen was demonstrated running low migration inks for food and pharma applications with an integrated nitrogen chamber. This guarantees 100 percent cure and zero odor generation by eliminating oxygen from the curing area.
Automation ecosystem
Automation is a key feature of efficient digital workflows, and Durst demonstrated its own Durst Workflow Label software ecosystem, along with a new tool, Durst Analytics. The latter allows multiple presses to be monitored remotely via a web-based dashboard, providing a wide range of production data including ink consumption and uptime, and including preventative maintenance functions.
Another part of this wider ecosystem is the Durst Smart Shop, which allows converters to integrate the press into B2C/B2B business workflows, all managed through a web-based user interface.
‘We have 40 people developing software across all the print segments we work in,’ says Martin Leitner. ‘So we can connect the press, workflow and color management and how data flows, all using automated hot folders.’
Available with the latest Durst Workflow Label + (v1.10) is a new feature called Save Ink, which uses intelligent color replacement algorithms to save an average of 9.5-12 percent of ink cost per job.
The Save Ink algorithm utilizes AI-assisted image analysis to change the original color combination in order to reduce ink consumption with minimal change (below delta 2) in visual appearance.
The amount of ink that can be saved depends on factors specific to each file. ‘We have analyzed more than 100 different real customer files,’ says Martin Leitner. ‘On average, cost savings of 12 percent have been achieved in a CMYK color configuration and 9.5 percent in CMYK+OGV configuration. There is no saving in white color.’
The Save Ink algorithm utilizes AI-assisted image analysis to change the original color combination in order to reduce ink consumption with minimal change in Martin Leitner demonstrates the Durst Tau RSCi press with two flexo stations visual appearance
Visually, files with Ink Save applied do not have any visible breaks in gradients. The only indication Ink Save has been used is a slight reduction in color saturation.
The real importance of Save Ink mode is when taken alongside the increasing productivity of Durst’s new press line, and particularly the RSCi. An RSCi press with integrated flexo units and Save Ink capability would allow converters to challenge flexography much further into medium-to-long run lengths.
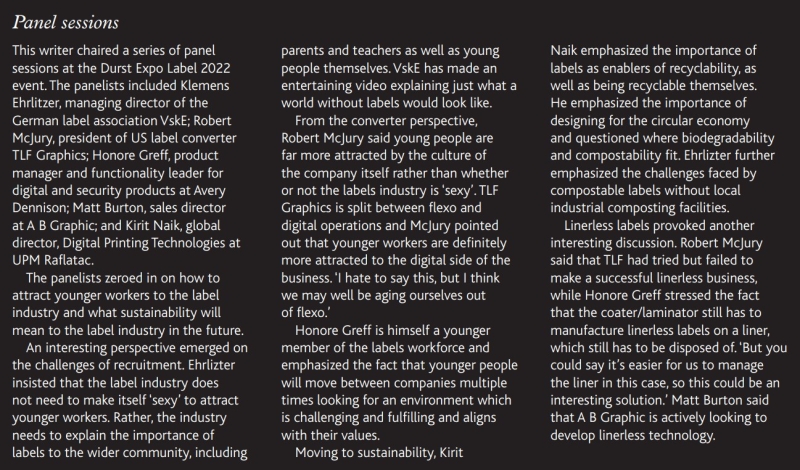
Stay up to date
Subscribe to the free Label News newsletter and receive the latest content every week. We'll never share your email address.