Heidelberg’s package printing promise
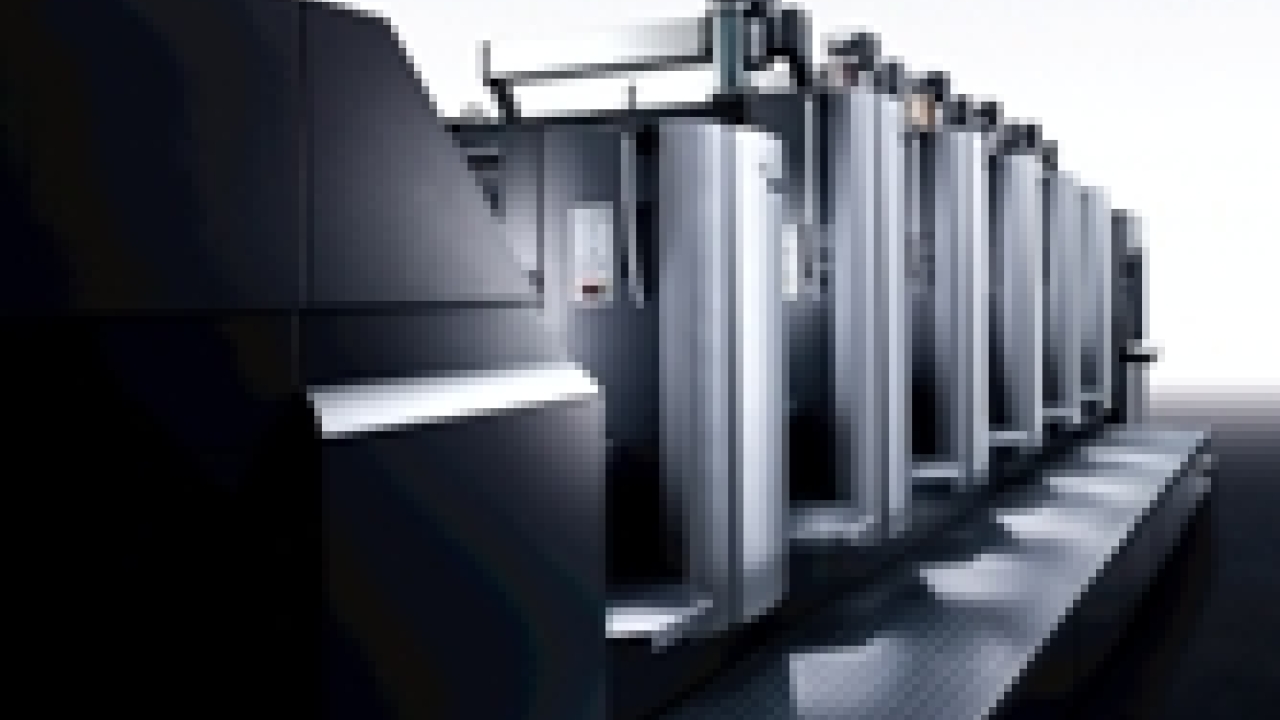
Packaging is seen as a core to Heidelberg’s future strategy and growth, and an area that will get plenty of attention under the HEI END banner at Drupa 2012 in Dusseldorf next May. Nick Coombes reports
As recently announced on the PPW website, Heidelberg has introduced its carbon balanced presses at a small price premium. Seen as a way of helping printers to help their more environmentally aware customers (and there are plenty of those on the high street and in the corporate world) to fulfill their sustainability requirements, the carbon used in the manufacture is calculated on a press specific basis, and certificates issued to show that the amount of carbon used has been offset by support of conservation organizations.
This is neither the time nor place to discuss the relative merits of "green" technology in the printing industry, but it certainly gives an indication of the political, if not environmental, pressure that brand owners and retail chains are under, that a manufacturer as large as Heidelberg is prepared, indeed convinced, to underwrite the time and effort, and therefore money, to quantify the eco-efficiency of its production techniques. Who else will follow?
Making its debut at the Dusseldorf expo will be Heidelberg’s latest 18,000-sheet per hour Speedmaster XL 105 perfector. Rated to offer an improvement in productivity of 15-20 percent overall, it offers converters the opportunity for double-sided carton printing. One has only to look at the relatively humble breakfast cereal box to realize the growth in demand for this type of two-sided application. Also on show at Drupa will be the Speedmaster CX 102. This high-spec press combines elements of the CD and XL technology, and has sold well, with more than 1,000 units finding customers since its launch 18 months ago.
Relief coating, cold foiling spot colors and Cristala design patterns are features that should be investigated at the show. Realizing the importance of these added value techniques led one leading German carton group to specify a unique Speedmaster XL 105, including the latest integrated FoilStar cold foil unit. The press allows new processes like blind and hot foil, relief and micro embossing, as well as foiling and high-gloss UV varnishing, which is occasionally a substitute for calendering. For the first time, these processes permit the in-line production of folding cartons with new high-brilliance metallic effects.
The technique draws attention to the graphics, text and logos, which can now be produced with metallic tones.
Inspection Control for product security, which allows printers to identify and remove faulty sheets, can now even spot a specific box error in multi-up work. This makes a huge saving in waste levels and lost money on a job. Heidelberg has now made it possible to fit Inspection Control onto the Diana X folder gluer as well as the Speedmaster press range. It can also be retro fitted to both. Still with security applications in mind, Heidelberg says it will unveil a 5080 dpi version of its Suprasetter A52/A75. The company is very strong in CtP (computer to plate), with more than 8,000 systems sold to date, of which more than half are Suprasetters. Drupa 2012 will see a new compact auto/dual cassette loader for the Suprasetter 105 unveiled, and a smaller processor to reduce chemistry and power consumption.
To maximize the performance of the press, the carton producer must have accurate, measured data supplied to the press, and automated set up and on-the-run adjustment. Heidelberg’s Prinect family, including workflow and spectral measurement devices, are constantly evolving so that lean manufacturing, color and even ecological factors, particularly waste, can be controlled.
Integration will be the buzzword for the Prinect packaging workflow at Drupa. It will include modules to cover CAD and one-up design, one-up editing, sheet layout and processing, printing and die cutting, and folder gluer applications. The benefits of workflow are well known by now: it speeds up make-ready, reduces waste and provides the company’s management team with the hard facts on which it can base sound business decisions for future investment. As one Heidelberg user commented to me recently when I quizzed him on the value of data flow: ‘If you don’t know where the problem is, how can you solve it?’
Heidelberg says it will be strengthening its MIS with a collaboration to develop products with Belgian specialist CERM. Packaging printers would also be well advised to take a look at the hot topic of Web2Print, for which Heidelberg has a co-operative arrangement with Pageflex Although the impact of this relationship management selling and work ganging tool is still predominantly in the commercial response print market, it is an interesting way of supporting, adding value and tying in customers more firmly at a time when old fashioned loyalty, or even cut throat pricing, doesn’t work.
According to Bernhard Schreier, CEO of Heidelberg: ‘The circumstances surrounding Drupa 2012 are exceptional because the industry is in a state of change, but we are ideally placed to offer valuable guidance and recommend the most appropriate solutions. In the current market and environment, trust and reliability are priorities for our customers. That is why we use our innovations to respond to customer queries that extend far beyond purely technical issues to, for example, which business models will be successful in the long run?’
Stay up to date
Subscribe to the free Label News newsletter and receive the latest content every week. We'll never share your email address.