HP Indigo 30000: An early adopter’s view
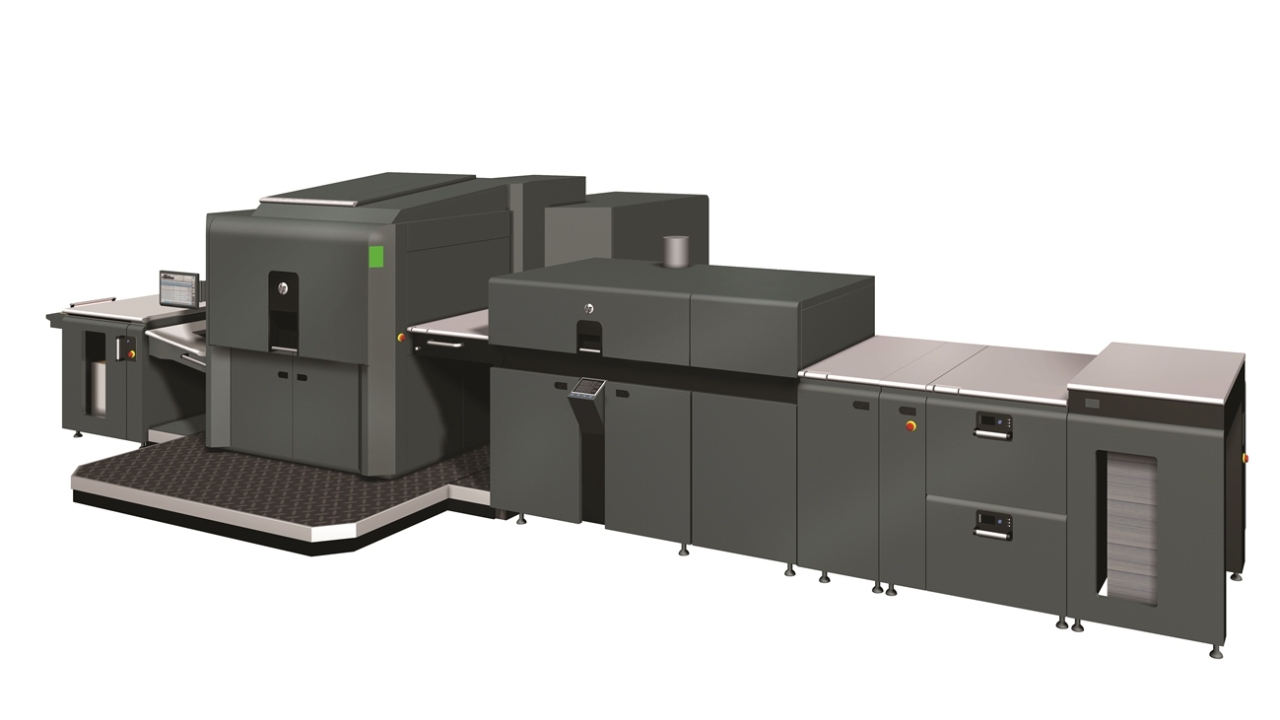
US printer Multi-Packaging Solutions has signed up to be one of the first to receive a new HP Indigo folding carton press. Danielle Jerschefske reports
Multi-Packaging Solutions (MPS) produces print and packaging, including folding cartons, labels, merchandising and special packaging for the cosmetics, healthcare, horticulture, media and consumer markets.
Headquartered in New York City, MPS has fourteen plants across the US and three facilities in Europe. The business is focused on investing in key technologies across all production areas to provide full service packaging management to multi-national clients.
Within its digital division, the packaging converter operates seventeen digital printing presses from various OEMs, including a 13in HP Indigo 6000 capable of producing folding cartons from roll stock up to 16 points thick.
The company has now taken the decision to extend its relationship with HP Indigo, and has signed up to become one of the first to receive its new 30000 model for printing folding cartons.
The new HP Indigo 30000 digital press offers a more robust design in a 29in (75cm) sheet-fed format capable of printing on material as thick as 24 points. It has seven printing stations that utilize HP Indigo’s proprietary ElectroInk technology.
Remaining consistent with the Indigo line of presses, the 30000 is equipped with Esko front-end management software and a Tresu iCoat 30000 unit for aqueous and UV spot coating.
MPS is still deciding on the facility location to house its latest investment, but expects the new HP Indigo 30000 to be installed by early 2014.
John Cote, vice-president of innovation and manufacturing technology at MPS, says: ‘This new HP Indigo press fills a void in high-quality production of folding cartons.
‘All of our customers have a need for smaller run items or other reasons for why digital makes sense beyond proofing and concept phases, such as serialization and SKU proliferation.
‘The quality of digital print continues to get closer to that of offset and the HP 30000 goes a long way toward closing the gap.’
While some conventional equipment can efficiently produce lower volumes of about 3,000 sheets, MPS explains that more often orders it receives are for only 500 to 800 sheets. ‘Using a 40in Heidelberg UV offset press to produce such low volumes is not ideal,’ says Cote. ‘Our operators would spend more time in make-ready, wasting more material than producing saleable product. This new Indigo press will allow us to effectively service this market gap.’
Increasingly too, the value chain is shifting in preference towards just-in-time delivery to improve inventory management and cash flow while reducing obsolescence. With digital print technology, lower volume orders of folding cartons, labels or any other printed packaging can be produced profitably and delivered on-demand.
Cote explains that MPS’s customers are ordering more frequently, on a monthly or weekly basis, which is not an easy need to manage using conventional printing equipment.
In servicing the healthcare market specifically, MPS is eager to gain the ability to print sequential number codes on carton stock. Cote says: ‘The emergence of serialization for track and trace purposes is massive and already integrated into many industries’ logistics chains.’
In 2004 the state of California passed ePedigree legislation requiring unit-level tracking of pharmaceutical products using serialized codes so to minimize the entrance of counterfeit products within the market. The medicine manufacturers will be responsible for including these codes (2D barcodes or RFID tags) on 50 percent of their products sold in California by 2015.
Come 2016, 100 percent of pharmaceutical products sold in California, which accounts for nine percent of the US market, will be required to have this traceability through packaging. It allows the possession of a particular product to be verified and reported.
Read more features from Packprint World here
Stay up to date
Subscribe to the free Label News newsletter and receive the latest content every week. We'll never share your email address.